Steel Mills
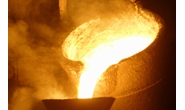
Green Steelmaking: New Technology High on Hydrogen
Written by Tim Triplett
December 10, 2019
Editor’s note: Steel is the largest producer of global industrial CO2 emissions. So, as stemming climate change takes on ever greater urgency, steelmakers are challenged to find production methods that emit fewer greenhouse gases. New technologies in development range from improving process efficiency to carbon capture to using hydrogen instead of coal as fuel. Following is one in a periodic series of articles to come on environmental innovations in steelmaking.
Using Hydrogen in Steel Production
Steel producers in Europe are testing the feasibility of using renewable hydrogen to replace fossil fuels in steel manufacturing.
A conventional blast furnace uses around 300 kilograms of coking coal (661 pounds) and 200 kilograms (449 pounds) of pulverized coal to produce one metric ton of pig iron. Coke is injected as an additional reducing agent into the bottom of the blast furnace where it reacts with oxygen in the iron ore. The coal process results in the production of carbon dioxide, whereas the hydrogen process produces water vapor. The reduction of CO2 emissions by using hydrogen vs. coal is significant.
In November, Thyssenkrupp’s Steel Europe Premal Desai successfully injected hydrogen into one of the 28 tuyeres, or nozzles, used to feed coal to the blast furnace. The experiment proved that hydrogen can fuel the steelmaking process while reducing emissions by about 20 percent.
Thyssenkrupp Steel plans to gradually extend the use of hydrogen to all 28 tuyeres on BF 9 and power three blast furnace completely by hydrogen by 2023.
Thyssenkrupp produces around 12 million metric tons of crude steel annually and has committed to achieving a 30 percent reduction in CO2 emissions by 2030. The company hopes to be carbon neutral by 2050.
In March 2019, ArcelorMittal launched a pilot project in Hamburg, Germany, to test using hydrogen in Direct Reduced Iron (DRI) production. In DRI furnaces fed with natural gas, about 50 percent of the reaction comes from hydrogen and the rest from carbon monoxide. Technology development should eventually allow use of 100 percent hydrogen instead of natural gas. The Hamburg project will test the feasibility of hydrogen steelmaking on an industrial scale, with an annual production of 100,000 metric tons of steel.
The process of reducing iron ore with hydrogen will first be tested using hydrogen generated from gas separation from the waste gas of the existing plant. The resulting hydrogen gas will have a purity of more than 95 percent. Eventually the plant should be able to run on “green” hydrogen once it is available in sufficient quantities at affordable prices, said ArcelorMittal.
Making “Green” Hydrogen
Hydrogen itself needs to be “green” in order for steel manufacturers to make environmentally friendly steel. Hydrogen can be produced by several methods, the most common being steam methane reforming or SMR. In the SMR process, methane found in natural gas reacts with steam, producing hydrogen and carbon monoxide. The carbon monoxide undergoes further reactions creating more hydrogen as well as undesirable carbon dioxide.
A greener version is created by electrolysis, where water is split into hydrogen and oxygen using electricity. Of course, for a net environmental benefit, the electricity needs to be produced by renewable sources as well, such as wind and solar energy.
The H2FUTURE project, funded by the European Union and partnered by Voestalpine, VERBUND, Siemens and others, has commenced operations on the world’s largest CO2-neutral hydrogen production plant in Linz, Austria. The 6 MW facility uses a Siemens Silyzer 300 proton exchange membrane (PEM) electrolysis system that splits water into its constituent parts, hydrogen and oxygen. The project hopes to determine whether the technology to produce green hydrogen is suitable for use on an industrial scale.
Voestalpine is currently investigating the practicality of using a hybrid technology to bridge between the existing coke/coal-based blast furnace route and electric arc furnaces powered with green electricity partly generated using green hydrogen. If economically feasible, this option could reduce the Group’s CO2 emissions by about one-third between 2030 and 2035. Over the long-term, Voestalpine plans to gradually increase the use of green hydrogen in the steel production process, for an 80 percent reduction in CO2 emissions by 2050.
“We have set ourselves a clear goal of greater direct avoidance of CO2 emissions in steel manufacturing over the coming years,” said Voestalpine AG Chairman Herbert Eibensteiner. “With the start of operations at the world’s largest hydrogen pilot plant at our site in Linz, we have succeeded in taking a significant step towards driving this technological transformation.”
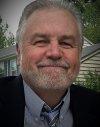
Tim Triplett
Read more from Tim TriplettLatest in Steel Mills
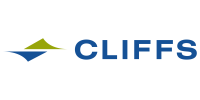
Cliffs idles Steelton, Riverdale, and Conshohocken operations
Cliffs has idled facilities in Riverdale, Ill., and Conshohocken and Steelton, Pa.
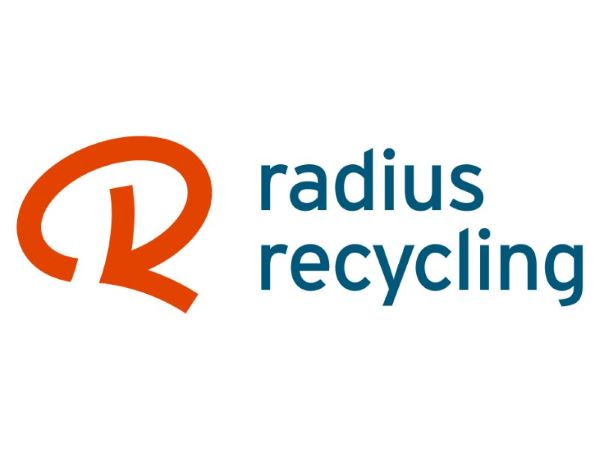
Radius loss narrows, volumes climb in ‘healthy’ West Coast market
Stronger steel demand in the Western US, rising scrap flows, and improved rolling mill utilization drove sequential gains for Portland, Ore.-based Radius Recycling.
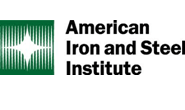
AISI: Raw steel production backs off multi-year high
US raw steel output edged lower last week after hitting a multi-year high in mid-June, according to the American Iron and Steel Institute (AISI).
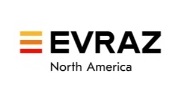
Private equity firm Atlas Holdings to acquire Evraz North America
Atlas Holdings said it has signed a definitive agreement to acquire Evraz North America (Evraz NA). The Greenwich, Conn.-based private equity firm said it expects the deal for the Chicago-based steelmaker to close in the second quarter of 2025 subject to various closing condition.
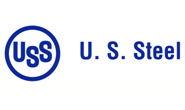
Granite City Works must remain open and other terms of the Nippon-USS deal
SEC documents also name Trump specifically as having veto power certain decisions are part of the “Golden Share” provision.