Steel Mills
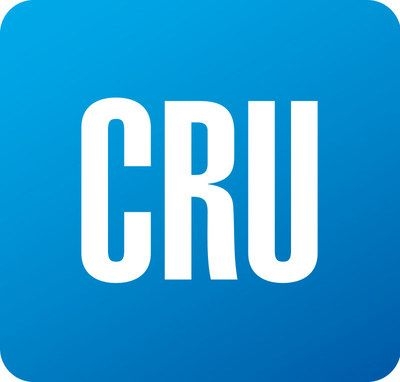
CRU Explains: Flexibility in the Steelmaking Chain
Written by Paul Butterworth
May 7, 2020
By CRU Research Manager Paul Butterworth and Analyst Alexander Ordosch, from CRU’s Global Steel Trade Service
The global Covid-19 outbreak has resulted in sharply falling steel demand all over the world. For the steel industry, it is a challenging task to reduce production levels as ~75 percent of global output is produced through the BF/BOF, or integrated steelmaking, process route. In our previous insight “CRU Explains: How Blast Furnaces Can be Idled” we covered options for cutting blast furnace (BF) production, but a BF is only one element in the steelmaking chain. In this insight, we want to cover the other vital steps for steel production and explain where the inflexibility exists.
Coke Batteries are More Inflexible than Blast Furnaces
By-product recovery coke batteries suffer from inherent inflexibility because it is difficult to adjust productivity, very costly to hot idle and practically impossible to cold idle. A coke battery heats coking coal under high temperatures without oxygen for many hours to adjust the technical properties of the coke. As a first step, utilization can be lowered by increasing coke heating time, but there are narrow limits for that. As a next step, costly hot idling can be attempted requiring natural gas to keep idled parts of the battery at operating temperature. Cold idling is normally not possible because a complete rebuild of the coke battery would be necessary before restart that takes months and costs tens of millions of dollars (this may not apply to non-recovery batteries that account for a smaller percentage of coke capacity globally).
With BF production being cut by >100 Mt worldwide, coke consumption is also significantly lower, posing a challenge for coke batteries to adjust production. We understand that one coke battery in Europe has been hot idled, taking advantage of low gas prices; others have reduced capacity utilization to the bare minimum while declaring force majeure on their coking coal contracts. In contrast, Japanese coke producers are still processing contracted volumes of coking coal although domestic coke demand has plummeted. Therefore, we currently see increased coke exports to China and quick coke inventory build in Japan.
Sintering, DRI Making and Steelmaking are More Flexible
• Sintering is a process to make fine-grained iron ore suitable for use in a BF. CRU understands that this process can be well adjusted to changing demand.
• DRI making is more flexible than ironmaking in a blast furnace. While there are difficulties operating a BF below 75 percent (see chart below), DRI facilities can easily operate as low as 50 percent capacity utilization. DRI production can also be turned off in a matter of hours and hot idling for several days is also possible.
• Covid-19 restrictions have recently forced temporary shutdowns of Nucor’s DRI facilities in Louisiana and Trinidad. However, a shortage of prime grades in the USA is currently incentivizing the restart of facilities, despite the fact that sheet demand is weak. Therefore, DRI making in Louisiana has recommenced and startup of production in Trinidad is expected soon.
• Steelmaking in a basic oxygen furnace (BOF or converter) or electric arc furnace (EAF) is a flexible process. EAFs can technically operate at any capacity utilization between zero and 100 percent. Steelmaking in a BOF can also be adjusted because an integrated mill typically operates several converters, which can be idled individually. While an EAF can decide whether to operate based on steel margins, a BOF is less flexible because it gets most of its input (i.e. hot metal) from the inflexible BF and can only adjust steel output via the scrap rate within narrow limits.
CRU has tracked idled EAFs worldwide and we understand that most of the still running EAFs are operating at low melting rates. Most EAFs outside the USA produce long products that enjoy comparably healthy demand. Most flat-rolling EAF capacity is in the USA and severe sheet demand weakness has forced them to cut production.
Casting and Rolling Can Adjust to Steel Demand
Casting and rolling are quite flexible processes that are disconnected via the semis yard. However, there are some rolling and surface treating processes that may not run well at low capacity utilization like continuous cold-rolling or annealing facilities and galvanizing lines. Due to steel demand weakness, many steelmakers have closed not only their hot end, but also their rolling facilities, particularly affecting flat rolling operations.
The semis yard can be used to keep the hot end operating while rolling output is reduced, or to keep the rolling mills running while the hot end is idled. The latter mode is commonly used before a planned BF outage (e.g. reline); semi stock is built and consequently rolled while the BF is down.
We saw Chinese mill stocks skyrocket during February-March 2020. The semis yard was one place to store large volumes of crude steel while finished steel demand fell sharply and steel production continued.
Blast Furnaces and Coke Batteries are the Bottlenecks for Flexibility
The coke battery is the most inflexible element of the steelmaking process followed by the blast furnace. Alternative ironmaking and raw material processing facilities such as DRI and sinter plants can adjust utilization lower. An EAF is inherently flexible being able to operate between zero and 100 percent utilization without major problems. Casting and rolling are also flexible processes that are decoupled via the semis yard—intermediate storage that provides flexibility to absorb short-term steel demand fluctuations.
Request more information about this topic.
Learn more about CRU’s services at www.crugroup.com
Paul Butterworth
Read more from Paul ButterworthLatest in Steel Mills
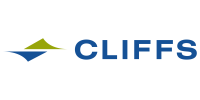
Cliffs idles Steelton, Riverdale, and Conshohocken operations
Cliffs has idled facilities in Riverdale, Ill., and Conshohocken and Steelton, Pa.
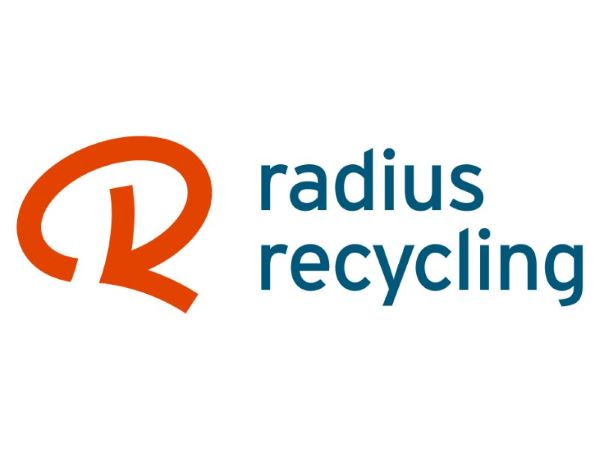
Radius loss narrows, volumes climb in ‘healthy’ West Coast market
Stronger steel demand in the Western US, rising scrap flows, and improved rolling mill utilization drove sequential gains for Portland, Ore.-based Radius Recycling.
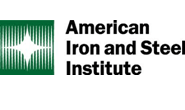
AISI: Raw steel production backs off multi-year high
US raw steel output edged lower last week after hitting a multi-year high in mid-June, according to the American Iron and Steel Institute (AISI).
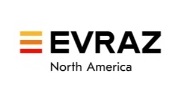
Private equity firm Atlas Holdings to acquire Evraz North America
Atlas Holdings said it has signed a definitive agreement to acquire Evraz North America (Evraz NA). The Greenwich, Conn.-based private equity firm said it expects the deal for the Chicago-based steelmaker to close in the second quarter of 2025 subject to various closing condition.
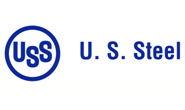
Granite City Works must remain open and other terms of the Nippon-USS deal
SEC documents also name Trump specifically as having veto power certain decisions are part of the “Golden Share” provision.