Economy
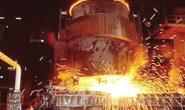
Residuals Eroding Minimills’ Cost Advantage
Written by Tim Triplett
October 12, 2017
What goes around comes around, as they say. In the case of the ferrous scrap market, what goes around and comes around again and again are residuals such as copper that complicate the steelmaking process and threaten to erode some of the competitive cost advantage now held by minimills.
Minimill steelmaking has transformed the steel industry in the past few decades and now accounts for nearly 70 percent of the steel made in the United States. Minimills use electric arc furnaces or EAFs to remelt ferrous scrap metal, including cars, trucks, appliances and other metal items recovered from the scrap stream. Integrated mills use basic oxygen furnaces or BOFs to make pure virgin steel from iron ore. The EAF steelmakers have a considerable cost advantage over the BOF mills, but the BOF process produces the highest quality steel. The minimills are continually working to improve the quality of their product with the goal of competing for high-end customers, notably the lucrative automotive industry. While the minimills have made significant inroads with makers of unexposed auto parts, the most demanding application requiring perfect surface quality—exposed auto body panels—remains elusive.
The minimills have a problem. Most of the impurities in melted scrap, including carbon, lead, zinc, silicon, manganese, phosphorous, sulphur, aluminum and vanadium, can be removed by pumping oxygen into the melted material. These elements either combine with the oxygen and dissipate as CO and CO2 or they oxidize and are removed with the slag.
Five elements commonly found in scrap cannot be removed from the metal: copper, nickel, chromium, molybdenum and tin. Each time steel is remelted, its dissolved content of these elements increases. These “residuals” affect the remelted steel’s hardness and formability, and can cause flaws in finished products, making them unsuitable for high-end applications where surface quality is critical. To work around the problem, steelmakers must add pure iron units, such as pig iron or DRI, to each melt to dilute the residual level to an acceptable, very small percentage.
“The EAFs enjoy a cost advantage today that could gradually whittle away,” explained steel industry veteran and consultant Steve Murphy. “The concern is that over time the scrap base will get higher and higher in residuals. If that does indeed happen, minimills will have to use increasing amounts of alternative iron units, which will increase their costs.”
To dilute the residuals, the minimills must purchase the highest quality scrap, alternative iron units such as direct-reduced iron (DRI) or hot-briquetted iron (HBI), or pig iron produced by integrated mills, which are their competitors in the U.S.
Murphy can foresee a time when U.S. minimills will purchase scrap exported from China. Almost all Chinese steel is produced using the BOF process, so Chinese scrap has much lower residual levels. China has reached a tipping point at which its economy and growing consumer base is now generating more scrap than the nation needs for its own recycling. The Chinese, who traditionally have been among the biggest importers of scrap from around the world, have recently begun exporting scrap—a trend likely to accelerate in the coming years, turning the global scrap market on its head.
Peter Wright, another steel mill veteran and consultant, expects scrap exports from China to explode, since little of it is consumed domestically by the nation’s BOF mills. This increase in supply stands to drive global scrap prices sharply downward. It would also be a big blow to integrated steel producers in the U.S., who would find themselves at an even greater cost disadvantage to their minimill rivals, he noted.
Copper is the most prevalent residual in scrap. If it is diluted to an acceptable level, the others (nickel, chromium, molybdenum and tin) should be sufficiently diluted, as well. For automotive steel, the copper content must be below 0.030 percent. A furnace full of obsolete scrap will typically have 10 times that amount. “If you have ‘thirty’ copper in your obsolete scrap, you have to do a huge dilution to get it down to the right level. It’s definitely a significant additional cost,” Wright said.
Material prices fluctuate over time, so it’s difficult to quantify the shifting costs of scrap vs. pig iron and other raw materials, Murphy noted. The cost of diluting the residuals may be offset by cheaper Chinese scrap at some point. “I’m optimistic solutions will be developed [to the residual problem]. It’s just a question of whether it will be cost effective.”
The automotive industry continues to experiment with new materials to take weight out of vehicles and improve their fuel efficiency. The proliferation of advanced high-strength steels containing such alloys as chromium and molybdenum will add to the residual problem in remelted steel. However, the added effect likely will be modest. It will be many years before the new generation of lightweight vehicles join the scrap heap. The substitution of steel by other materials such as aluminum, and the fact that high-strength steel parts are thinner and lighter, means steel will make up a lower percentage of automotive scrap in the future.
The challenge for minimills is not all about materials. To serve the market for exposed automotive body panels, minimills would also have to invest in high-quality galvanizing lines to ensure flawless surface integrity for painted cars and trucks.
Steel Market Update reached out to minimills for comment, but none responded as yet.
The phrase “what goes around comes around” basically means that the consequences of one’s actions must always be dealt with eventually. Minimill steel producers created a market for recyclable scrap metal. Over the next 5-10 years, they must face the consequences of dealing with growing impurities in their raw material.
Written by Tim Triplett, Tim@SteelMarketUpdate.com
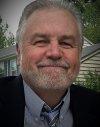
Tim Triplett
Read more from Tim TriplettLatest in Economy
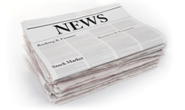
Steel groups welcome passage of budget bill
Steel trade groups praised the passage of the Big Beautiful Bill (BBB) in Congress on Thursday.
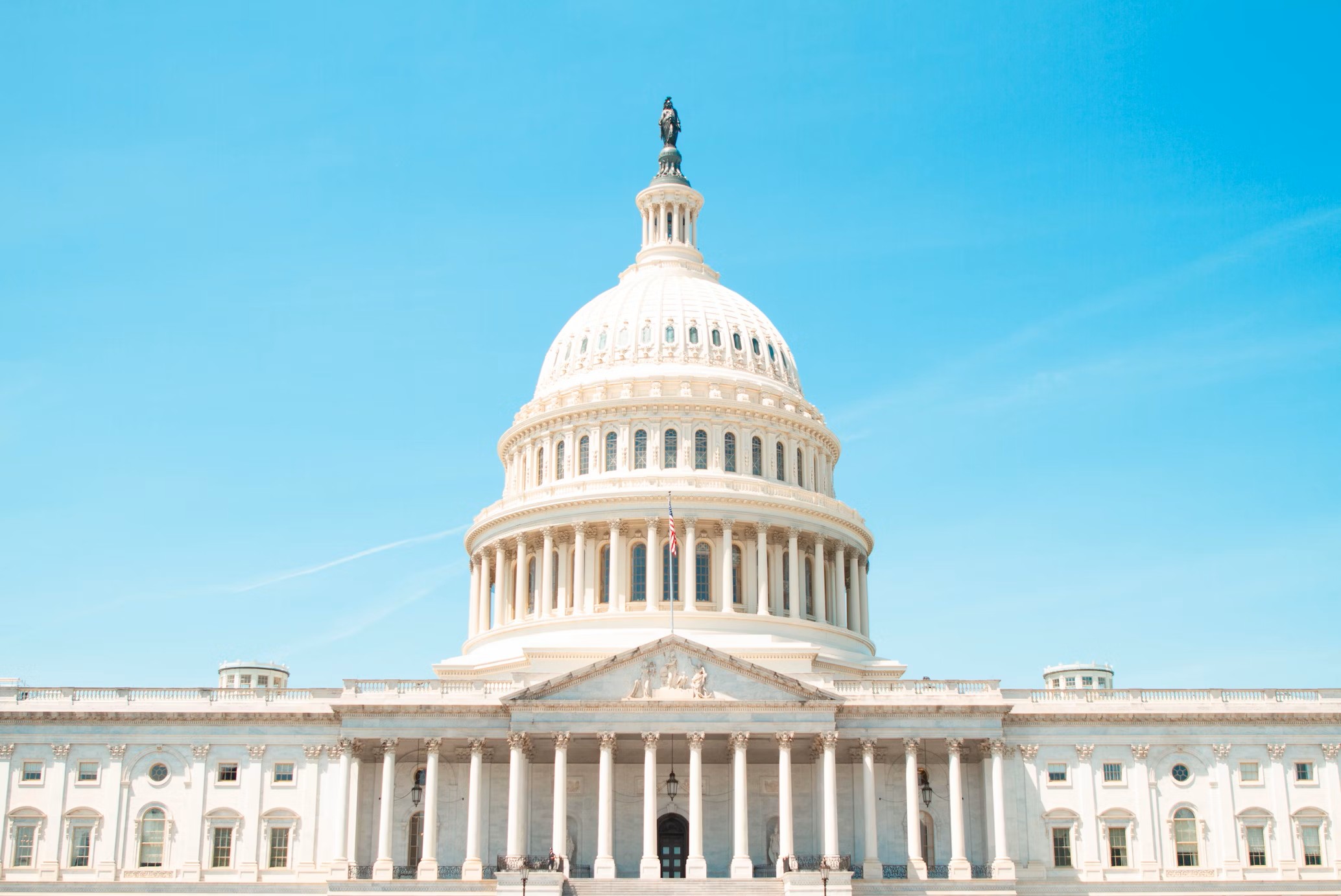
Industry groups praise Senate for passing tax and budget bill
The Steel Manufacturers Association and the American Iron and Steel Institute applauded the tax provisions included in the Senate's tax and budget reconciliation bill.
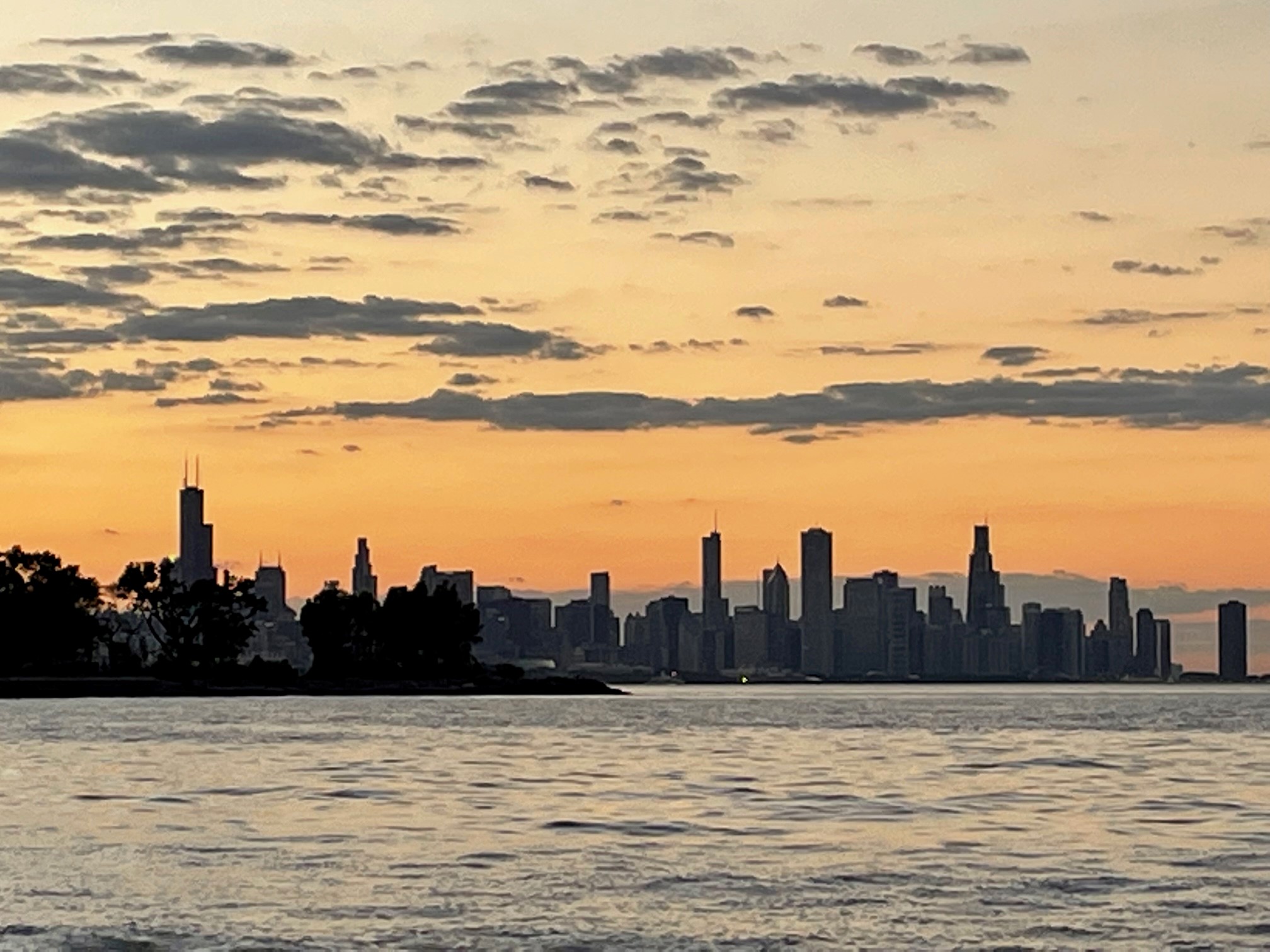
Chicago PMI dips 0.1 points in June
The Chicago Purchasing Managers Index (PMI) slipped 0.1 points to 40.4 points, in June.
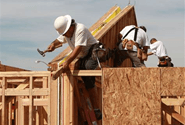
Multi-family pullback drives housing starts to 5-year low in May
US housing starts tumbled in May to a five-year low, according to figures recently released by the US Census Bureau.
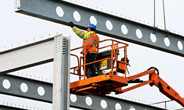
Architecture firms still struggling, ABI data shows
Architecture firms reported a modest improvement in billings through May, yet business conditions remained soft, according to the latest Architecture Billings Index (ABI) release from the American Institute of Architects (AIA) and Deltek.