Steel Products Prices North America
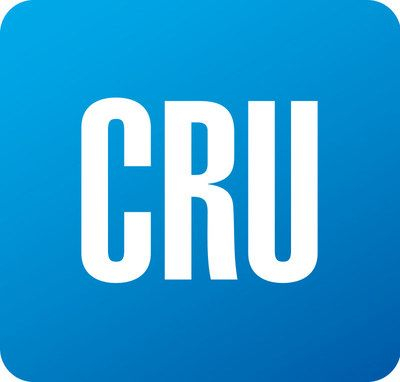
CRU: Aluminum’s Disruptive Technology Landscape
Written by Greg Wittbecker
December 5, 2021
By Greg Wittbecker, Advisor, CRU Group
Andy Grove, the former CEO of Intel, wrote a classic business book, “Only the Paranoid Survive.” One of the simple messages of that great read was to always pay attention to your competition. It’s for that reason, we thought it useful to update you on some of Alcoa’s recent statements from their 2021 Investor Day Event.
Alcoa presented their new technology roadmap on Nov. 9, highlighting two key projects:
• Their inert anode technology being developed with the Elysis partnership with Rio Tinto, Apple, and the Canadian government.
• Their recently patented Astraea technology for taking scrap aluminum and refining it to ultra-high purity primary-like aluminum.
Elysis Inert Anode
We have discussed inert anode in prior columns, but here’s a refresher. The aluminum industry has been producing primary aluminum with the same basic process since the industrial scale method was discovered in 1886. It uses an electrolysis process with a cathode and anode in a cell to extract the aluminum from aluminum oxide (alumina). The process has undergone enhancements over the years in terms of cell design and higher amperage applied to the process. Industrial cells ran at 50,000 amperages during the World War II era; the Chinese and Rio Tinto have developed cells now running at 600,000-660,000 amperages as “pre-bake anode technology.” However, the process still employs a carbon anode that degrades over time and generates CO2. Best-in-class primary smelters generate about 2 tons of CO2/ton of metal (using hydro power). Worst-in-class smelters generate about 15-17 tons of CO2/ton.
Alcoa has been working on the inert anode for decades. The concept replaces the destructible carbon anode with an inert anode made of a proprietary material that lasts a very long time and eliminates the carbon emissions. Elysis was formed to join forces with partner capital and unique technical contributions to get this concept into commercial production.
Elysis came into being in 2018 and has been making steady progress. The joint venture has:
• Demonstrated it can make commercial grade 99% aluminum in lab conditions.
• The process eliminates CO2 and generates oxygen, thus they can advertise the metal as having zero direct carbon emissions.
• They have perfected how to produce the inert anode using standard, commercially available materials.
So, What’s New?
The Elysis partners are now constructing an undisclosed number of industrial-scale cells in Rio Tinto’s Alma, Quebec, smelter. These will run at 450,000 amps and will provide the first commercial demonstration of the technology. Many key questions await answers from this stage of development:
• How durable is the inert anode? Elysis says it could last over two years compared to existing technology, which requires replacement every 20-30 days.
• Will the cell produce 99.7% purity? This is the commercial standard today.
• What will be the energy efficiency of the cell? Best-in-class pre-bake smelters are aiming for energy consumption below 12,000 kWh/ton of aluminum.
• What will be the cost of production? The average cost of producing aluminum today is about $1,575/ton with best-in-class under $1,000/ton and the worst above $2,600/ton.
Elysis is concurrently building the supply chain to produce the inert anodes. They aim to commercialize the technology in 2024 with major deployment aiming for 2026.
The Russians are also working on their version of inert anode and have successfully produced 99% purity in Siberia. They have advertised their technology being ready in 2023, however have “hedged their bets” by concurrently announcing major capex programs in Siberia using existing technology. The Chinese have been remarkably quiet, considering they have led the world’s advancement in pre-bake technology. We suspect the Chinese have their own version of inert anode and are waiting to announce it once they have run it at industrial scale.
The promise of producing a carbon-free primary smelter is exciting, as the global economy aims for decarbonization. However, until we see tangible proof the process’s durability – and more importantly its cost structure – it is hard to predict when the technology becomes broadly adopted.
Alcoa’s Astraea Metal Purification Process
Alcoa’s other announcement at Investor Day seems to have caused an even higher stir than Elysis. They have patented a scrap purity process trademarked as Astraea. It appears to be a discovery found during the work on the inert anode and uses an electrolytic process to purify metal.
Alcoa aims to take shredded aluminum (ISRI specification “Zorba”) and refine to P0101 purity or 99.99%.
The promise of the technology is two-fold:
• It creates an entirely new market for Zorba, which today relies on secondary diecasting market demand in the U.S. and abroad. This is especially intriguing when one considers that as the auto industry migrates towards electric vehicles and away from internal combustion engines (ICE), the demand for diecasting is expected to decline sharply approaching 2035 when some automakers say they will be out of the ICE business.
• The process provides a low carbon supply of very high purity aluminum to supplement existing primary pre-bake technology and/or the Elysis process. Does the market need 99.99% aluminum? Absolutely NOT. The market for this grade is relatively tiny and the resultant Astraea product would likely be blended down for alloying.
Will it work, what will it cost and why does this matter to steel?
Alcoa is now constructing a pilot plant and aims to be commercial scale in the next 1-2 years.
There is a risk of comparing this process to that of existing scrap recycling processes. That would NOT be the best way to think about this. Astraea really is the ultimate example of a “hybrid smelter,” blurring the distinction between a primary aluminum smelter and a classic secondary smelter. The metal it will produce won’t compete for secondary metal demand…it will compete for PRIMARY metal demand. As such, its cost structure will need to be competitive with the best of the best of the primary smelters.
Why should steel care about any of this, you ask? You should if you buy steel scrap. Zorba is a co-product of steel shredding. The demand for steel scrap is what drives the run rates of shredders. Zorba “comes along for the ride.” No one pretends that the demand for Zorba inspires shredders to process more/fewer auto bodies. Zorba and the other nonferrous revenue streams are good for the shredders now. They could get even better if Astraea works, and this “might” drive different production decisions for shredders.
Today, Zorba is priced to sell against diecast alloy A380, DIN226 (EU) and ADC12 (Asia) and trades at a substantial discount to primary aluminum. A380 is worth about $1.14 per pound compared to primary 99.7% ingot at $1.45 per pound.
In an Astraea inspired price environment, Zorba could become a key feedstock to producing primary-like metal, trading at that $1.45 price. That $.31 per pound price differential will be reflected in Zorba’ s value, and an increase in Zorba’ s value of that magnitude would change the revenue stream for a shredder dramatically. Zorba sales could become much more interesting and “might” inspire higher shredding run rates = more steel scrap.
There are a lot of gaps in this theory today, notably can Astraea work and at what cost? However, if it can be a durable process AND competitive with PRIMARY smelting costs….it could be a game-changer for the Zorba market and indirectly the steel scrap market.
Greg Wittbecker joined CRU in January 2018 after retiring from Alcoa, where he was Vice President of Industry Analysis and Managing Director of Alcoa Beijing Trading, based in Shanghai, China. His career spans 35 years in the aluminum industry, having also held senior commercial and management roles at Cargill, Wise Metals and Koch Supply and Trading. Greg brings perspective on the entire aluminum supply chain from bauxite to aluminum finished products and will be a regular contributor to SMU going forward. He can be reached at gregory.wittbecker@crugroup.com
Request more information about this topic.
Learn more about CRU’s services at www.crugroup.com
Greg Wittbecker
Read more from Greg WittbeckerLatest in Steel Products Prices North America
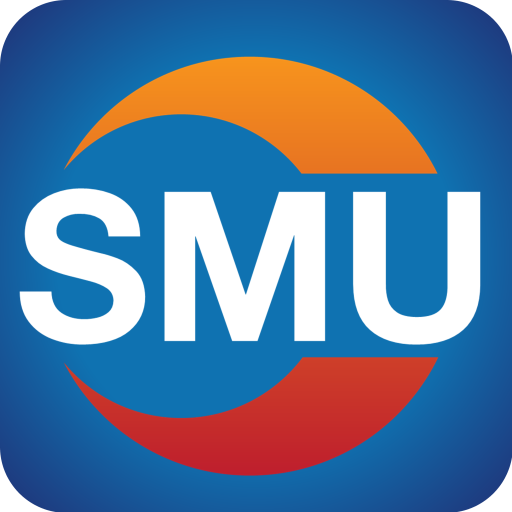
SMU Price Ranges: Sheet and plate steady ahead of Independence Day
Sheet and plate prices were little changed in the shortened week ahead of Independence Day, according to SMU’s latest check of the market.
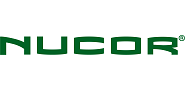
Nucor maintains plate prices, opens August order book
Nucor aims to keep plate prices flat again with the opening of its August order book.
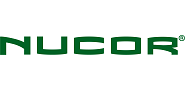
Nucor CSP remains level at $900/ton
Nucor maintained its weekly list price for hot-rolled (HR) coil this week, following two consecutive increases.
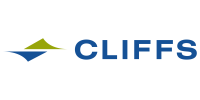
Cliffs raises prices, seeks $950/ton for July spot HR
Cleveland-Cliffs plans to increase prices for hot-rolled (HR) coil to $950 per short ton (st) with the opening of its July spot order book. The Cleveland-based steelmaker said the price hike was effective immediately in a letter to customers dated Monday.
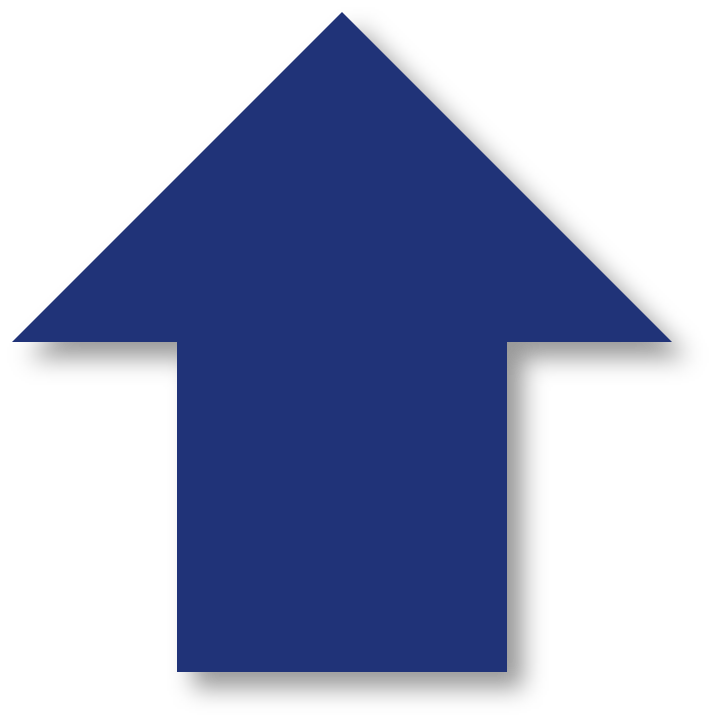
HRC vs. prime scrap spread widens in June
The price spread between HRC and prime scrap widened in June.