International Steel Prices
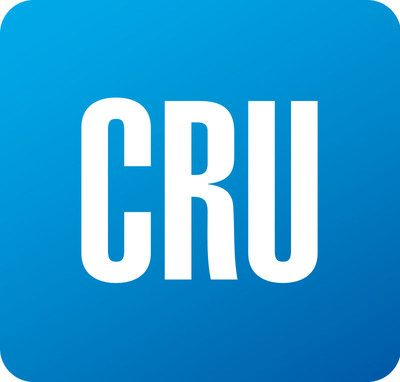
CRU: A Hydrogen Economy Would Create Huge Steel Demand
Written by Matthew Watkins
November 24, 2021
By CRU Principal Analyst Matthew Watkins and Analyst Iris Speelmanns, part of CRU’s steel and the energy transition series
When we think about hydrogen and steel, we generally focus on steel supply. Hydrogen is a possible alternate reductant, replacing coke and offering a pathway to low-CO2 steel production. But a hydrogen economy could also be a huge driver of steel demand. Here we set out some thinking on the enablers of, and barriers to, a hydrogen economy, some ideas on how it might be structured, and where and how much steel it could consume.
What is a Hydrogen Economy and How Do We Get to One?
Today we make and use hydrogen mainly as part of industrial processes, especially the manufacture of ammonia. Mostly this is what is called “grey” hydrogen, which uses fossil fuels (i.e., largely natural gas) as an input. In that sense, there is already a “hydrogen economy.” But when we use this phrase in connection with a sustainable future, we are really thinking about making hydrogen in new, more sustainable ways, and particularly we are thinking about using hydrogen for many more things. Hydrogen would remain a direct industrial input but much more widely so, for example, being used as the reductant in ironmaking where today this is mostly coke, or natural gas in some cases. Its uses would grow outside the industry to include areas such as transportation fuels, heating and energy storage and transport. In each of these cases, the driver is the desire to minimize CO2 emissions and combat global climate change by using less-polluting hydrogen to displace fossil fuels.
Is this a good idea? It is certainly an idea whose time appears to have come politically and societally. To have success, it must also work economically. Currently this is not the case. Hydrogen is expensive to make and inefficient or even unproven to use in many applications. But it can be made and consumed in ways that are low emitting. Consequently, to get to a hydrogen economy these processes need to become cheaper, relative to what we do today.
Higher Costs of Emitting CO2 Would Be One Way to Force It
One way to do that is to increase the cost of high-CO2 options. CRU Sustainability has constructed a carbon abatement curve that sets out the CO2 cost necessary to incentivize transitioning to low-carbon technologies across various areas of the economy. As the CO2 emissions element of continuing to operate with existing polluting processes becomes more expensive, progressively more lower-emission processes become attractive as a substitute. There are many lower-emission processes that can be incentivized, including relatively “easy” and well-advanced ones such as wind or solar replacing coal power.
CRU’s work shows that the various hydrogen-based processes cluster to the upper end of the abatement curve (i.e., they all require a high CO2 cost to make economic sense). Specifically, we are talking about CO2 costs of €200 /t ($225 U.S.) and above. This assumes no subsidy and that it is the market that provides the incentive.
Clearly that is far from current CO2 costs, which are close to €60 /t ($68 U.S.). So it may be that we cannot rely on market forces alone to develop a hydrogen economy any time soon.
Bringing Hydrogen Production Costs Down is Another
If we could make hydrogen more cheaply, that would be likely to make it more attractive. Development of the industry over time is likely to do this, but there is a chicken-and-egg situation whereby the industry needs scale to bring costs down, but it is too high cost to achieve scale to start with. This is a problem that faces all nascent industries. Generally, the solution is to subsidize and protect the infant industry in some way until it achieves sustainable scale. In principle, subsidization can stop at that point.
Hydrogen has Attractive Security of Supply Considerations
Unlike fossil fuels, where the resources are distributed around the world depending on the gift, or otherwise, of geology, hydrogen is a manufactured product and, in principle, can be made by any country. For green hydrogen, which is made by using renewable electricity to split hydrogen from water molecules, “all” you need is somewhere with access to wind, sun, waves, tides or geothermal energy, coupled with access to water. Lots of places in the world have that and so there is an immediate attraction in principle towards hydrogen from a security of supply standpoint. It is no longer about whether you were lucky enough for geology to gift you with natural reserves.
Renewable energy potential is more equitably distributed than fossil fuel resources, but it is still not even. Some places are sunnier, some are windier, or have bigger tidal ranges for example. A lot of attention on hydrogen focuses on plans for very large-scale production hubs in places such as Western Australia, North Africa or Chile. These are predicated on a local potential for lots of low-cost renewable energy. In places where the cost of renewables is higher, it makes less sense to go large on hydrogen production. But the security of supply imperative may support a second production model in these places that is small scale for local consumption.
Large Scale = Large Challenges
For the large hubs, the model is likely to be one of many exports. Hydrogen could be made, perhaps converted, into a more transportable form such as ammonia, shipped around the world and then consumed somewhere else. This consumption might be as ammonia or it might need some re-processing, perhaps even back into electricity.
This sounds insane. Why would you take a lot of electricity, use it to separate hydrogen from water – which might even necessitate a prior electricity-intensive step of desalination if seawater is the hydrogen source – convert that to ammonia, ship it somewhere else, ideally in a low polluting way, and then use it to generate a much smaller amount of electricity at the destination? The electricity cost at source would have to be orders of magnitude less than the cost at destination, and there would have to be no alternative solution for either transport, storage, local generation or energy/ fuel source.
Maybe less seemingly insane is a model whereby hydrogen is transported as hydrogen through pipelines. In this model, it would be very difficult to get hydrogen from Australia to Japan, for example, but it could work to cross landmasses as we already do with natural gas. Again, there are problems. Hydrogen has a lower density than natural gas and you need to put much more of it into a pipe to transport an equivalent amount of energy. It can also cause problems relating to the steel of the pipe if you are not careful. A further problem with long distance transportation is that hydrogen is very explosive, raising lots of safety issues.
Where you have lots of production in one place and lots of consumption in another then you are going to need storage solutions. This could be geological storage – again, like natural gas – or it could be tanked.
Is Smaller More Beautiful?
These large challenges might suggest that local hydrogen networks are more attractive. A few hundred years ago, it was entirely normal for factories and mills making wool or cotton goods, or grinding flour, to have their own local power supply. Build the mill next to a flowing river, ideally create a reservoir upstream to preserve and control the water flow, install a waterwheel and you have lots of clean local power for your industrial operation. There may be nothing wrong with that as a concept. A local network minimizes the need for transport or storage. But it may be questionable whether any individual site is large enough to support the power generation infrastructure. This might also imply that hydrogen industries should move to where hydrogen is the cheapest.
A Hydrogen Economy Would Generate Steel Demand in Three Main Areas
Assuming that all these challenges can be overcome, we see three core areas where a hydrogen economy would demand steel:
- Production: renewable energy infrastructure
- Transport: pipelines
- Storage: tanks
Below we explore these areas in more detail and introduce some ideas on the scale of steel demand that might result.
Hydrogen Production: Renewable Energy Needs Steel
Making hydrogen without emissions is a clear long-term goal. If this happens by electrolyzing water, the electrolysis process needs to run off low-CO2 electricity. This could be nuclear, which would be a less steel-intensive solution. Nuclear does come with its own unique problems that may prevent widespread adoption in some regions, but the industry is not stagnant and there may be possibilities for hydrogen that arise from current proposals for mini reactors, for example.
If the electricity is supplied by solar or wind it will be steel intensive. Our prior work on steel in renewables shows steel intensities of 35–45 t/MW in solar, 84 t/MW in onshore wind and 212 t/MW in offshore wind, which perhaps could double for floating offshore.
How much hydrogen do we need to make? This is a big question and of course the answer depends on how many things we convert to running off hydrogen. In Europe, one detailed answer has been provided by the European Hydrogen Backbone. This gives forecast numbers for TWh of hydrogen demand in Europe across future industrial, transport and power uses. This gives a good basis to illustrate the order of magnitude of possible associated steel demand, combining with our intensity of use numbers above, including system losses and typical renewable load factors, and assuming that all demand is met by local production:
The result suggests that potentially very large amounts of steel will be needed to support making the hydrogen needed. If all the electricity needed was generated by fixed bottom offshore wind, the associated European steel demand could be 197 Mt by 2030, for example.
For context, in 2021 total EU+UK carbon steel demand from all sectors is expected to be 153 Mt. So, these are incredibly large numbers.
A key reason the numbers are so large is that the load factor (i.e., utilization) is low for renewables. And this is only for Europe – as other regions develop hydrogen economies, this adds to these numbers.
It is worth noting that if blue hydrogen gains significant ground as a solution, it is possible that there could be additional steel demand if the CCUS component of the system needs steel pipeline capacity. Here we have assumed that the economics of blue hydrogen only work with local CCUS sites, which minimize pipe needs. In any case, blue hydrogen may be a temporary, or bridge, solution.
Further, the electrolyzers themselves may be a source of steel demand. We have assumed in this modelling work that their steel need is small relative to the renewable energy, but this is a further area of upside.
Hydrogen Transport: Steel Pipes and Ships
As discussed above, bulk hydrogen is likely to be transported by pipeline where geography allows, or by ship where it does not, in which case it may be in the form of ammonia. Local hydrogen networks may utilize smaller-scale road tankers, but these are likely to be small scale and relatively minor in terms of steel demand.
Possible sources of steel demand are, therefore, in the pipes and ships, along with any necessary changes to port infrastructure (e.g., re-purposing LNG terminals). This, in turn, implies much of the demand from transport will be for steel plate.
Hydrogen and steel are not best friends and steel pipes carrying hydrogen risk embrittlement unless additionally protected. Coatings and linings of pipes are possible to avoid this risk. Some steel companies are developing steel grades designed to be suitable for hydrogen transport. For example, in June 2021, it was announced that Corinth Pipeworks started delivery on an order by Snam for 440 km of large-diameter steel pipe suitable for up to 100% H2. The steel is grade L415ME, supplied by ArcelorMittal from Fos-sur-Mer and Bremen. AM said this is a new steel (n.b. maybe new to AM) created for the project and it is carrying out further research into suitable steel grades.
We assume that steel will be the material of choice for pipes. Plastic is assumed not to be a viable alternative for several reasons including that it can experience a loss in ductility or reduction in other mechanical properties because of the needed operating temperature and pressure conditions. Additionally, plastic is made out of oil, which will need to be avoided in a sustainable economy.
Several studies suggest that most of the existing natural gas transportation infrastructure could be re-used for hydrogen. If this is true – maybe a big “if” – this will limit upside for steel demand, but there are some additional elements. According to a whitepaper from Siemens, to maintain equivalent energy flow, hydrogen should be transported at 3x the volume of natural gas, meaning 3x as many turbines and compressors are needed on the network. More substantially, less than 100% of existing pipes may be suitable for hydrogen, meaning some replacement will be needed. Snam has been trialling pipeline shipment in Italy of natural gas with a low but increasing H2 content. It estimates that 70% of its existing natural gas pipelines are compatible with hydrogen (n.b. it’s not clear if that means 30% are not compatible or have just not been tested).
Data in CRU’s Steel Plate Market Outlook indicates that large-diameter pipes are set to consume 4.0–4.5 Mt/y of steel in Europe in the next five years. As an order of magnitude estimate, we might assume that an additional 25% of this volume is needed for hydrogen-related upgrades to the existing and planned pipe network. This implies extra steel demand of 1.0–1.2 Mt/y. If the same assumption holds at the global level, the extra steel demand could be 7.0–7.4 Mt/y. These numbers have upside if hydrogen means more pipes are built than would be the case for gas.
Hydrogen Storage: Going Underground
As with natural gas, storage options for hydrogen comprise tanked storage and geological storage. More work may be necessary to fully understand suitability of geological storage but, in principle, salt caverns or porous rock storage may be suitable. Limitations will be most obviously the existence of suitable geology but also how easily and cheaply hydrogen can be input and output.
In the case of natural gas, most large-scale storage is geological rather than tanked. Tanks are more widespread for oil storage.
Storage may be for commercial or strategic reasons. Strategic storage is usually done at the country level to help manage variability in supply, and commercial at the company level to help manage variability in demand. Would there be a case for strategic storage of hydrogen as there is for natural gas? As it is a manufactured product, the strategic nature may be more around strategic production rather than strategic storage as such. Countries do not have to be “blessed” with hydrogen deposits; they can simply choose to make them. Probably many will choose to do so.
For large scale manufacturing, what are the critical drivers of location? How high does availability of suitable geological storage rank? The number one criterion is likely to be local availability of cheap renewable power. If that is the case, maybe geological storage is a “nice-to-have” but not critical at the supply site. If there is no direct shipping link set up to a remote storage location, could tanks be needed?
The space needs of hydrogen suggest that tanks are unlikely to be a large-scale solution. Ultimately, therefore, we do not think that storage will be the major driver of steel demand in a hydrogen economy. But it can add something. From our earlier work on steel used in oil and gas, we concluded that oil storage tanks consumed globally ~5 Mt/y of steel. Tanked storage is much more prevalent in oil than in gas and hydrogen is likely to be more like gas, therefore, this 5 Mt may be considered an upper limit.
Request more information about this topic.
Learn more about CRU’s services at www.crugroup.com
Matthew Watkins
Read more from Matthew WatkinsLatest in International Steel Prices
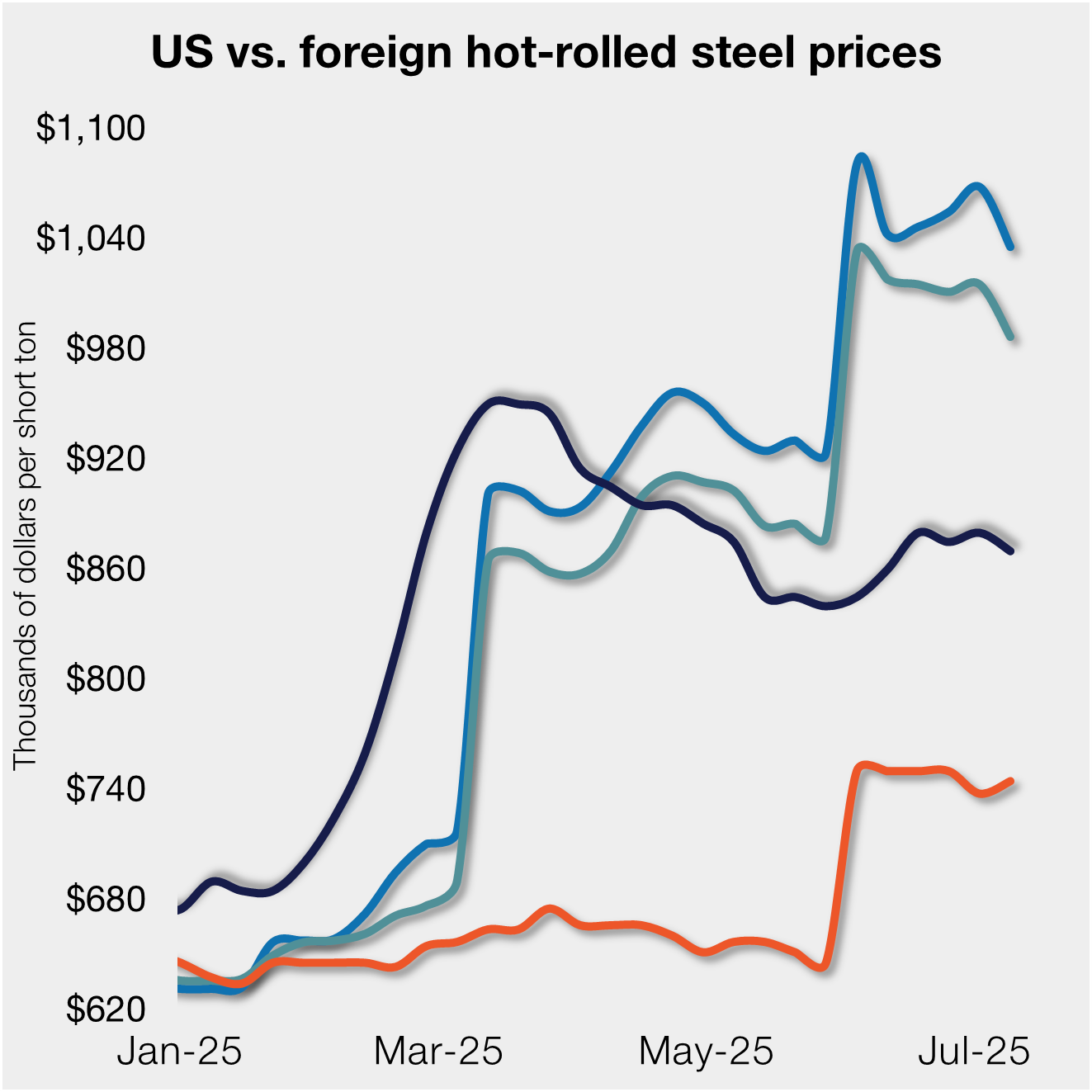
S232 tariffs keep US HR prices below imports from EU
Hot-rolled (HR) coil prices in the US ticked down this week but have fluctuated little over the past month. Stateside tags continue to trail imports from Europe, supported by Section 232 steel tariffs that were doubled in early June.
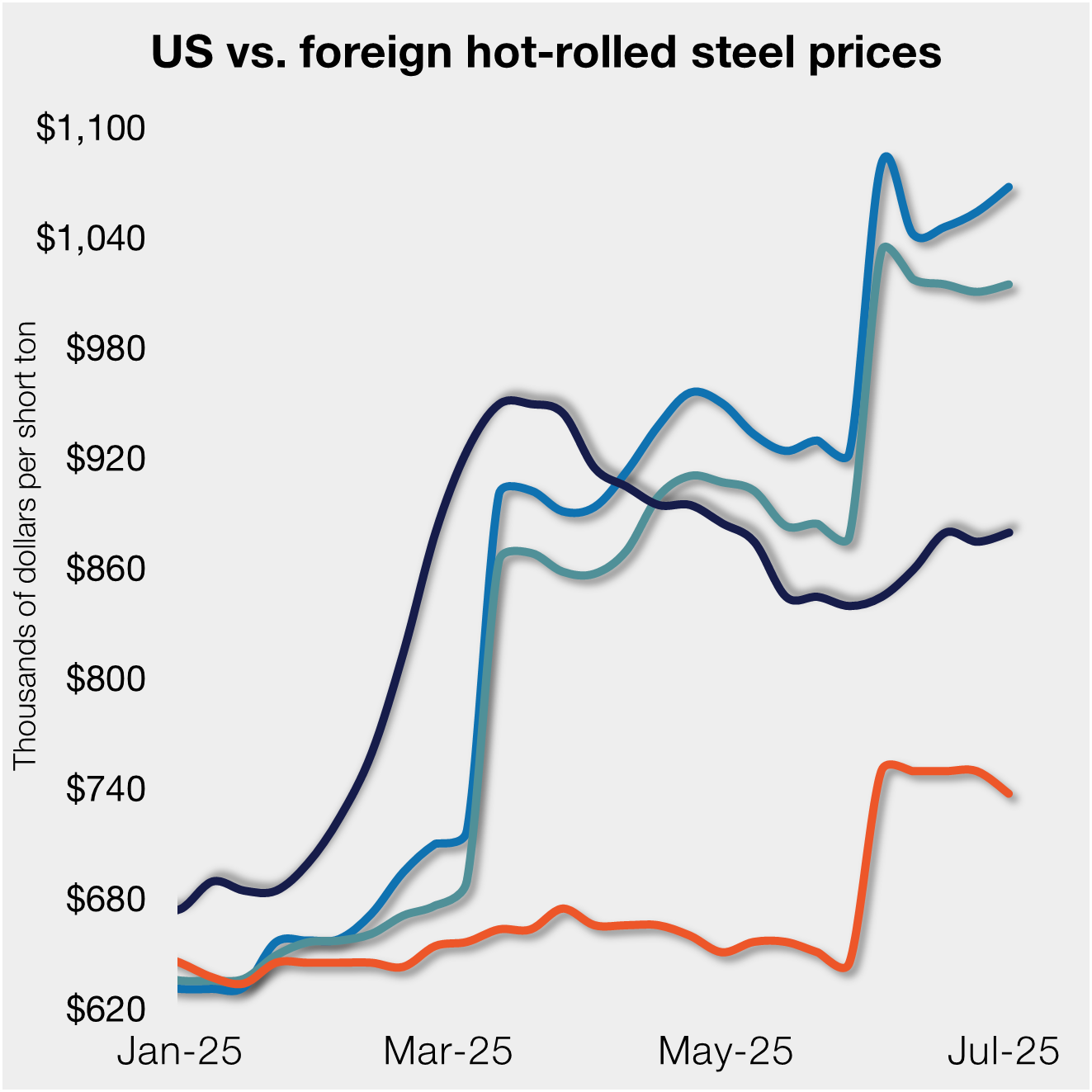
Doubled S232 tariff holds US HR prices below EU
David Schollaert presents this week's analysis of hot-rolled coil prices, foreign vs. domestic.
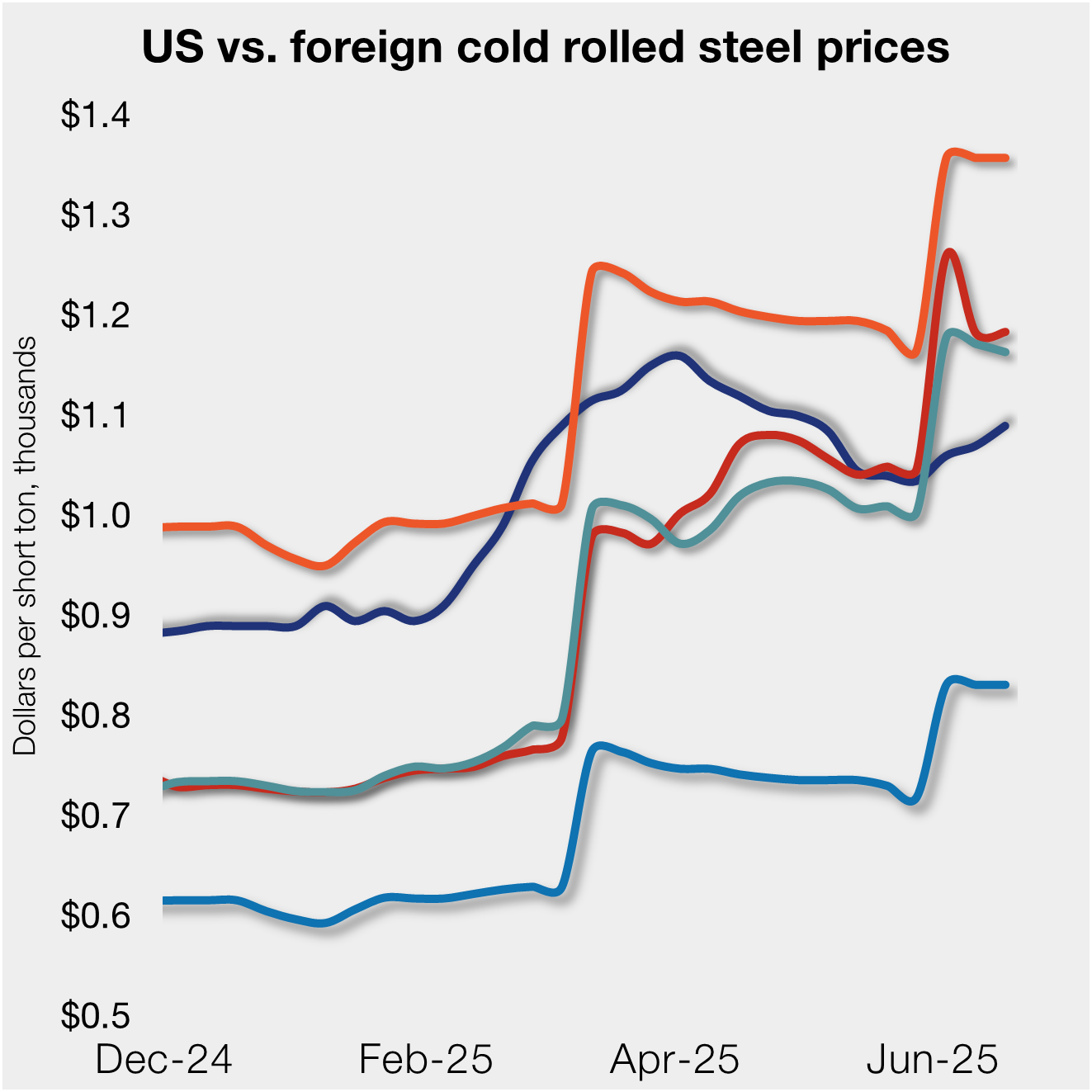
Higher US CR prices inch closer to EU, Japanese tags
US cold-rolled (CR) coil prices continued to tick higher this week, while offshore markets were mixed.
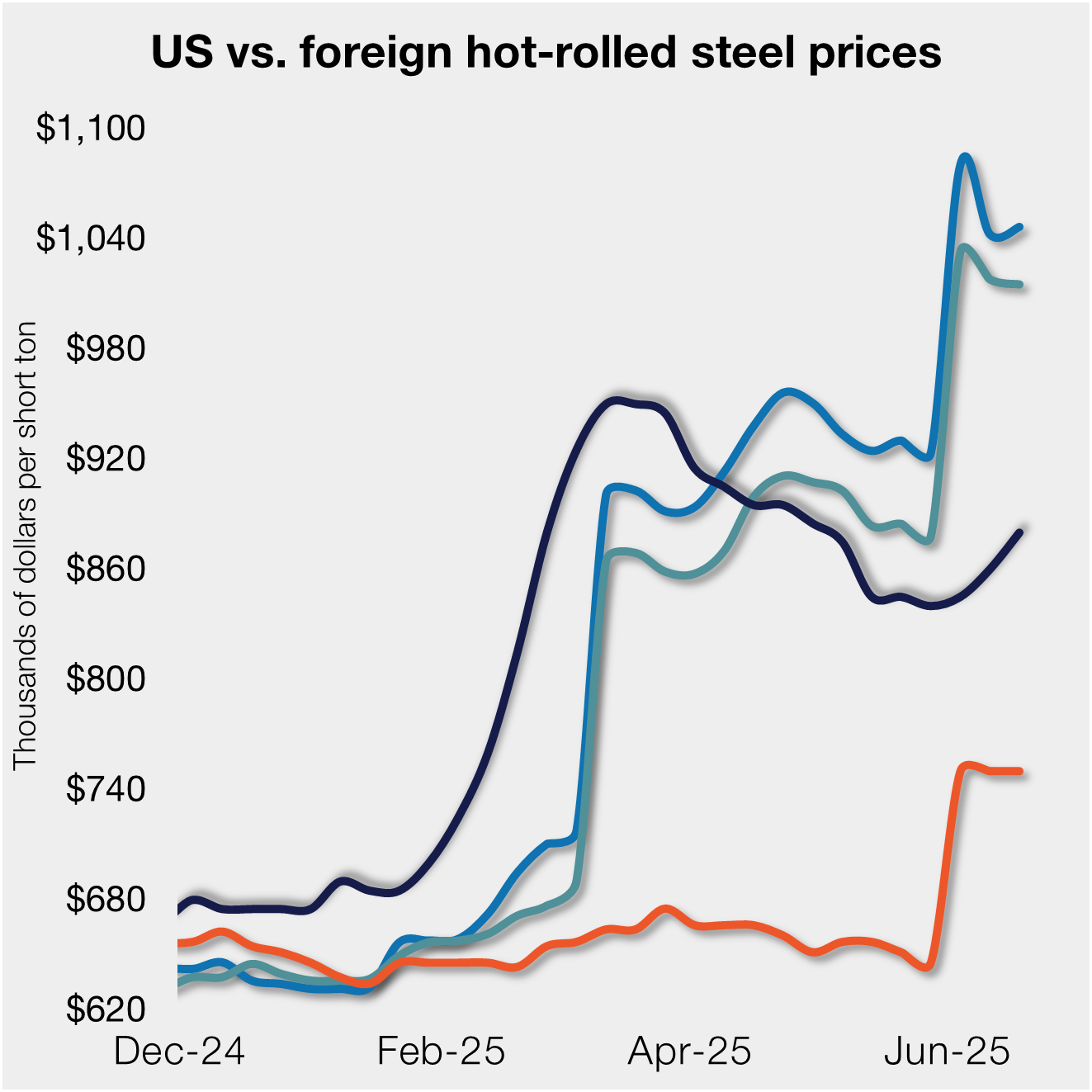
Stacked S232 keeps US HR prices below EU
US hot-rolled coil prices crept up again this week but still trail imports from Europe.
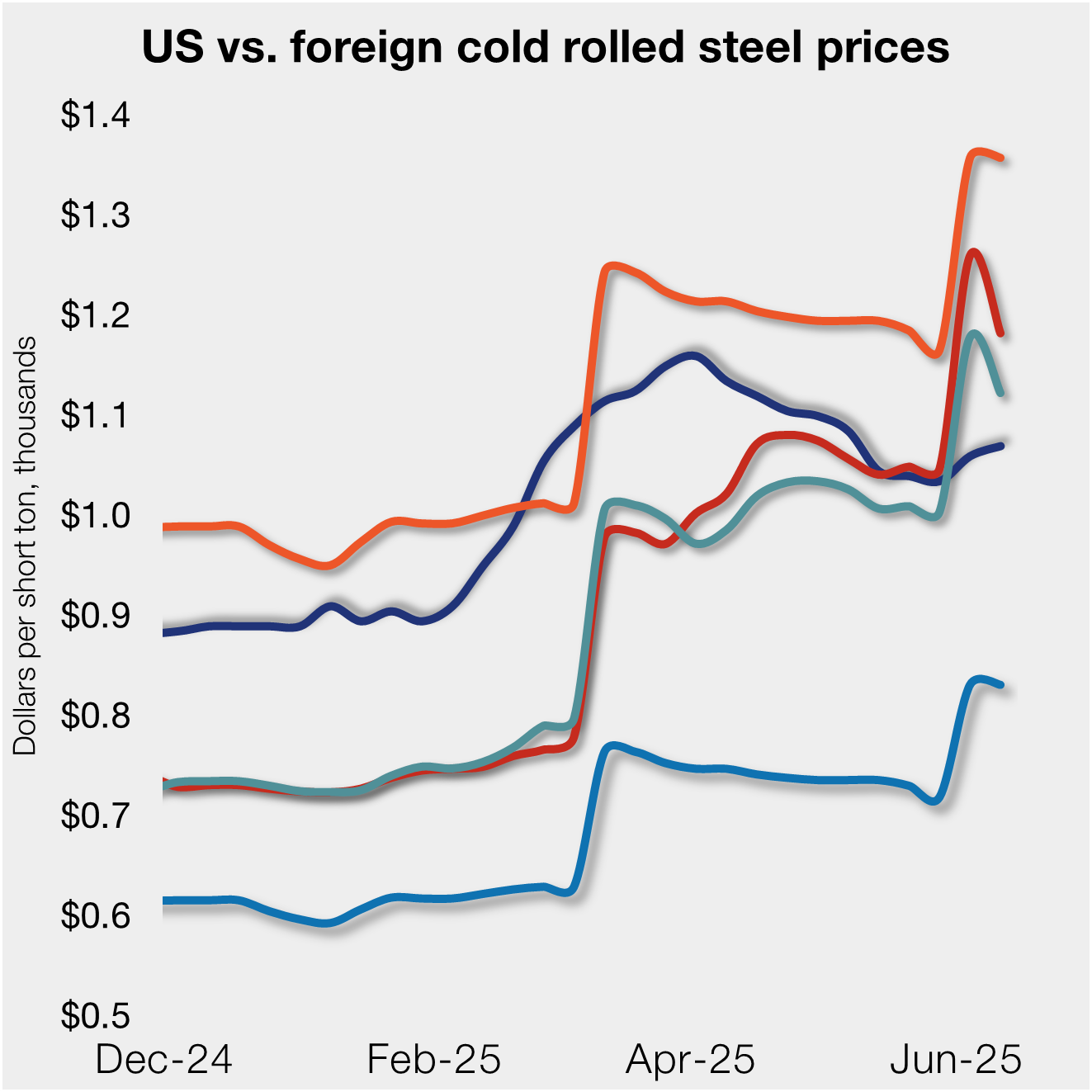
Doubled S232 lifts EU, Japanese CR prices over US tags
US cold-rolled (CR) coil prices edged up again this week, and most offshore markets moved in the opposite direction. But the diverging price moves stateside vs. abroad did little to impact pricing trends. The bigger impact was from Section 232, which were doubled to 50% as of June 3. The higher tariffs have resulted in […]