Steel Markets
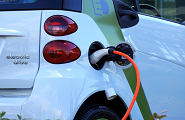
SMU Steel Summit: Electric Vehicles a Growth Market for Steel
Written by Brett Linton
August 27, 2021
Electric vehicle (EV) sales have gotten a big boost from President Biden’s pledge to reduce harmful CO2 emissions. And the Biden administration’s infrastructure bill now under debate in Congress, which includes $7.5 billion in funding for a nationwide network of EV charging stations, could go a long way toward reducing the “range anxiety” that is keeping many consumers from embracing emissions-free cars and trucks, said John Catterall, vice president of the American Iron and Steel Institute’s Automotive Program.
Speaking to the crowd at SMU’s Steel Summit in Atlanta on Wednesday, Catterall noted that the rate of EV sales is now outpacing sales of conventional internal combustion engine (ICE) vehicles. Globally, light vehicle sales for the first half of 2021 increased by 21% from the first half of 2020. In that same time frame, EV sales increased 172%. In the U.S. alone, total light vehicle sales rose 30%, while EV sales were up 168%. This spread could be slightly amplified by the tight supply of new vehicles due to the microchip shortage or excess cash that buyers have after being shut in by the pandemic, but it is showing an emerging trend in favor of EVs. Projections show that by 2030, EVs could account for 50% of global passenger car sales.
Catterall addressed affordability as well, noting that EV battery costs will continue to decline as the technology advances, making the overall cost of each EV cheaper. His data suggests that by 2025, the cost to manufacture an EV could be similar to an internal combustion engine (ICE) car. As EVs become better packaged and batteries more integrated, the mass of the vehicle will decrease and will also help drive down costs.
Steering the presentation towards vehicle design, Catterall said it is important that the EV battery structure is protected from any impacts or compression from an accident, which is best accomplished using very high-strength steel. Namely martensitic grades, press hardened steel grades, and now third-generation high-strength austenite grades. Using steel “gives engineers a lot of latitude” says Catterall, compared to other materials such as aluminum or composites. Steel continues to account for a large percentage (52%) of the material content in light-vehicles, according to the below chart.
Aluminum remains a threat to steel, as emerging EV producers aiming for longer ranges want the lightest structure possible. At one-third the mass of steel, aluminum would seem to be a viable solution. However, Catterall said, steel and auto industry research shows that the weight savings from aluminum are not that great compared to thin-gauge high-strength steels. Aluminum can’t protect the batteries as well as steel in a crash, and aluminum holds additional costs in terms of forming and joining. Plus, the OEMs are already equipped to work with steel sheet.
Asked about the environmental impact of the batteries themselves, Catterall said, “I think we need to see a lot more life cycle analysis. Right now we do have an issue, as the initial production of those batteries is probably not where is needs to be from a sustainability standpoint.” The battery packs are designed to be in service for at least 10 years and to be high-performing that entire time. After that they don’t head to the landfill, however, they are still very usable for other applications such as solar panel energy storage. There are not enough batteries in the field yet, he added, but eventually companies will see a business opportunity and try to profit off their recycling.
By Brett Linton, Brett@SteelMarketUpdate.com
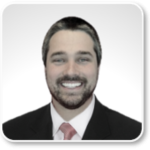
Brett Linton
Read more from Brett LintonLatest in Steel Markets
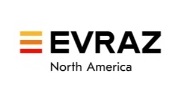
USW cheers Evraz NA agreement with Atlas Holdings
The United Steelworkers (USW) labor union celebrated recent news of the signed agreement between Atlas Holdings and Evraz NA in which the Connecticut-based private equity company said it plans to acquire North America’s Evraz facilities.
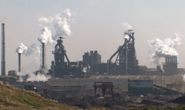
Steel buyer spirits tempered by soft spot market conditions
Steel sheet buyers report feeling bogged down by the ongoing stresses of stagnant demand, news fatigue, tariff negotiations or implementation timelines, and persistent macroeconomic uncertainty.
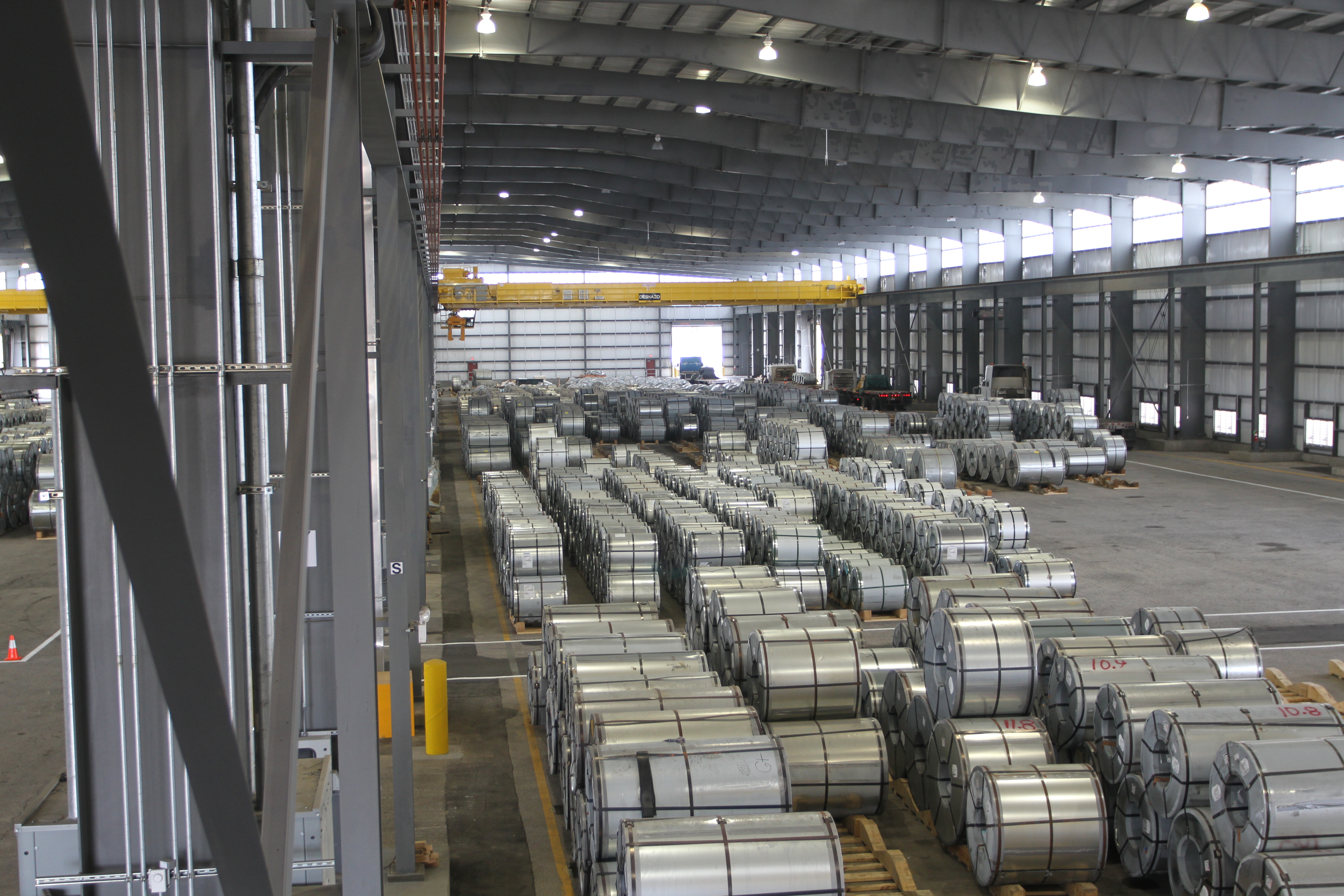
Hot-rolled coil buyers continue seeking certainty
Steel market participants contend that buyers will remain in “wait-and-see" mode until some market stability is restored.
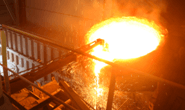
Latin American steel advocates warn on cheap import flood
Subsidized Chinese steel imports and cheap steel products from Association of Southeast Asian Nations (ASEAN) entering Latin American (LATAM) are threatening the region's steel market.
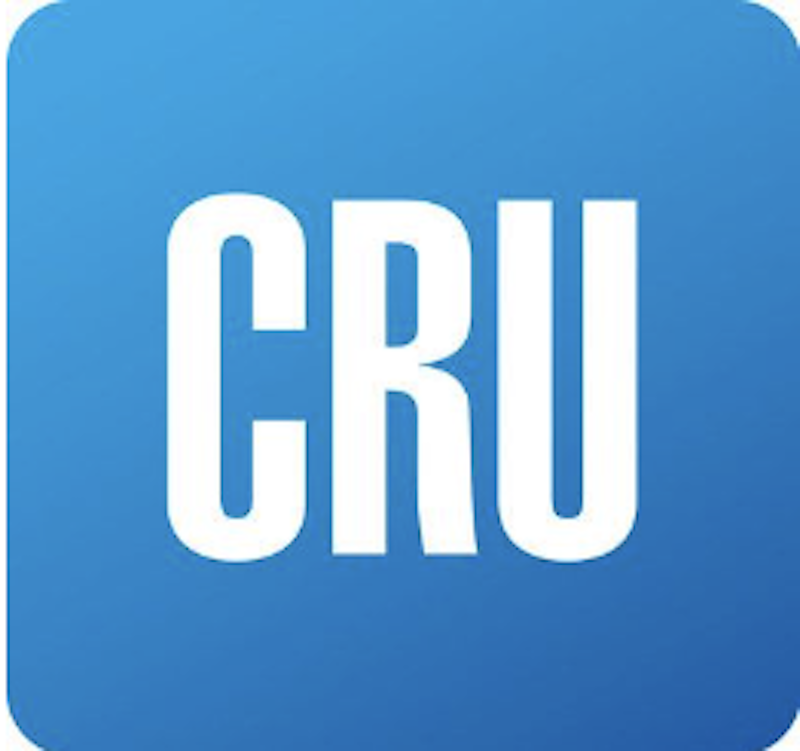
CRU: Steel prices fall amid global demand weakness
The forceful headwinds bearing down on steel markets across the globe have created demand challenges and sent prices southward. The US, however, challenged the global trend.