Economy
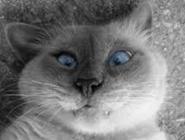
Researchers Claim ‘Super Steel’ Solves Strength-Ductility Tradeoff
Written by Tim Triplett
August 25, 2017
Researchers in Asia claim they have developed a new way to make steel that offers a high degree of strength without sacrificing ductility, creating a strong but formable material that could prove useful in the production of lighter, more fuel-efficient vehicles, among many other applications.
Typically, making steel stronger decreases its formability. The Hong Kong-Beijing-Taiwan mechanical engineering team led by Dr. Huang Mingxin from the University of Hong Kong says it has developed a “Super Steel” that addresses this strength-ductility trade-off.
In their paper published in the journal Science, the research team describes the process used to make the new type of steel. It employs a new deformed and partitioned (D&P) process that involves cold rolling followed by low-temperature annealing. Details of the process are confidential. The material that results is made with 0.47 percent carbon, 10 percent manganese, 0.7 percent vanadium and 2.0 percent aluminum. Metastable austenite grains embedded during the process helps the steel retain ductility.
The “breakthrough” material offers a yield strength of 2.2 GPa and 16 percent uniform elongation, which would make it the best in its class. Compared with widely used automotive steels, such as DP780 and Q&P980, as well as maraging steel used in aerospace and defense, the D&P steel demonstrates a much higher yield strength while maintaining much better ductility, the researchers claim.
In addition to offering improved physical properties, the material can be produced at just one-fifth the cost of steel currently used in many aerospace and defense applications. The new technique utilizes low-cost raw materials and conventional industrial processes, which gives it great potential for industrial mass production, say its developers.
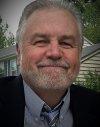
Tim Triplett
Read more from Tim TriplettLatest in Economy
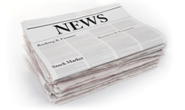
Steel groups welcome passage of budget bill
Steel trade groups praised the passage of the Big Beautiful Bill (BBB) in Congress on Thursday.
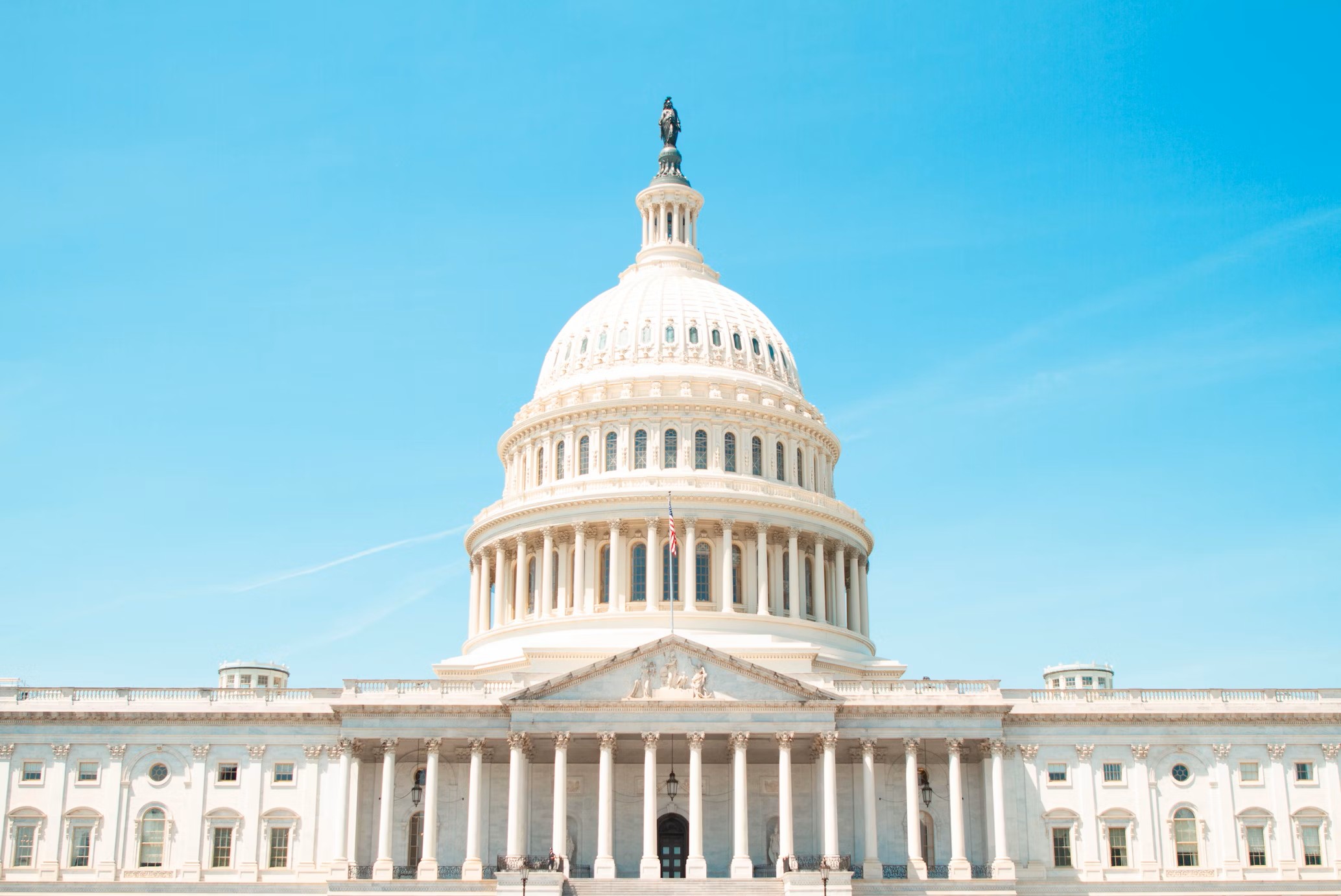
Industry groups praise Senate for passing tax and budget bill
The Steel Manufacturers Association and the American Iron and Steel Institute applauded the tax provisions included in the Senate's tax and budget reconciliation bill.
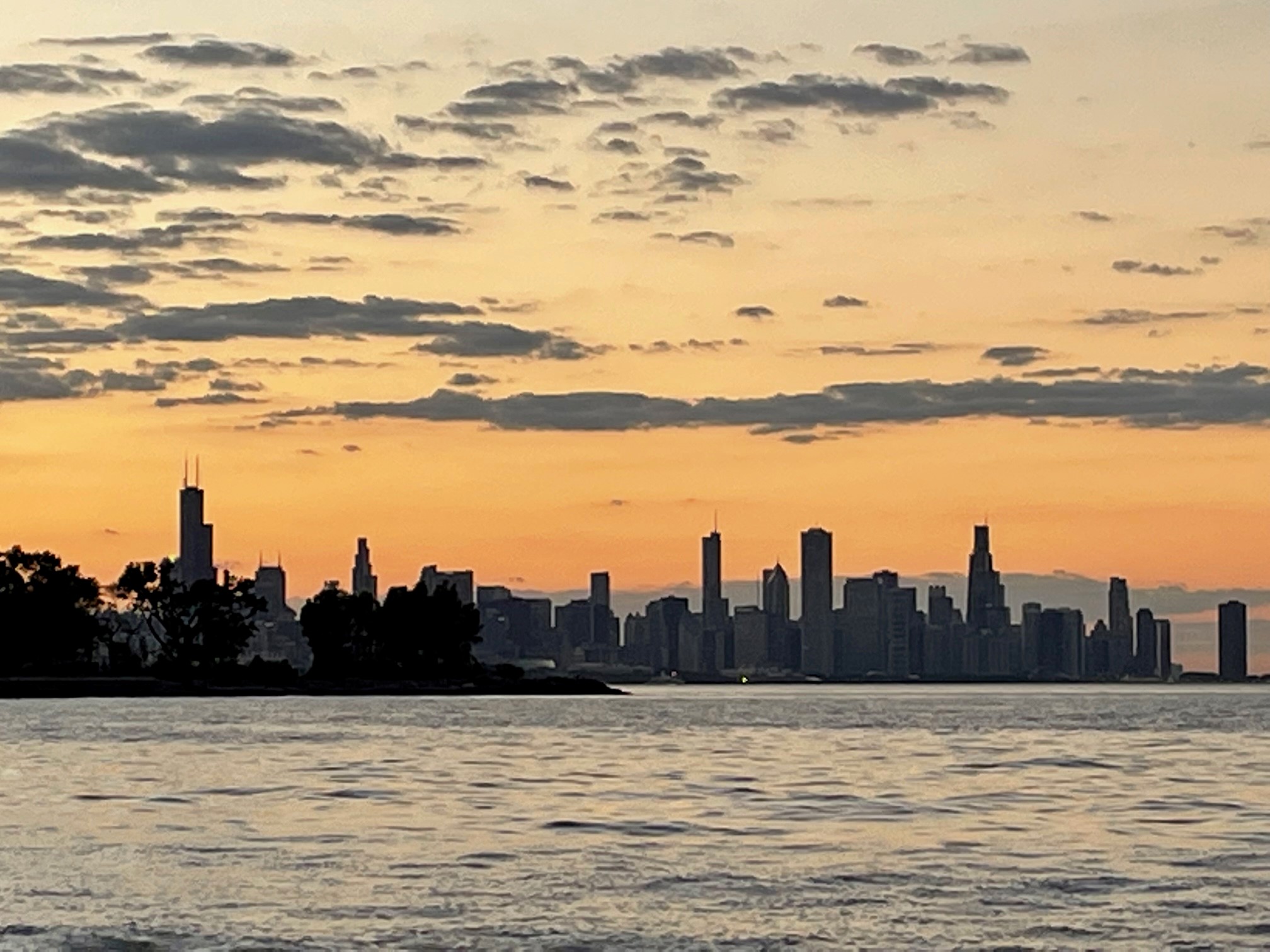
Chicago PMI dips 0.1 points in June
The Chicago Purchasing Managers Index (PMI) slipped 0.1 points to 40.4 points, in June.
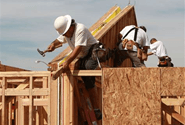
Multi-family pullback drives housing starts to 5-year low in May
US housing starts tumbled in May to a five-year low, according to figures recently released by the US Census Bureau.
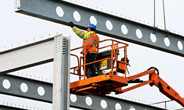
Architecture firms still struggling, ABI data shows
Architecture firms reported a modest improvement in billings through May, yet business conditions remained soft, according to the latest Architecture Billings Index (ABI) release from the American Institute of Architects (AIA) and Deltek.