Steel Mills
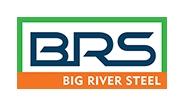
SMU Steel 101 Tours Big River Steel
Written by John Packard
November 16, 2016
On Tuesday of this week Steel Market Update (SMU) and one of our Steel 101: Introduction to Steel Making & Market Fundamentals workshops toured the Big River Steel facility in Osceola, Arkansas. We conducted the classroom portion of our program in Memphis and then drove to the mill for our tour and then we moved over to The Grange at Wilson Gardens for a special reception and dinner with BRS management, customer support staff and our attendees and staff.
Big River Steel has to be one of the largest construction sites in the United States with close to 1900 contractors on site the day we visited the plant. They are working toward bringing the mill to life in the coming weeks as they prepare to fire up their first electric arc furnace and run their first bars into the hot strip mill.
The amount of construction activity was daunting and, unfortunately, we were unable to climb onto certain pieces of equipment as they were either in the process of being commissioned or they were surrounded with workers putting the finishing touches on the equipment.
Mark Bula, Chief Commercial Officer for Big River Steel, told us that the mill has a number of orders to run before the end of the year and everyone seemed anxious to make it happen.
We were able to walk the furnace, ladle metallurgical station, hot strip mill, pickle-tandem cold mill and galvanizing line. From our untrained eye there appeared to be a large amount of work to be done before the first coils get run, but we do not doubt that sometime in the next few weeks the first coils will come off that HSM.
One of the attendees in our workshop was the Executive Director of the Arkansas Teacher Retirement System which has a 20 percent equity stake in the mill. When asked why the mill hadn’t run its first coils earlier this year, he told us that the mill had made a decision to switch which furnace was going to come online first from the original plans. The switch created engineering work for SMS who designed and is building the equipment and software. This put the mill three to four months behind schedule.
Nonetheless, the people at Big River Steel were very accommodating and professional throughout the process of coordinating the tour and working with our group. We want to take a moment to thank the mill’s CEO, David Stickler, Chief Commercial Officer Mark Bula and the Manager of Technical Services, Mark Orvis as well as the rest of the hard-working BRS teammates for their hospitality.
We have been invited to come back and we will hold them to their invitation as we would like to see the mill as a fire-dragon beast melting scrap and making steel in the months ahead.
Our next Steel 101 workshop will be held in Huntsville, Alabama and will include a tour of the Nucor Decatur sheet mill with its automotive quality galvanizing facility. The workshop is already two-thirds of the way to being sold out so we recommend if you are interested to register as soon as possible. You can find more information and register either online or through our office: 800-432-3475/706-216-2140.

John Packard
Read more from John PackardLatest in Steel Mills
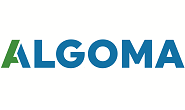
Algoma fires up EAF steelmaking with first arc
Algoma Steel reached a milestone in its transformation from blast furnace to electric arc furnace (EAF) steelmaking, with its Unit One EAF achieving its first steel production this week.
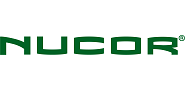
Nucor holds HR list price at $910/ton
Nucor is keeping its list price for spot hot-rolled coil unchanged after last week’s shortened holiday week.
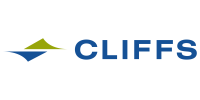
Cliffs unveils new hydrogen-powered stainless line in Ohio
CEO Lourenco Goncalves, flanked by state leaders and union reps, touted the project as proof that US manufacturing is not only alive, but also advancing.
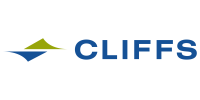
Cliffs idles Steelton, Riverdale, and Conshohocken operations
Cliffs has idled facilities in Riverdale, Ill., and Conshohocken and Steelton, Pa.
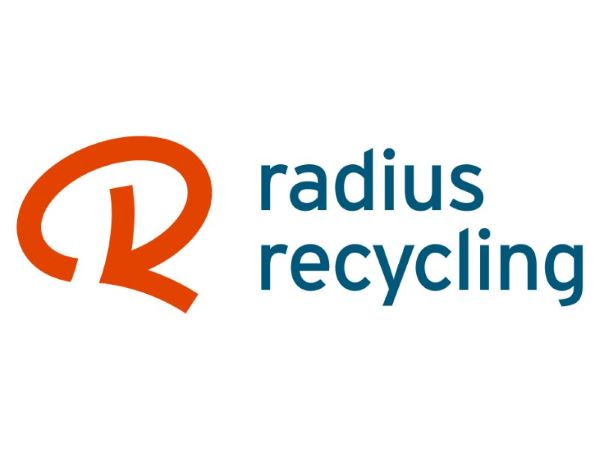
Radius loss narrows, volumes climb in ‘healthy’ West Coast market
Stronger steel demand in the Western US, rising scrap flows, and improved rolling mill utilization drove sequential gains for Portland, Ore.-based Radius Recycling.