Steel Products Prices North America
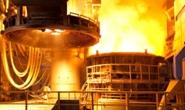
The Theoretical Marginal Cost to Produce Steel
Written by John Packard
February 8, 2016
We were reminded recently of an article we produced on February 24, 2015 regarding our theoretical marginal cost of Steel Making (cost will vary by mill and not included in our formula is any adjustment for running at less than 70 percent capacity levels, SA&G are not included, etc.). We were asked if we could update the graphic used, which is the same graphic our metallurgist uses during our Steel 101 workshop. Here is a copy of the graphic used in that article:
Steel Market Update conducted one of our Steel 101 workshops in January so I asked John Eckstein to update the graphic with some of the latest data (as of the end of January 2016) so we could present it again to our readers.
Again, it is important to note that this is an exercise only and not necessarily a true tabulation of any specific steel mill’s cost to produce (don’t run out and try to beat up your mill rep looking for price reductions based on this exercise).
There is no clear agreement either by the analysts, metallurgists or consultants as to exactly what it cost each mill to produce a hot band. The closest we have heard a mill to reporting their cost to produce was Steel Dynamics (Keith Busse as CEO) who mentioned a number of years ago that he used prime scrap plus $150 per ton. If that is still correct with prime grades going for $180-$200 per ton we would get a HRC cost of $330-$350 per ton. This is more than the $281 per ton shown in our theoretical model above which does not include overhead, which could well explain the $49-$69 per ton difference. When we did this exercise one year ago the variance was $69 per ton….
Our model does not take into consideration other costs such as zinc and aluminum which would impact coating costs. Zinc, for example, was trading at approximately $0.97 per pound one year ago versus $0.75 per pound today (LME prices and does not include premiums that mills must pay in order to get material to their plants).One of the things that is not mentioned in the calculations we provided is they are based on running the mill to peak capacity and with the right product mix in order to be the most efficient. We believe the flat rolled mills are running somewhere around 60 percent to 75 percent capacity at this time (depending on the mill).
As mentioned above, we have the issue of overhead (people, equipment, R&D, inventory, depreciation, etc.) and what is a fair return on investment for a steel mill operation? Whatever that number is, it is not reflected in our calculation (thus our cost is theoretical).

John Packard
Read more from John PackardLatest in Steel Products Prices North America
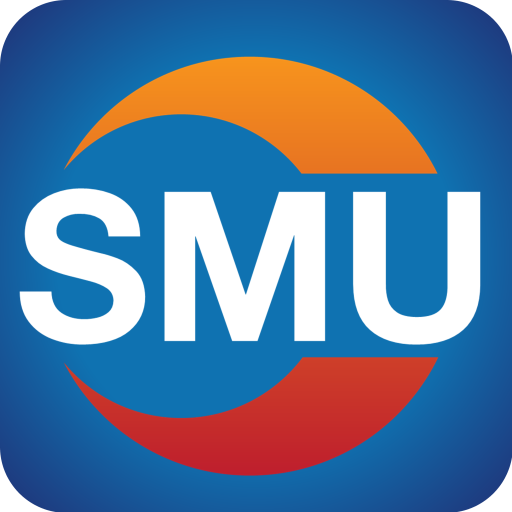
SMU Price Ranges: Sheet and plate steady ahead of Independence Day
Sheet and plate prices were little changed in the shortened week ahead of Independence Day, according to SMU’s latest check of the market.
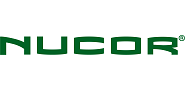
Nucor maintains plate prices, opens August order book
Nucor aims to keep plate prices flat again with the opening of its August order book.
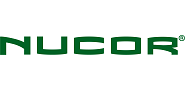
Nucor CSP remains level at $900/ton
Nucor maintained its weekly list price for hot-rolled (HR) coil this week, following two consecutive increases.
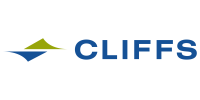
Cliffs raises prices, seeks $950/ton for July spot HR
Cleveland-Cliffs plans to increase prices for hot-rolled (HR) coil to $950 per short ton (st) with the opening of its July spot order book. The Cleveland-based steelmaker said the price hike was effective immediately in a letter to customers dated Monday.
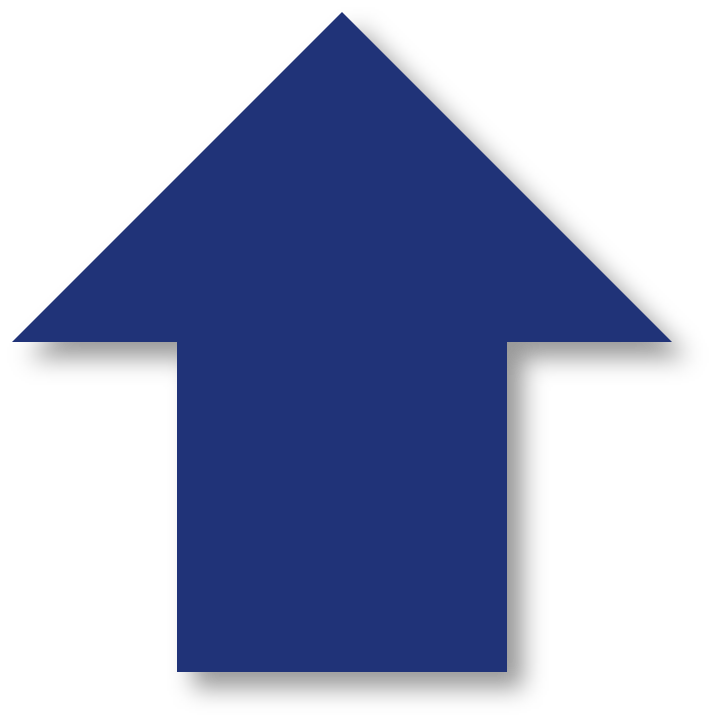
HRC vs. prime scrap spread widens in June
The price spread between HRC and prime scrap widened in June.