Economy
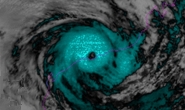
Global Steel Industry Tackles “Decarb” Challenge
Written by Tim Triplett
February 2, 2020
As advanced as steelmaking has become, producing steel is still an inherently carbon- and energy-intensive process. Steel mills in the United States and the rest of the world find themselves in the crosshairs of the many environmental and political groups now calling for dramatic steps to reduce harmful air emissions and slow the pace of climate change. With their own best interests in mind, as well as those of the planet, steel companies are spending millions to research and develop new technologies with the lofty goal of someday “decarbonizing” steel, and perhaps gaining a marketing advantage along the way.
Steelmakers around the world produced nearly 1.9 billion metric tons in 2019 in a process that transforms iron ore and coking coal or recycled scrap into new metal by applying enormous amounts of heat. The process emits vast volumes of carbon dioxide, the primary greenhouse gas that is warming the planet and changing its climate. The World Steel Association estimates 1.82 metric tons of CO2 were emitted for every ton of steel produced in 2018. The steel industry generates 7-9 percent of all direct emissions from the global use of fossil fuel.
To address the problem will require incremental changes in how steel is made and, hopefully, some new breakthrough technologies in research labs around the world. Steel industry trade groups are banding together to help their members share some of the cost of this burdensome R&D. Among them is the American Iron and Steel Institute (AISI) based in Washington, D.C.
AISI is quick to point out that the steel industry in the United States has reduced its energy intensity by 35 percent and CO2 emissions intensity by 37 percent per ton of steel shipped since 1990. The domestic steel sector reduced total air emissions by nearly 80 percent in the 20 years from 1996 to 2016. Much of that progress can be attributed to the proliferation of minimills and their use of electric arc furnaces to remelt steel scrap. Minimills, which now account for roughly two-thirds of annual steel production in the U.S., have displaced much of the volume from the higher polluting integrated steel process.
The steel industry also has contributed to a better environment indirectly. Its development of advanced high-strength steels is helping the auto industry reduce the weight of cars and trucks, increasing their fuel economy and reducing tailpipe emissions.
AISI also points to peer-reviewed studies offering a life cycle analysis of steel versus other materials, notably aluminum, and maintains that if the environmental impact of the energy needed to produce aluminum is taken into account, steel offers a higher net benefit. “The sustainability of steel products is superior to competing materials and minimizes environmental impact when measured through the entire life cycle,” AISI contends (while the aluminum industry offers its own studies that claim just the opposite).
The steel industry in the U.S. does a better job of limiting harmful emissions than mills in other countries, the trade association adds, referring to a study comparing hot-dip galvanized steel coils produced in North America to the same product produced in China and shipped to the North American market. The study found that the coils sourced from China added nearly 50 percent more GHG emissions to the environment.
Most mills have their own research programs in the works, but AISI assists by sponsoring collaborative R&D projects, which helps reduce duplicated effort and expense. “With AISI’s support they are able to take on higher cost, higher risk projects and share the burden across multiple companies,” said Mike Sortwell, senior director of technology for AISI. Companies that agree to participate and help fund each project get the findings of the research to use in their own R&D.
Currently under way is a study on advanced measurement technology. The goal is to develop a new sensor that can withstand the high heat of steelmaking and measure ladle temperatures continuously rather than periodically. More precise temperature readings will allow more precise control of the energy put into the steelmaking process. “It’s a way to refine a century-old process by adding some new-age technology,” said Sortwell.
Also in the works are plans to move forward with a pilot plant that will use a new flash ironmaking process developed in conjunction with the University of Utah. “It uses a different type of reduction process to greatly eliminate the amount of CO2 produced, and other emissions as well,” said Sortwell. “This was about a $12 million project on some really groundbreaking technology.”
High-performance computing is a tool showing promise. With access to supercomputers, AISI members can use diagnostic programs that normally take 20 hours and run them in 20 minutes to improve their processes and make their mills more efficient.
Carbon Capture and Storage is yet another approach that is making the move from the lab to the field. The world’s first commercial-scale industrial CCS project is reportedly in operation in Abu Dhabi, capturing carbon dioxide emissions from the Emirates Steel Plant in Musaffah before they get into the atmosphere.
As the issue of climate change takes on greater urgency, steelmakers are feeling more pressure from customers to reduce their emissions. Mills are beginning to see their environmental credentials as a marketing opportunity. The fuel source for the electricity used by the mill goes a long way in determining the greenhouse gas footprint of the mill itself. Nucor, for example, says its new micromill in Sedalia, Mo., will be the first U.S. steel plant to run on wind energy. SSAB claims it will be the first to market with “fossil free steel” as soon as 2026, using its new Hybrit process, which replaces coking coal with hydrogen, among other innovations.
As encouraging as these developments sound, there is no magic pill to completely cure steelmaking. “It will take breakthrough technology to meet a lot of the goals you hear bandied about both legislatively and regulatorily across the globe,” said Brett Smith, senior director of government relations for AISI. “The production of steel is energy and carbon intensive by nature. There is no big technology change on the horizon that can be put in place in 2-5 years. It’s a longer-term effort.”
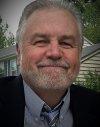
Tim Triplett
Read more from Tim TriplettLatest in Economy
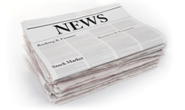
Steel groups welcome passage of budget bill
Steel trade groups praised the passage of the Big Beautiful Bill (BBB) in Congress on Thursday.
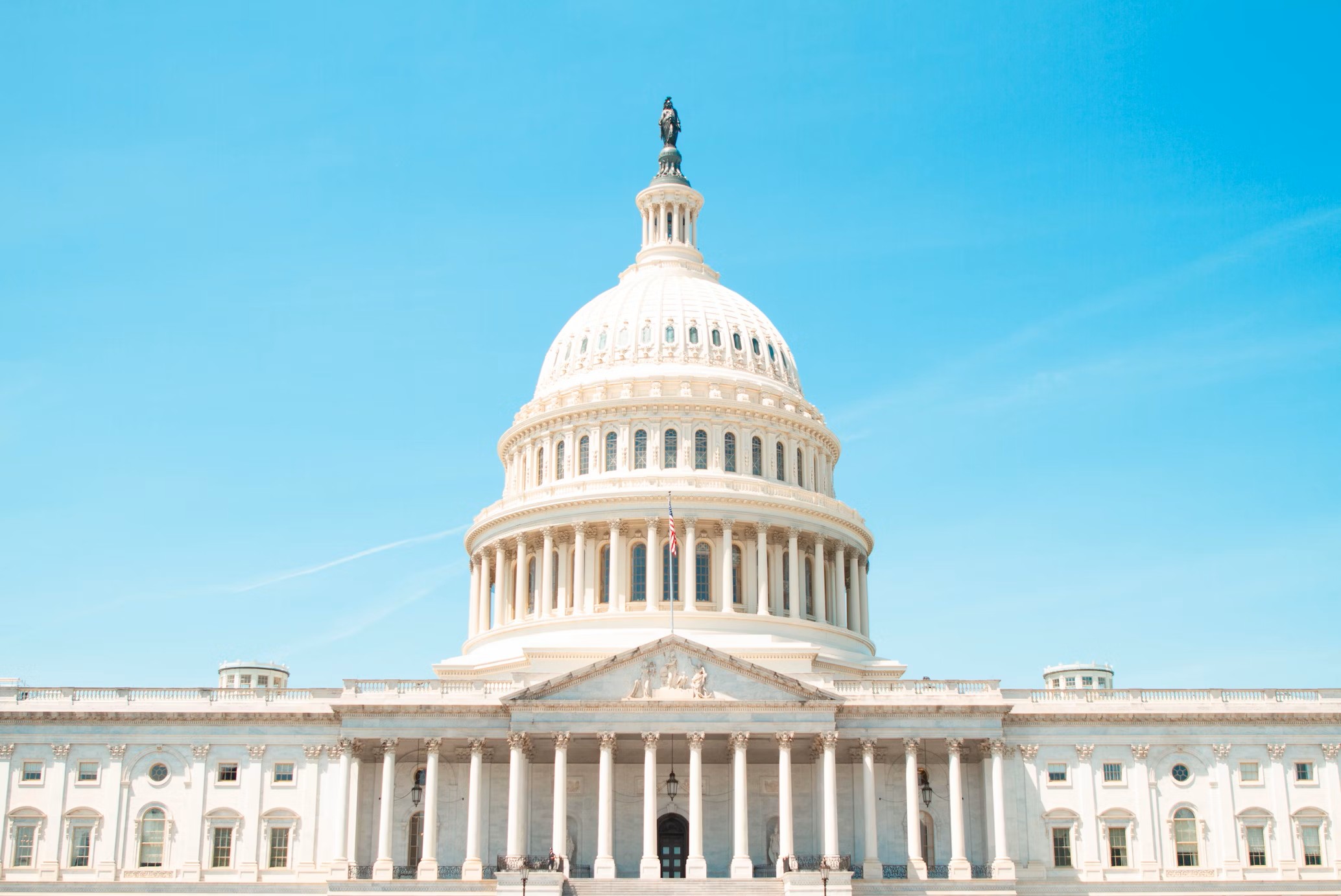
Industry groups praise Senate for passing tax and budget bill
The Steel Manufacturers Association and the American Iron and Steel Institute applauded the tax provisions included in the Senate's tax and budget reconciliation bill.
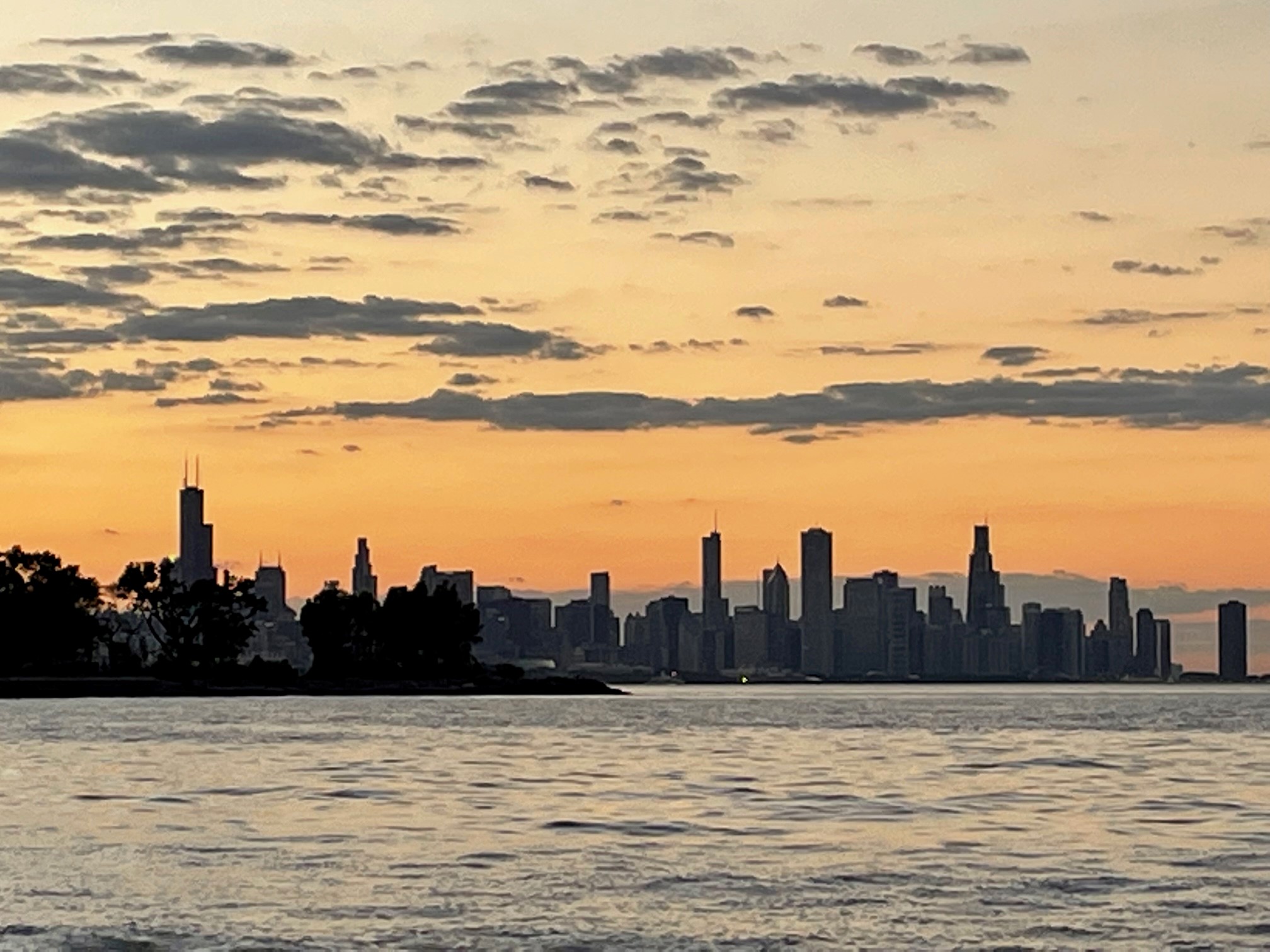
Chicago PMI dips 0.1 points in June
The Chicago Purchasing Managers Index (PMI) slipped 0.1 points to 40.4 points, in June.
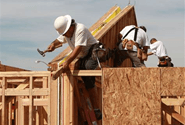
Multi-family pullback drives housing starts to 5-year low in May
US housing starts tumbled in May to a five-year low, according to figures recently released by the US Census Bureau.
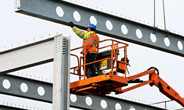
Architecture firms still struggling, ABI data shows
Architecture firms reported a modest improvement in billings through May, yet business conditions remained soft, according to the latest Architecture Billings Index (ABI) release from the American Institute of Architects (AIA) and Deltek.