SMU Data and Models
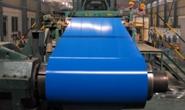
Steel Buyers Basics: Painted Steel Price Calculator
Written by Mario Briccetti
March 21, 2014
Editor’s note: Leading paint suppliers have announced price increases effective in January, which will impact the market for prepainted steel and aluminum (see related article). The following SMU Steel Buyers Basics article authored by Mario Briccetti and reprinted from March 2014 explains how the cost of the paint calculates into the cost of prepainted products.
Buyers of coil coated painted steel do not actually purchase any paint, they purchase the service of painting from a coil coater – the coil coater buys the paint as part of the service they supply. Typically, an end buyer never sees the actual price of the paint and only sees the resulting impact on the cost of the painting service. This article explains the amount of paint that is typically used in this process so that buyers can better understand what ability they have to negotiate paint increases.
Typically, painted steel goes through the following processes:
Cleaning (both sides)
Pretreatment (both sides) so the primer coat will stick
Primer coat (both sides)
Backer coat (usually thin, protects the top coat when the steel is coiled up)
Finish or top coat
In a modern coil coating process, these steps are all done (at high speed) in one pass through the coil coating line. Some types of coatings require multiple passes through the coating line.
The largest drivers for coil coating costs are the chemicals to clean and pretreat the steel, the primer paint, the backer paint and the topcoat paint. In addition to these costs are the capital costs of the coil coating equipment, the overhead costs (particularly natural gas to run the paint curing furnaces) and labor cost associated with running the equipment. So if paint costs rise by 4 percent, what is a fair increase in the overall cost of coating steel?
Buyers can determine this if they know the amount of paint used per ton of the steel they have painted. In order to figure that out, first determine the total square feet of the steel per ton and then the amount of paint used per square foot of coil. For instance, 24-gauge galvanized steel (I’ll use 0.024” thickness) x 48 wide theoretically has 2,043 square feet of steel per ton.
A gallon of high-end Kynar paint might cost $100 and be applied at an average film thickness of 0.75 mills. However, most of the paint is solvent (perhaps 60 percent) that evaporates during curing, so only 40 percent of the gallon of paint remains to create the film thickness (known as DFT). There are 231 cubic inches in a gallon of liquid, so one gallon of paint (with 40 percent solids remaining after curing) will cover 856 square feet of coil. Thus, it will take 2.39 gallons of paint to cover one ton of coil.
Painted ft2 per gallon = (0.40 * 231 in3/gal) / (0.00075in *144in2/ft2) = 856 ft2/gal
Gallons/ton = 2,043 ft2/ton / 856 ft2/gal = 2.39 gal/ton
At $100 per gallon, the cost for just the topcoat paint (and only the top coat) is $239/ton or $11.94/cwt. A 4 percent per gallon paint increase means that the actual paint cost increase (again just for the single top coat layer) is about $0.48/cwt. While the topcoat price may be the largest factor in the cost of coil coating, there are many other factors including the costs of the primers, pretreatment, backer and all the other overhead costs that go into coil coating. Buyers should estimate all of these costs (using the same method presented for the top coat) before negotiating pricing.
Typically, coaters will ask for increases for themselves whenever the paint suppliers increase their prices. In negotiation, information is power — astute buyers should try to separate out the paint increase from the additional costs for the coil coater. Be aware, each color of paint, each type of paint and each type of primer will have its own cost per gallon, its own percentage of solids remaining after curing and its own applied thickness – that’s what spreadsheets are for.
Mario Briccetti
Read more from Mario BriccettiLatest in SMU Data and Models
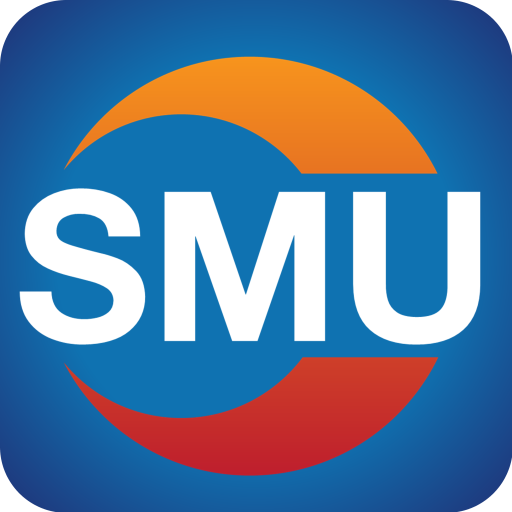
SMU Scrap Survey: Sentiment Indices rise
Both current and future scrap sentiment jumped this month, though survey participants reported responses before key trade news was announced.
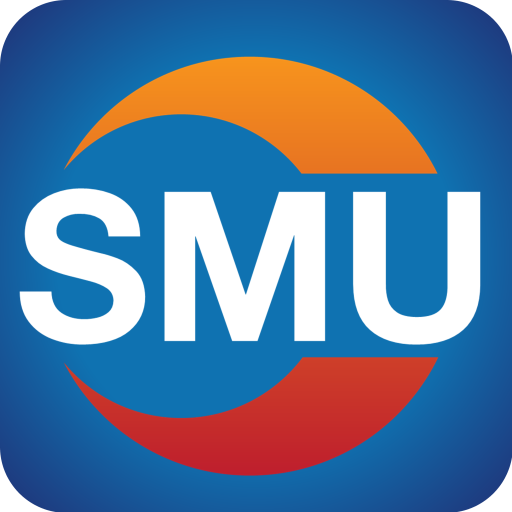
SMU Survey: Sentiment splits, buyers have better view of future than the present
SMU’s Steel Buyers’ Sentiment Indices moved in opposite directions this week. After rebounding from a near five-year low in late June, Current Sentiment slipped again. At the same time, Future Sentiment climbed to a four-month high. Both indices continue to show optimism among buyers about their company’s chances for success, but suggest there is less confidence in that optimism than earlier in the year.
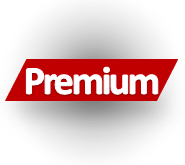
SMU scrap market survey results now available
SMU’s ferrous scrap market survey results are now available on our website to all premium members. After logging in at steelmarketupdate.com, visit the pricing and analysis tab and look under the “survey results” section for “ferrous scrap survey” results. Past scrap survey results are also available under that selection. If you need help accessing the survey results […]
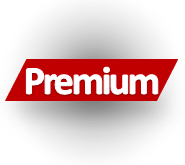
SMU flat-rolled market survey results now available
SMU’s latest steel buyers market survey results are now available on our website to all premium members. After logging in at steelmarketupdate.com, visit the pricing and analysis tab and look under the “survey results” section for “latest survey results.” Past survey results are also available under that selection. If you need help accessing the survey results, or if […]
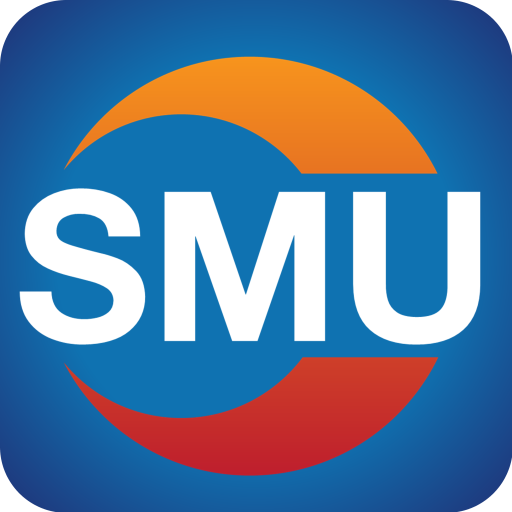
SMU Survey: Sheet lead times stabilize, plate contracts
Mill lead times for sheet products were steady to slightly longer this week compared to our late June market check, while plate lead times contracted, according to steel buyers responding to this week’s market survey.