Steel Markets
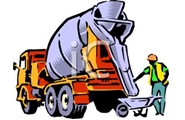
Tariffs Undermining Construction as Materials Prices Jump
Written by Sandy Williams
May 10, 2018
Construction costs are surging as tariffs drive prices up for a wide range of building materials, said a new analysis of Labor Department data by the Associated General Contractors of America. Firms are facing higher input prices that they are unable to pass along to customers.
“Contractors have started to boost the prices they charge, but they are falling further behind on the cost of materials they buy,” said the association’s chief economist, Ken Simonson. “This imbalance poses two risks—either contractors will suffer decreased profit margins or project owners with fixed budgets will cut back on the projects they undertake.”
The producer price index for construction inputs rose 1.0 percent in April and 6.4 percent in the last 12 months, for the steepest year-over-year increase since 2011, noted AGC. The index measuring what contractors charge for construction of nonresidential buildings, like schools, offices and warehouses, rose 1.1 percent from March and 4.2 percent year-over-year.
“The gap between the 6.4 percent rise in the cost of construction goods and the 4.2 percent increase in prices charged is ominous,” Simonson observed. “Unfortunately, the gap may widen further if tariffs or quotas push up costs further for the many steel, aluminum and wood products used in construction.”
The April producer price index jumped by 11.9 percent in the last 12 months for aluminum mill shapes, 11.0 percent for lumber and plywood, and 7.4 percent for steel mill products. Other construction inputs that rose in April include: diesel fuel, 41.6 percent; copper and brass mill shapes, 10.5 percent; gypsum products, 7.5 percent; ready-mix concrete, 6.9 percent; and truck transportation of freight, 6.0 percent.
As metal and lumber prices continue to surge, contractors will need to charge more, which may result in projects lost or delayed.
“The new tariffs have the potential to undermine many of the benefits of the president’s recently enacted tax and regulatory reforms,” said Stephen E. Sandherr, the association’s chief executive officer. “Instead of investing their tax savings in new personnel and equipment, many firms are being forced to use them to cover increasing steel and aluminum costs.”
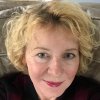
Sandy Williams
Read more from Sandy WilliamsLatest in Steel Markets
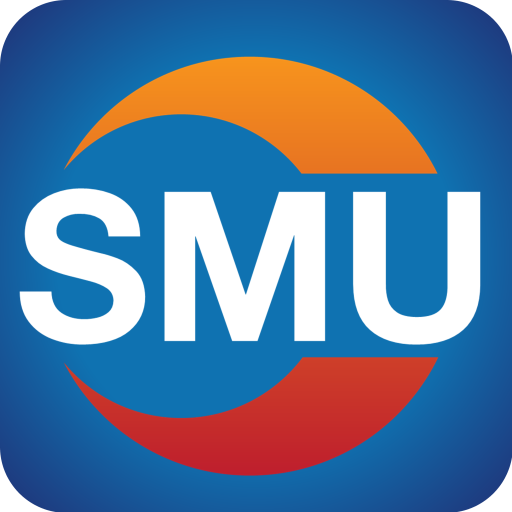
SMU Week in Review: September 1-5
Here are highlights of what’s happened this past week and a few upcoming things to keep an eye on.
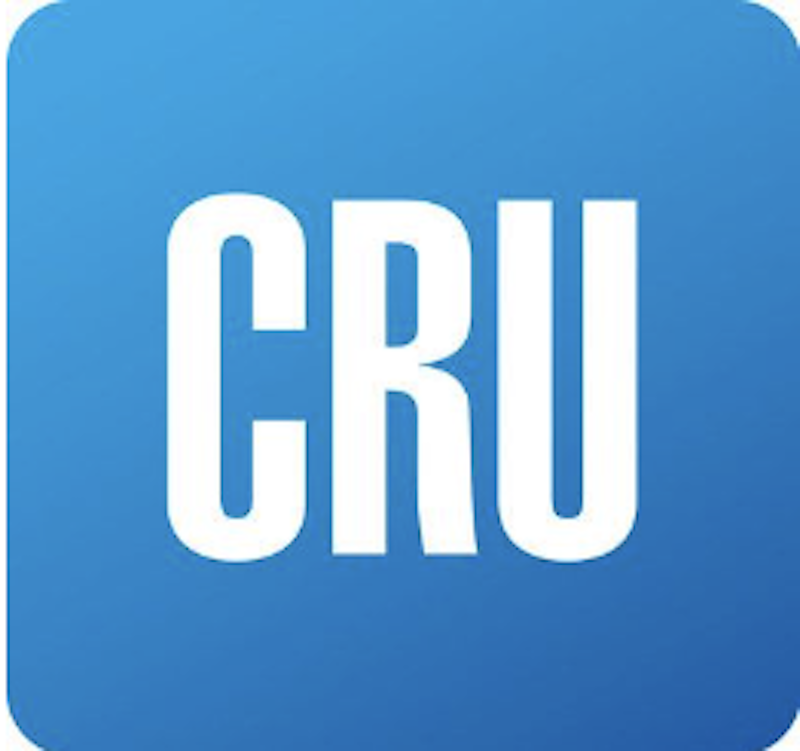
CRU: US longs market holds steady despite tariff pressures
he US longs market remained stable this month despite ongoing challenges from tariff-impacted imports, even as end-use demand was relatively unchanged and scrap prices held flat in August.
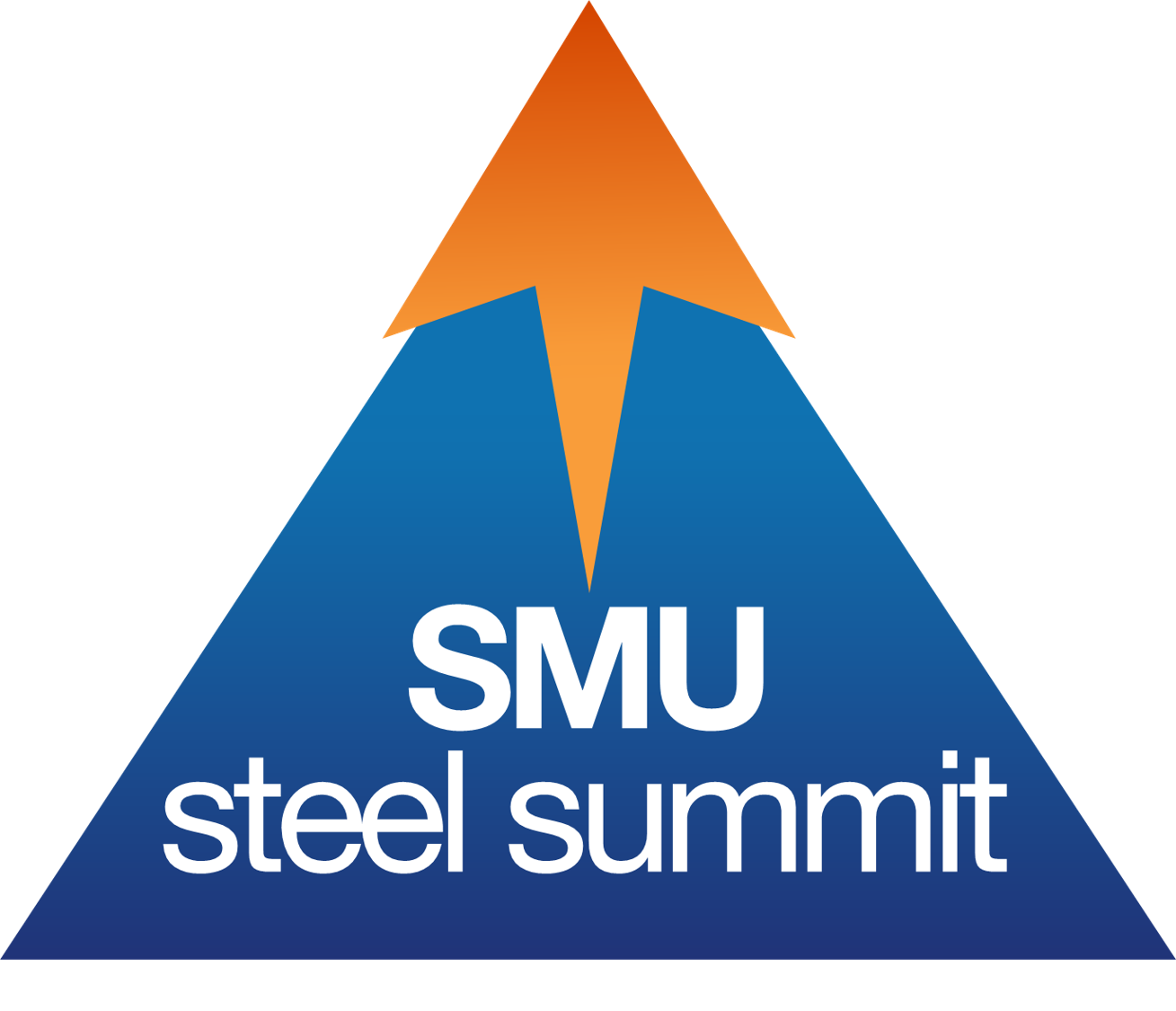
Steel Summit: Schneider sees SDI ‘on the edge of a very good run’
Steel Dynamics Inc. (SDI) President and Chief Operating Officer, Barry Schneider, remains bullish about the Fort Wayne, Ind.-based steelmaker’s position in the current market.
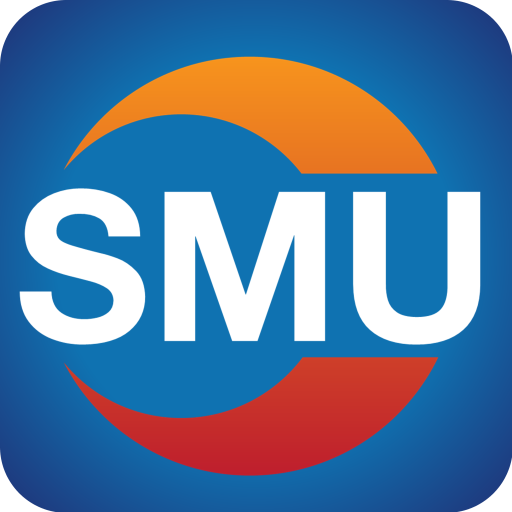
Sheet market participants say sales still in a slump
Across the US and throughout the steel supply chain, market participants are reporting another painfully quiet week for hot-rolled (HR) coil sales.
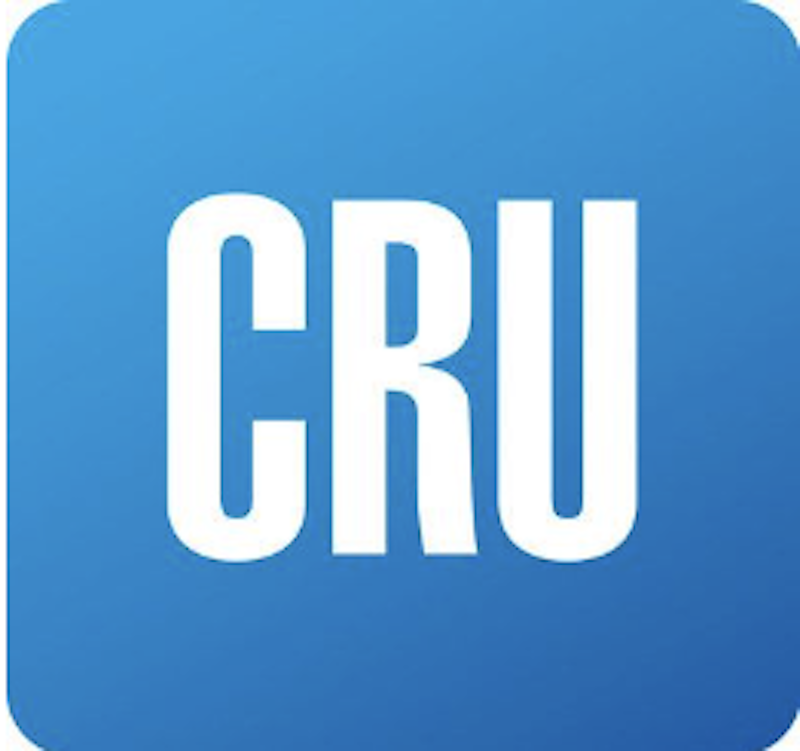
CRU: Lower sheet prices have pulled back demand for imports
Domestic sheet prices in the US remained under pressure, limiting interest in imports, while domestic prices for longs products continued to rise.