Steel Mills
Cliffs Rules Out New EAFs, Looks to Use More H2 in BFs
Written by Michael Cowden
February 16, 2023
Cleveland-Cliffs has ruled out spending money to build new electric-arc furnaces (EAFs), the company’s top executive said.
The Cleveland-based steelmaker will instead focus on decarbonizing its blast furnaces (BFs) and basic-oxygen furnaces (BOFs), which are better suited than EAFs to supply the automotive industry, company chairman, president, and CEO Lourenco Goncalves said.
“Cleveland-Cliffs does not need to and does not plan to invest in new EAFs beyond the five EAFs we already operate,” he said.
Goncalves made the comment during the company’s fourth-quarter earnings conference call earlier this week.
It was notable because Cliffs filed an air permit application to build an EAF at its Middletown Works in Ohio, although Goncalves has previously said the company wouldn’t further pursue an new EAF there.
Cliffs instead aims to use more hydrogen in its blast furnaces and in its direct-reduction plant in Toledo, Ohio.
Recall that Cliffs is already charging hot-briquetted iron (HBI) made in Toledo into its blast furnaces as part of its efforts to reduce carbon emissions.
“Now, we look forward to becoming the first steel company in the world to utilize hydrogen as a clean reductant to iron oxides on a full, industrial scale,” Goncalves said.
Such broader use of hydrogen hinges on the gas becoming more affordable and more widely available. To that end, Cliffs is working with the Great Lakes Clean Hydrogen Coalition in hopes of building a hydrogen hub in the Midwest, he said.
Cliffs, in the meantime, aims to decarbonize BF/BOF operations at its steel mill in Burns Harbor, Ind., via carbon capture and sequestration. Government incentives should help the project create “meaningful” return investments, Goncalves said.
Burns Harbor, with annual capacity of 5 million tons, is one of Cliff’s largest mills.
The emphasis on decarbonization comes as some EAF sheet mills say they are making inroads into automotive markets traditionally dominated by integrated steelmakers. Goncalves questioned their ability to make additional gains.
“Our significant presence as a supplier of highly specified automotive-grade materials, particularly exposed parts, dictates the use of blast furnaces and BOFs,” Goncalves said.
“We are not alone. Every country with a major presence in automotive manufacturing – Japan, South Korea, Germany, France, or even China… relies on blast furnaces and BOFs,” he added.
Automotive is important to Cliffs because it represents approximately 5 million tons of annual demand. Another 2 million tons per year feeds into automotive indirectly via service centers and processors, Goncalves said.
That means nearly 44% of the roughly 16 million tons Cliffs expects to ship in 2023 are linked to the automotive industry.
Goncalves also stressed on the call that coated products sold to the automotive industry – think galvanized, galvanneal, and electrogalvanized – are higher margin than commodity-grade hot-rolled and cold-rolled steel sheet.
By Michael Cowden, michael@steelmarketupdate.com

Michael Cowden
Read more from Michael CowdenLatest in Steel Mills
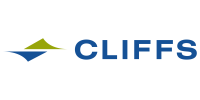
Cliffs idles Steelton, Riverdale, and Conshohocken operations
Cliffs has idled facilities in Riverdale, Ill., and Conshohocken and Steelton, Pa.
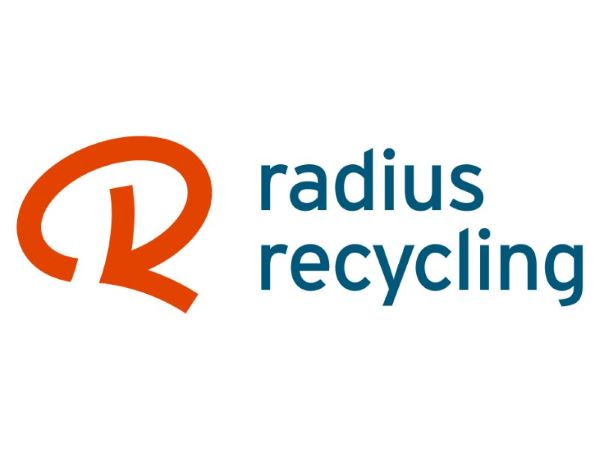
Radius loss narrows, volumes climb in ‘healthy’ West Coast market
Stronger steel demand in the Western US, rising scrap flows, and improved rolling mill utilization drove sequential gains for Portland, Ore.-based Radius Recycling.
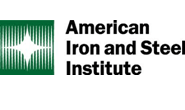
AISI: Raw steel production backs off multi-year high
US raw steel output edged lower last week after hitting a multi-year high in mid-June, according to the American Iron and Steel Institute (AISI).
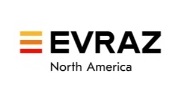
Private equity firm Atlas Holdings to acquire Evraz North America
Atlas Holdings said it has signed a definitive agreement to acquire Evraz North America (Evraz NA). The Greenwich, Conn.-based private equity firm said it expects the deal for the Chicago-based steelmaker to close in the second quarter of 2025 subject to various closing condition.
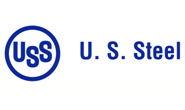
Granite City Works must remain open and other terms of the Nippon-USS deal
SEC documents also name Trump specifically as having veto power certain decisions are part of the “Golden Share” provision.