SMU Data and Models
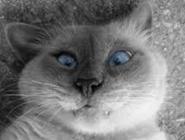
Steel Buyers Basics: Kobe Steel Problems and How to Avoid Them
Written by Mario Briccetti
October 21, 2017
SMU Note–The Kobe Steel scandal regarding falsifying test certifications has had a ripple effect. Steel Market Update asked those responding to our flat rolled steel market trends questionnaire if the Kobe scandal is raising some concerns that other mills may cut corners with testing and falsify documentation. Twenty-nine percent of our respondents had concerns.
From our background and experience, we are not aware of a single steel mill located in the United States or Canada that would falsify data.
The following article is written by Mario Briccetti of Briccetti and Associates as advice to steel buyers and operations people who have concerns:
Kobe Steel recently discovered that, for a range of metal products, employees had either falsified certification data or skipped the agreed-upon testing. These revelations have been very disturbing to Kobe’s customers, who used this suspect metal in everything from trains, planes to automobiles.
Beyond the Kobe situation, customers throughout worldwide supply chains are wondering how much of this type of activity (or lack of activity) takes place at their suppliers, and what to do about it. Problems can occur at any point in the chain, from overseas material, to the local service center, through toll coaters, etc. How does a customer make sure their supplier is meeting all of their promised product specifications? How much testing of parts should customers be doing themselves?
Unfortunately, most customers tend to rephrase this question into: How do I make sure I have no liability for this type of activity? One answer: So long as parts work in the application, just keep ignorant. I suspect more of this sort of thing is happening than people want to acknowledge.
There are several potential reasons suppliers don’t perform agreed-upon testing or falsify certification data. One reason, of course, is that they are simply dishonest and don’t care about their customers. This article is not about that kind of supplier. And I don’t believe Kobe is that kind of supplier. After discovering their problems, they didn’t hide that information but announced it. You can read their communications at http://www.kobelco.co.jp/english/
A second related supplier specification violation is also about saving money, but doing so in a way that the supplier does not believe will affect part quality. For instance, if a customer specifies G60 galvanized material, that means that G60 is the minimum possible coating weight — not an average. So the coater will target their process somewhat higher than G60 to maintain that minimum.
In my mill visits, I’ve seen that coating safety margin set anywhere from 1 percent to 6 percent. But giving away 6 percent on the galvanizing coating is expensive, and the pressure to cut this safety margin is ever present. What if only 1 part in a million of the coating surface fell under G60? How about 1 part in a billion or a trillion? Given that every process has some tolerance that tends to follow a bell curve, is it really even possible to be 100 percent sure of the coating thickness everywhere?
Galvanizing coating is just one example. Steel thickness tolerance, paint coating tolerance, and alloy percentage tolerance are all examples of where this type of specification violation might occur because of cost pressure. I know that some suppliers are much more aggressive in this area than others. As long as parts from suppliers are processed and perform without problems, no one notices that small percentages of shipped steel might be slightly under these types of specifications.
A third reason specifications sometimes are not maintained is because an expert knows that certain specifications can be violated without impairing the part quality. For instance, steel specs typically contain both carbon and manganese percentage ranges and a targeted tensile strength and elongation percentage. However, only the tensile strength and elongation percentage may be important to the application. An expert realizes that manganese and carbon have a trade-off effect on tensile and elongation. Steel that is low in carbon but high in manganese could be well-suited to the application even though it is outside of the specified range. When a material shortage occurs, and the customer is both inflexible and punitive, a metallurgist might be very tempted to fudge the certified specifications in order to keep a customer up and running.
A fourth reason actually has been described by Kobe as part of their problem. They were supposed to test tensile strength on an aluminum part but did not. Instead they only tested hardness. Kobe claims that tensile can be calculated based on hardness, so they certified that calculated value instead of actually performing the test like they were supposed to.
Is any of this behavior ethical? No. Is it illegal? Yes. Does it happen in the real world? My sources tell me it will never happen in a domestic steel mill. However, for foreign mills and downstream of the mill, they are not so sure. And once a supplier starts down this road, they can find it very hard to stop. It can ruin a company. I strongly suspect that if all suppliers underwent the scrutiny that Kobe is facing today, some number of them would at least have some explaining to do. Warren Buffet has a saying – only when the tide goes out do you see who is swimming naked.
How should a buyer avoid this kind of problem? Here are some general guidelines:
First, don’t deal with disreputable suppliers. Check out any supplier carefully before you start a relationship. For current suppliers, keep an eye on their financial performance. Companies under financial stress put that stress on their employees, who in turn become more likely to cheat. Be prepared to act if you lose faith in a supplier. The hardest part of following this rule is when the suspect supplier has the best price – a buyer should always look at value instead of price.
Second, buyers should visit their suppliers and understand each supplier’s processes. Get to know some of the operations people at your supplier – they are a direct source of information on how the supplier is performing. An educated buyer has a far better chance of detecting supplier specification cheating than does an uninformed buyer.
Third, buyers should make sure the record keeping for the steel they buy is properly kept both at their own company and at their suppliers. Steel coils all have a number that is traceable back through its processing to the mill’s heat batch. Without traceability, a buyer is completely lost when facing an issue similar to the Kobe problem. In this age of cheap computer storage, there is no excuse for losing traceability data.
Fourth, a buyer should work to establish a trusting relationship with suppliers. When problems occur, rather than put a stick into the eye of the supplier, try to work through the problem. In my example about carbon and manganese, approve the use of the steel with the higher manganese.
Fifth, make sure that part specifications are correct and understood by both parties. Don’t over-specify (something I had a tendency to do when I was an engineer). Periodically have your team and your supplier review part specs to ensure they are relevant and important.
Finally, don’t completely trust your suppliers. Set up a program to periodically test their parts yourself (or hire a third party to do it). Test those specs that a supplier might be tempted to cheat on (like coating weight and steel thickness) or that are critical to your end product. Take the time to rate your key suppliers on how well they perform.
To end on a positive note, a good supplier will accept responsibility and accept liability that comes with systematically failing to make parts correctly. A supplier such as Kobe that has lied to its customers is in terrible trouble now, but can recover. If Kobe takes the blame, shares the pain and protects customers through this disaster, no matter the cost to themselves, they might find, in the long term, they have built a relationship customers will come to appreciate.
About the Author: Mario Briccetti is the principal of Briccetti and Associates. He is a former engineer and has held top purchasing positions in the manufacturing and distributor segments of the industry. Briccetti is also an instructor for the SMU Steel 101 workshop. He can be reached at MarioBriccetti@gmail.com.
SMU Note: In response to the above commentary, a former quality assurance division manager for integrated mills offered the following comment: “After working for over 40 years in various quality positions for different integrated steel companies, the process of testing and certification of these test results has veracity. Each mill had a quality assurance manual that details practices and procedures that must be adhered to within the course of manufacturing and compliance to standards. Internal audits to determine compliance to these standards were done annually. In addition to internal audits, we were required to have two surveillance audits annually by our registrar. These outside audits took at least four days with hundreds of hours of preparation. The consequences of a major find could result in decertification. In the case of Kobe Steel or any other mill that permits this behavior of falsifying mill test reports, the top executives and top quality personnel should all be fired. The next step should be that each individual be prosecuted. For those who may question the veracity of the test reports from their mill source, request an audit and see for yourself.”
Mario Briccetti
Read more from Mario BriccettiLatest in SMU Data and Models
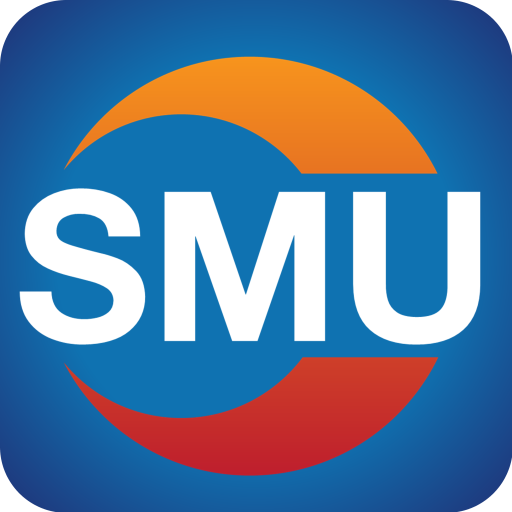
SMU Survey: Buyers’ Sentiment rebounds from multi-year low
Both of SMU’s Steel Buyers’ Sentiment Indices edged higher this week. Current Sentiment rebounded from a near five-year low, while Future Sentiment rose to a two-month high
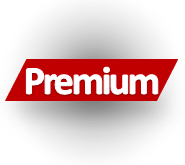
SMU flat-rolled market survey results now available
SMU’s latest steel buyers market survey results are now available on our website to all premium members.
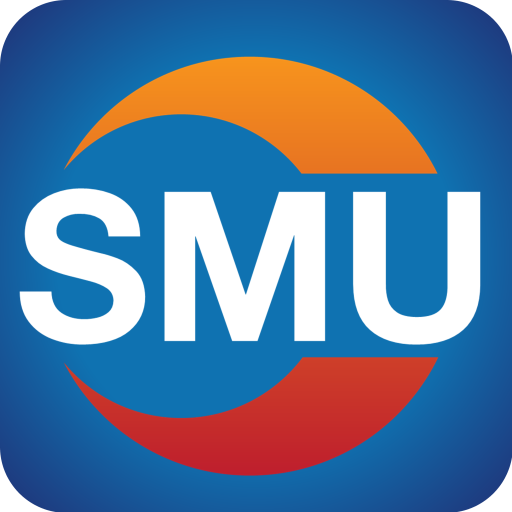
SMU Survey: Sheet lead times pull back after early-June blip, plate holds
Following the uptick seen two weeks ago, lead times eased this week for all four sheet products tracked by SMU, while plate lead times held steady, according to this week’s market survey.
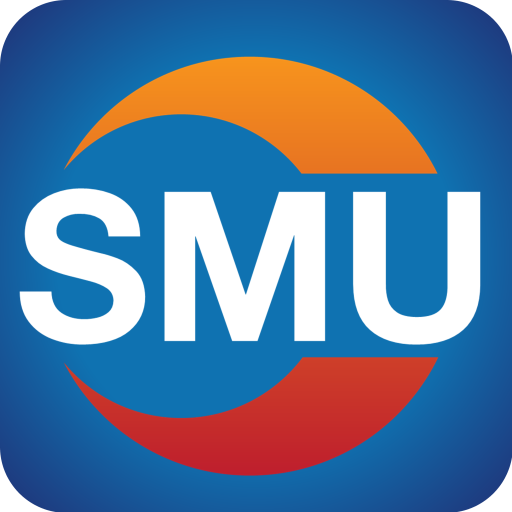
SMU Survey: Pricing power abruptly shifts to steel buyers
The majority of steel buyers responding to our latest market survey say domestic mills are more willing to talk price on sheet and plate products than they were earlier this month. Sheet negotiation rates rebounded across the board compared to early June, while our plate negotiation rate hit a full 100%.
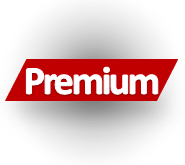
Service centers: Mill orders down marginally in May
SMU’s Mill Order Index (MOI) declined for a third straight month in May, but only marginally.