Steel Products Prices North America
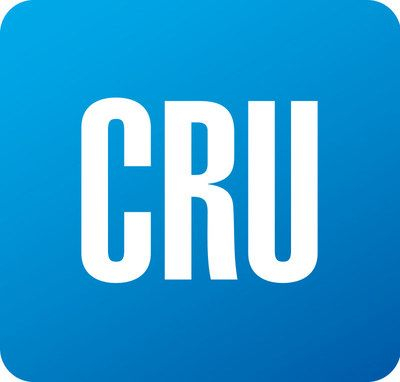
CRU Aluminum: Update on Decarbonizing Primary Aluminum
Written by Greg Wittbecker
November 18, 2022
New Commitments in Middle East Around Carbon Capture and Alcoa Gives Updates on Elysis Technology
We were struck this week by reports from Saudi Arabia that the Ma’aden smelter intends to pursue a carbon capture, utilization, and storage (CCUS) approach to reducing its carbon footprint.
During the current COP27 event in Egypt, Ma’aden’ Senior Vice President Hammad Al-Rashid made the statement that “carbon capture, utilization and storage represents a significant opportunity for the mining industry. At Ma’aden, we are committed to providing CO2 for the national grid. We have also started a project to capture CO2 to be used in the food and beverage industry”.
Most carbon capture technologies that have been studied for the aluminum sector have been found wanting because they were designed for capturing off gas from industries with much higher concentrations of CO2 than aluminum. Typically, these technologies were geared toward sectors with concentrations above 4%, where off-gas CO2 emissions in aluminum average around 1%.
Recently, Hydro Aluminum invested $20 million into US-based Verdox, an M.I.T. spin-off that aims to target the unique challenges of aluminum smelter off-gas emissions. Hydro thinks they have cracked the code and can get there cost-effectively.
The challenge with CCUS has always been cost. According to a comprehensive study conducted by the Belfer Center for Science and International Affairs at Harvard’s Kennedy School, CCUS is still very expensive to execute:
- Ammonia production: $22–32 per ton
- Cement production: $19–205 per ton
- Coal-fired power plants: $20–132 per ton
- Ethanol production: $26–36 per ton
- Natural gas power plants: $49–150 per ton
- Hydrogen production: $65–136 per ton
- Steel mills: $8–133 per ton
While aluminum was not explicitly cited in the Belfer Center study, we must assume that it is going to be the same cost range as coal-fired power plants and steel mills. A study published by Accenture entitled “Decarbonizing Aluminium with Industrial Clusters” (Jan. 18, 2022) estimates the cost at around $100/ton.
The industrial cluster concept leverages the idea of concentrating industrial energy companies in proximity to each other to amortize the high costs of CCUS across a broader number of companies. It also seeks to capitalize on industrial demand for CO2, such as Ma’aden aims to do in its vision statement.
Until recently, $100–125/ton for CCUS was categorially ruled out by aluminum producers as a viable path to decarbonize.
This was pragmatically based. The EU Emissions Trading System (ETS) over the course of the trailing 10 years has only briefly flirted with prices approaching €100/ton. For much of the decade, prices were under €40/ton. The business case did not exist, nor were there any consequences for not investing the capex in CCUS.
Fast forward to 2022. While the EU has postponed the imposition of its carbon border adjustment mechanism (CBAM) until at least 2025, there is a sense of inevitability coming and non-EU producers must ready themselves for this.
In the case of Ma’aden, they have average CO2 emissions of 7.4 tons (2023 CRU estimate, Scope 1-2-3). The proposed CBAM threshold of 5 tons means that Ma’aden faces a carbon tax on 2.4 tons x whatever the market price will be come 2025. At today’s ETS market, that would be a penalty of about $178/ton of aluminum attempting to be imported into EU27.
Now the business case changes, and it is easy to understand why the priority to decarbonize has been elevated
Zero Carbon Smelting — The Elysis Project Lays Out More Discrete Financial Targets
Alcoa, Rio Tinto, Apple, and the Quebec Government have been painstakingly developing the Elysis inert anode technology since forming their joint venture in 2018. This technology aims to not only generate zero carbon emissions, but to produce oxygen in its process.
The joint venture is now testing pots at Rio’s Alma, Quebec, smelter, aiming to operate three x 450,000 amperage pots by the end of 2023.
In statements at the Goldman Sachs Metals & Mining Conference on Nov. 16, Alcoa’s CFO Bill Oplinger laid out some very specific goals:
- A capital cost or intensity 10% lower than existing Hall-Heroult prebake technology
- Operating costs 15% less than Hall-Heroult
- Increase through-put of 15% over Hall-Heroult
- The partners expect to have the commercial package ready by 2024 and first hot metal from a retrofit or brownfield expansion in 2026
What Do These Targets Translate Into Based Upon Current World ex-China Metrics?
Drawing upon CRU’s extensive analysis of long-term trends in capital efficiency and operating costs, we can lay out some of Alcoa’s goals:
Capital cost improvement — The current pipeline of brownfield and greenfield smelter projects in the World ex-China has a broad range of unit costs per ton of planned capacity. These range from $1,475 to as high of $6,850, with an average of $3,800. Alcoa’s target would imply coming in at about $380 per ton below the average. Since the inert anode technology eliminated the use of pre-baked carbon anode, that is very realistic. A typical carbon anode plant attached to a primary smelter can easily cost $350–400 per ton of installed capacity.
Operating costs — CRU’s estimate of average business costs for 2022 outside China is around $1,735 per ton. Again, carbon cost elimination is the key. Carbon runs about 17% of a smelter’s cost so the 15% reduction appears to make sense.
Increased output — The best way of measuring increased efficiency is energy consumption per ton produced. The International Aluminium Institute (IAI) reported global average energy consumption for 2021 was 14,114 kWh per ton, with a range of 13,089 (North America) to 16,513 (Australia). A 15% gain in the average efficiency would mean a reduction in energy consumption of 2,117 kWh per ton to about 12,000 kWh per ton. Is that achievable? If the Chinese are to be believed, absolutely. The Chinese are now operating 660,000 amperage potlines and they claim to be aiming to reducing average consumption to under 11,000 kWh/ton. Elysis is aiming towards best-in-class consumption.
What’s Next?
The actions by Ma’aden, Hydro, Alcoa and Rio demonstrate that the primary aluminum sector is tackling the challenge of decarbonization head-on. It’s clear that participants are not waiting for the promise of renewable energy to offer the final solution.
In the case of Ma’aden, the proxy for the other natural gas-based producers in the Middle East, CCUS is beginning to be a faster path to decarbonize. Eventually solar and wind will provide viable alternatives to gas, but until the storage issues are solved, CCUS may be the quicker “fix”. The experience in the Middle East ought to spread into India and the other coal-based producer regions. China is already pushing this very hard.
Hydro’s decision to invest in Verdox is an interesting statement on the multi-thronged approach. Hydro enjoys access to rich hydro-based energy and along with Alcoa, has pushed into wind energy in Norway. Yet, they are concurrently using CCUS to lower the bar faster.
Alcoa and Rio are “all-in” on the inert anode. Skeptics say this technology has a long way to go to make the business case. However, the arrival of CBAM in Europe and other tax regimes, where failure to decarbonize becomes more punitive, will accelerate the process.
By Greg Wittbecker, Advisor, CRU Group, Gregory.Wittbecker@crugroup.com
Greg Wittbecker
Read more from Greg WittbeckerLatest in Steel Products Prices North America
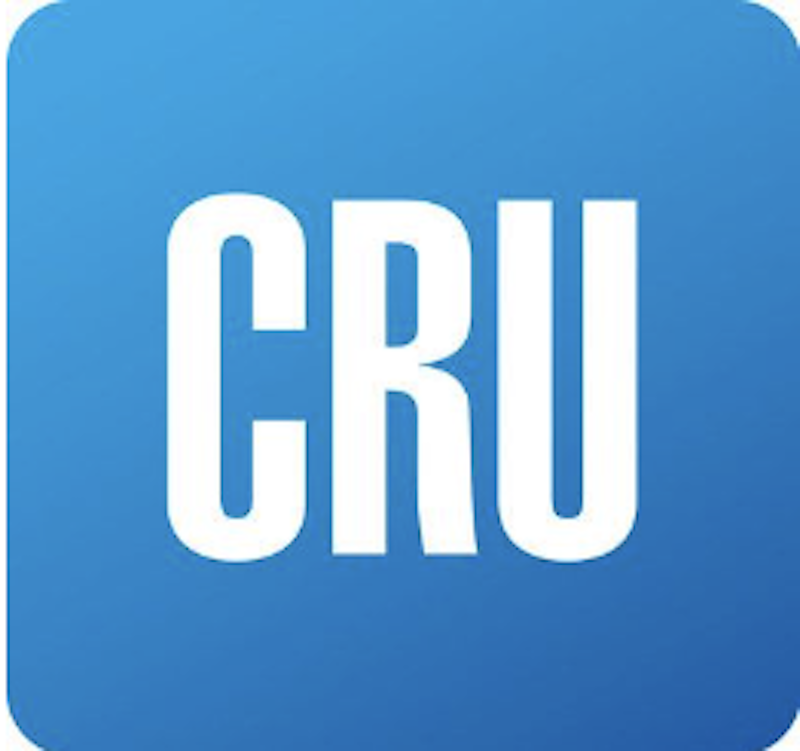
CRU: Q3 will be the lowest point in current sheet price cycle
CRU Principal Analyst Shankhadeep Mukherjee expects a restocking cycle for steel sheet products in most parts of the world due to either low inventories or seasonally stronger demand.
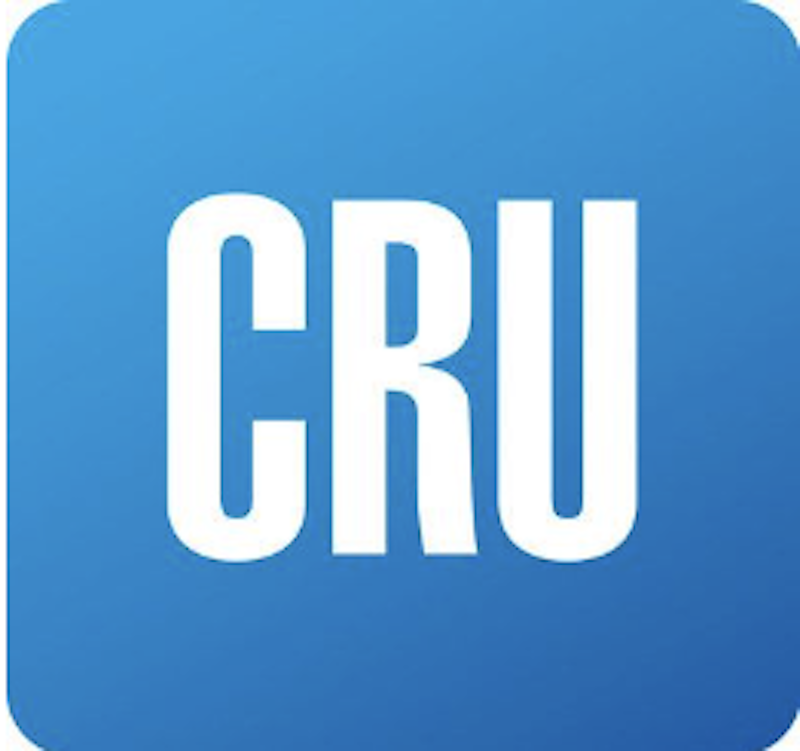
CRU: US rebar and wire rod prices rise alongside S232 increase
CRU Senior Steel Analyst Alexandra Anderson discusses current market and pricing dynamics for long steel products in the US.
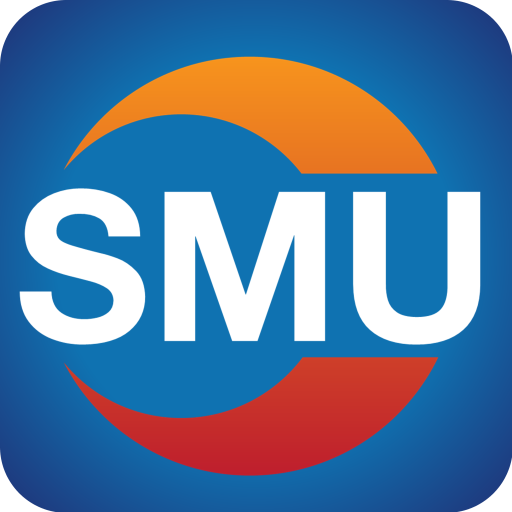
SMU Price Ranges: Sheet and plate steady ahead of Independence Day
Sheet and plate prices were little changed in the shortened week ahead of Independence Day, according to SMU’s latest check of the market.
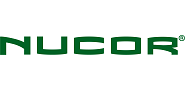
Nucor maintains plate prices, opens August order book
Nucor aims to keep plate prices flat again with the opening of its August order book.
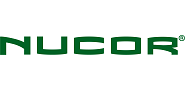
Nucor CSP remains level at $900/ton
Nucor maintained its weekly list price for hot-rolled (HR) coil this week, following two consecutive increases.