Steel Products Prices North America
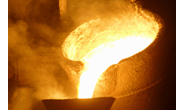
Competitive Dynamics Changing in the Pig Iron Market?
Written by Tim Triplett
February 2, 2021
As lower-emission electric arc furnace (EAF) mills become the predominant steelmaking method in the United States and other parts of the world, demand for pig iron, used to dilute the inclusions in melted scrap, will only grow. This trend has fueled speculation that integrated producers in the U.S. may repurpose idled blast furnaces for commercial pig iron production. Which raises a competitive question: Would EAF mills be reluctant to buy pig iron, and become reliant, on a competitor?
Steve Miller, an industry veteran and periodic contributor to Steel Market Update, offers the following perspective on the global pig iron market:
“First of all, the reason there is so much merchant pig iron production in Russia and Ukraine is because their mills had outdated cold ends. So, they started to make and sell iron units when the Iron Curtain fell and they were permitted to trade with the U.S. Over the years, they have gradually started to update their rolling and casting equipment, which has resulted in more retained hot metal.
“There is still significant cold pig iron generation in the CIS, but the Western mills have always worried about the reliability of this supply. Hence, the investment in mill-owned DRI production by the domestic minimills.
“In Brazil, pig iron is more like a national crop. However, the costs of the raw materials needed to make pig iron there are enormous. For one thing, they are dependent on Vale for iron ore, which they have to buy at the world price. They also have significant transportation and warehousing costs. The cost and availability of charcoal is erratic. Plus they are always under pressure due to rain forest destruction and poor labor conditions at the charcoal pits.
“So, the sad truth about the Brazilian pig iron industry is the only way they can make any money, selling to a steel industry that has cyclical phases, is to rely on the currency value of the U.S. dollar/euro versus the Brazilian real. They basically get paid in advance by U.S. buyers in dollars, but buy their raw materials and pay their labor in Brazilian reals. A number of producers went by the wayside during times where the dollar was weak.
“Given all of these risks to long-term supply for U.S. pig iron users, it’s a wonder that domestic mills haven’t tried to make their own previously. In fact, it has been attempted at least four times in the last 25 years. In the recent past, Bethlehem Steel produced basic pig iron at the Sparrows Point plant for almost 25 years before the mill was closed. AK Steel-Ashland in Kentucky briefly made pig iron in the late 1990s, but terminated for reasons unknown. About the same time, U.S. Steel/Kobe in Lorain, Ohio, also was producing pig iron until business conditions forced the closure of one of their blast furnaces and constrained the amount of ‘hot metal’ available for the pig iron caster. Finally, the one remaining producer in the U.S. today is Cleveland-Cliffs in East Chicago, Ind., formerly Inland Steel.
“So, with this backdrop, there is speculation that either U.S. Steel or other Cleveland-Cliffs integrated mills may start to produce merchant pig iron for use domestically. What would this do to the pig iron market in the U.S. and other consuming nations?
“That depends on several factors. Since CLF and USS are both integrated mills, they are in competition with the EAF minimills that produce flat-rolled steel and need pig iron to dilute the copper and other alloys in scrap. Will they sell to these competitors? It should be noted that both these corporations now possess EAF-based steelmaking assets of their own. CLF is also ready to produce hot-briquetted iron (HBI) at its Toledo, Ohio, installation. Would they want to make merchant pig iron to compete with their own product at this stage?
“There are internal usages for cold pig iron within these large organizations. Whether they sell to the general marketplace or just supply their own needs, it will have an effect on the gross amount of pig iron that the U.S. needs to import. When the Bethlehem pig iron caster was operational, the 20,000-40,000 tons per month of production had very little effect on the price of imported pig iron. The U.S. is a 5-6 million tons-per-year market. I believe things will not be affected too noticeably unless both USS and CLF decide to both produce pig iron.
“We are now hearing that Stelco’s Nanticoke plant on Lake Erie has installed a caster and is ready to produce merchant pig iron for sale in the U.S. and Canada. They claim the reconditioned blast furnace can produce 1.0 million tons per year; however, all that ‘hot metal’ will not be used for merchant pig iron production as they are also producing steel. I think both USS and CLF will closely watch the developments at Stelco before diving into the pig iron distribution business.”
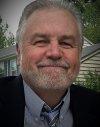
Tim Triplett
Read more from Tim TriplettLatest in Steel Products Prices North America
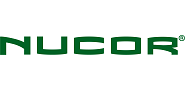
Nucor maintains plate prices, opens August order book
Nucor aims to keep plate prices flat again with the opening of its August order book.
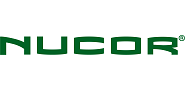
Nucor CSP remains level at $900/ton
Nucor maintained its weekly list price for hot-rolled (HR) coil this week, following two consecutive increases.
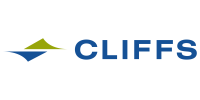
Cliffs raises prices, seeks $950/ton for July spot HR
Cleveland-Cliffs plans to increase prices for hot-rolled (HR) coil to $950 per short ton (st) with the opening of its July spot order book. The Cleveland-based steelmaker said the price hike was effective immediately in a letter to customers dated Monday.
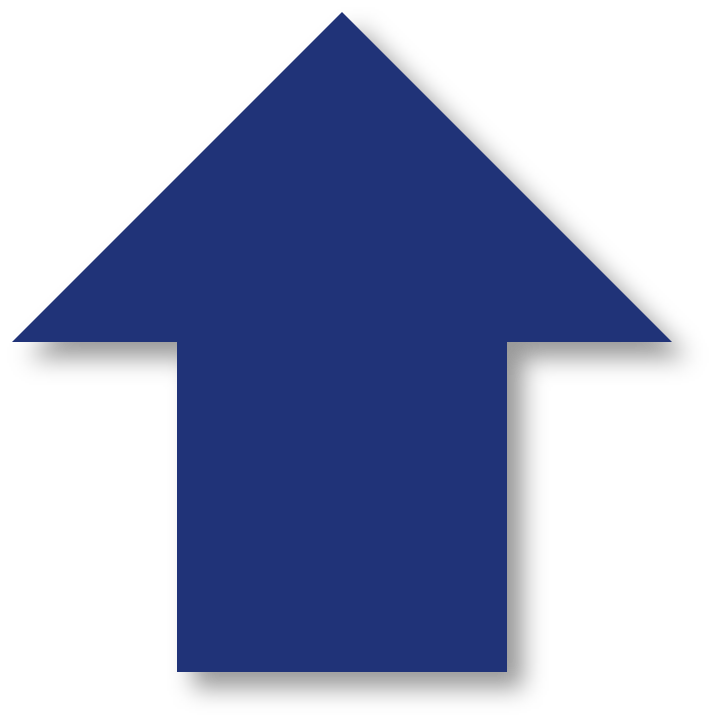
HRC vs. prime scrap spread widens in June
The price spread between HRC and prime scrap widened in June.
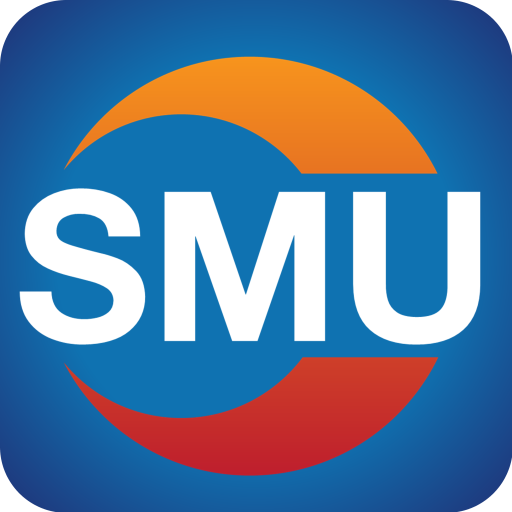
SMU price ranges: Steel prices rise in response to tariffs
Steel prices climbed for a second straight week across all five sheet and plate products tracked by SMU.