Steel Mills
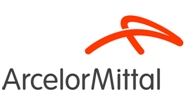
ArcelorMittal and Honda Co-Engineer AHSS Solutions
Written by Sandy Williams
May 17, 2018
The U.S. steel industry continues to find new ways to help automakers lighten vehicles for better fuel efficiency.
One of the latest developments is by ArcelorMittal in partnership with Honda. Engineers from the two companies designed the industry’s first hot-stamped, laser-welded inner and outer door ring using ultra-high-strength steel. The system replaces conventional multi-piece, spot weld designs.
ArcelorMittal debuted an outer door ring for the 2014 Acura MDX, but the newest evolution in 2018 utilizes a new double-ring rear frame design and new two-piece ultra-high-strength steel front door rings, which significantly increase body rigidity.
“A vehicle’s front body structure – or the area surrounding the driver and passenger – consists of a ring that serves as a critical part of the safety cage. The outer ring is where the doors and styling components affix, while the inner ring is where the airbags and all interior features attach,” said Joe Riggsby, Acura RDX body development leader, Honda R&D Americas. “Together, they make a continuous structure that encompasses the front door opening and offers a solution that is very stiff.”
The inner and outer door ring system makes the vehicle safer by transferring loads coming from the front of the vehicle to the back of the structure, as well as protecting occupants from side crashes.
The inner door ring is comprised of five different gauges of ArcelorMittal’s patented press hardenable steel, Usibor® 1500, while the outer door ring is comprised of four gauges of Usibor® 1500. The Usibor steel blanks are made at a blanking company, then shipped to ArcelorMittal’s Tailored Blanks facility in Detroit where the enabling technology, called laser ablation, takes place. Once ablated, the steels are welded together, with multiple quality control processes ensuring precision. The blanks are then sent to a hot-stamper to be stamped into the final part required by the automaker.
Honda introduced the new system at the SAE World Congress Experience in Detroit in January on its 2019 Acura RDX. Honda also increased its use of ultra-high-strength steels in the RDX by more than 50 percent, reducing the weight of the vehicle by 42 pounds.
“We see the door ring and our hot-stamped solutions continue to move through the industry,” said ArcelorMittal Tailored Blanks representative Todd Baker. “We are working with more customers to implement them into more vehicles, and we see it taking place across vehicles lines. The application isn’t just limited to SUVs and minivans; we are seeing it in pickup trucks and small cars. This validates our belief that the door ring and hot-stamped welded blanks offer a cost-effective way to make vehicles safer and lighter.”
Honda Motor Company was presented the Automotive Excellence Award on May 16, 2018, from the American Iron and Steel Institute for the use of advanced high-strength steels in its 2018 Honda Odyssey. The chassis uses a Next-Gen Advanced Compatibility Engineering (ACE) body structure in combination with tailor-welded hot-stamped door rings and a new multi-connection bumper beam to enhance occupant protection. The Odyssey is comprised of 58 percent high-strength steel leading to high rigidity and a lightweight body.
The Steel Market Development Institute (SMDI) reported that more than 60 steel-intensive vehicles debuted at auto shows this year, in every major vehicle segment and size. In the last four years, the amount of AHSS used in automotive applications has been 10 percent higher than forecast, said SMDI.
“With so many new steel-intensive vehicle debuts across key vehicle segments, it truly reinforces how advanced high-strength steel (AHSS) is driving innovation across the industry and helping automakers reach their lightweighting targets,” said Jody Hall, vice president of the automotive market for SMDI. “There are more than 200 grades of innovative AHSS available to automakers today. This allows engineers to apply the right grade in the right location for exceptional occupant protection, durability and crash energy management.”
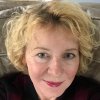
Sandy Williams
Read more from Sandy WilliamsLatest in Steel Mills
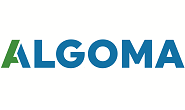
Algoma fires up EAF steelmaking with first arc
Algoma Steel reached a milestone in its transformation from blast furnace to electric arc furnace (EAF) steelmaking, with its Unit One EAF achieving its first steel production this week.
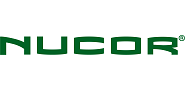
Nucor holds HR list price at $910/ton
Nucor is keeping its list price for spot hot-rolled coil unchanged after last week’s shortened holiday week.
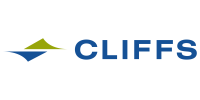
Cliffs unveils new hydrogen-powered stainless line in Ohio
CEO Lourenco Goncalves, flanked by state leaders and union reps, touted the project as proof that US manufacturing is not only alive, but also advancing.
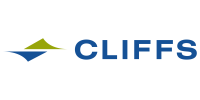
Cliffs idles Steelton, Riverdale, and Conshohocken operations
Cliffs has idled facilities in Riverdale, Ill., and Conshohocken and Steelton, Pa.
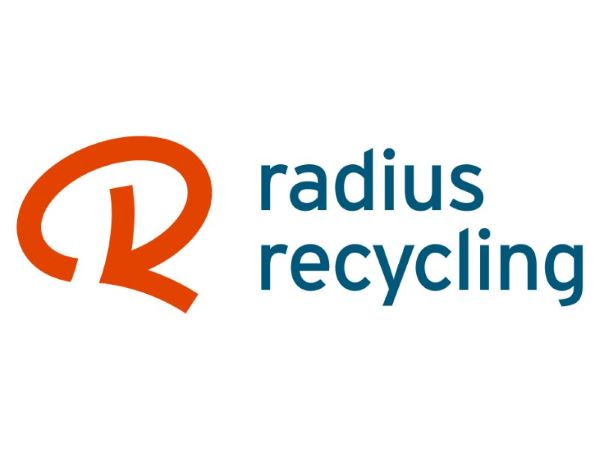
Radius loss narrows, volumes climb in ‘healthy’ West Coast market
Stronger steel demand in the Western US, rising scrap flows, and improved rolling mill utilization drove sequential gains for Portland, Ore.-based Radius Recycling.