Environment and Energy
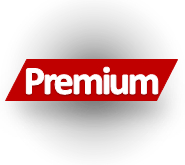
CRU: Challenges Ahead for the Steel Industry to Achieve Carbon Neutrality
Written by Tim Triplett
July 14, 2021
By CRU Research Analyst Yusu Mao
CRU hosted its inaugural Steel Decarbonization Strategies Virtual Conference from June 25-28. Policy makers, industry leaders and financial institutions from across the global steel value chain joined the event to discuss pathways to carbon neutrality, the financial tools to support necessary investment and the policy frameworks needed to make them viable. This Insight highlights some key takeaways from the three-day event.
Achieving Carbon Neutrality Posts Enormous Challenges for Steel Producers
The steel industry accounts for ~8% of the world’s carbon emissions and the challenge to achieve net zero is large and complex. At the same time, steel demand is forecast to increase over the next decade and beyond, therefore, the requirement to reduce emissions intensity of steelmaking is only growing greater. In this respect, it is recognized that simply improving process efficiency, while a valid shorter-term measure, is not a solution and that fundamental changes to plant technology will be required.
That is, to meet global emissions targets, a significant change to the way that steel is produced is needed, particularly for producers in countries that are already operating at, or close to, best practice. This will be achieved either by a reduction of the amount of carbon as an input into the iron and steelmaking process, such as by using natural gas or hydrogen to replace coal, or by capturing CO2 in combination with storage or recycling.
To realize commercially viable, widespread adoption, affordability remains a key difficulty to overcome. One of the key takeaways from the conference is that a broad shift to hydrogen-based steelmaking, which remains an emerging technology, involves huge capex and would entail high operating costs. Indeed, it is suggested that the wholesale adoption of renewables for base load power will lead to higher electricity prices, not lower, which would further undermine the cost structure of hydrogen steelmaking, which consumes large amounts of electricity. As such, one estimate suggests that CO2 prices would need to rise above $350 /tCO2 to lift traditional, integrated steelmaking costs sufficiently to incentivize investment in hydrogen steelmaking. With such high CO2 prices, steel prices would have to rise significantly, hence, strong policy support would be needed, particularly where a country or region applied such a high price unilaterally.
The conference highlighted that a key choice for the industry will be to either adopt a multi-phased approach that could achieve deeper decarbonization earlier or to wait and adopt a final solution in one step at a later stage. For example, retaining existing processes alongside carbon capture would reduce emissions in the shorter term, but not completely until hydrogen-based DRI technology is available. Further details on technological developments were elaborated in the conference. Additionally, it was clear that each region will need to follow its own path, depending on its stage of economic development, resource endowment and existing steelmaking technologies in use.
Cross-Value Chain Thinking Matters for a Powerful Shift
Beside the challenges posed for steel producers, how steel consuming companies understand the overall carbon footprint of their suppliers was another focus of the conference. For end-users, including the auto, renewables and construction sectors, the production and processing of steel contributes a high proportion of their Scope 3 emissions and this is an increasingly important focus area of their procurement strategies. As a result, increasingly, steel suppliers are having to measure and disclose their carbon footprint to their customers and, in some cases, meet certain thresholds to be eligible to sell. This also raised the issue of standardization and the need for common, agreed measures of carbon performance.
It was also clear from the conference that pressure for change will come from other stakeholders on the value chain, such as consumers and investors. It was suggested that the drive for sustainable production from these players will create a pool of demand for low-carbon steel that has the potential to incentivize the green transformation.
CRU: Where We Can Help
In the conference, CRU’s market experts provided perspectives and insights on global decarbonization efforts across the steel supply chain. Analysis based on CRU’s Steel Cost Model set out the level of CO2 prices required to drive the transition to low-carbon steelmaking, as well as the role of policy. This analysis also demonstrated that a wholesale shift to scrap-based EAF steelmaking was not the answer and that, while recycled steel scrap formed part of the solution to low-carbon, it is not the whole. Indeed, it was further demonstrated that the perception of scrap-based EAF steelmaking as “sustainable” and integrated steelmaking as not, is wholly false and, in fact, counterproductive to the achievement of emission targets at the global level.
CRU has recently launched CRU Sustainability, a new division that brings together all of CRU’s sustainability expertise to give clients the much-needed data and insights to accelerate the journey to net zero. CRU Sustainability will have four focus areas: climate policy and regulation, carbon emissions and markets, the clean energy transition and the circular economy.
To find out more, or to discuss any of these issues and better understand the implications for your business, please contact CRU.
Request more information about this topic.
Learn more about CRU’s services at www.crugroup.com
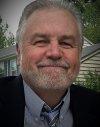
Tim Triplett
Read more from Tim TriplettLatest in Environment and Energy
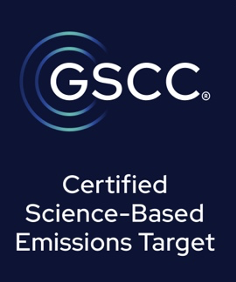
Global Steel Climate Council certifies eight SDI, ASA HR products
GSCC certifies eight products from Steel Dynamics and Arkansas Steel Associates.
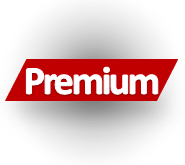
June energy market update
In this Premium analysis we examine North American oil and natural gas prices, drill rig activity, and crude oil stock levels. Trends in energy prices and rig counts serve as leading indicators for oil country tubular goods (OCTG) and line pipe demand.
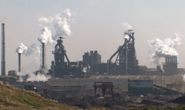
EPA deregulation proposals win praise from steel advocates
Two industry groups are applauding two EPA proposals that would support domestic steel production.
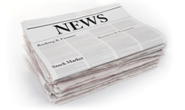
Met coal receives critical materials status
The US Department of Energy (DOE) adds metallurgical coal to the nation’s list of Critical Materials, following its designation by US Secretary of Energy, Chris Wright’s announcement on May 22.
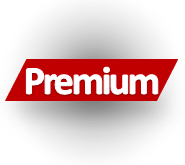
May energy market update
An analysis of the North American energy market in May.