Steel Mills
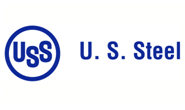
U.S. Steel Doubles Down on Endless Casting Technology
Written by Tim Triplett
January 19, 2022
Among the attributes of the new, advanced minimill U.S. Steel plans to build in Osceola, Ark., next to its Big River Steel plant, is endless casting and rolling technology that will make the facility the first of its kind in the United States. What is endless casting and rolling, and what competitive advantages will it bring to U.S. Steel?
The technology, which has been used in Europe for more than a decade, uses thin slab technology in a continuous process that can transform 250 tons of liquid steel into coiled sheet every 40 minutes, offering significant savings in time and energy.
Using special flow control of molten alloy steels at temperatures of 3,000 degrees, the system solidifies a 4-inch-thick bar of steel, up to 77 inches wide, and continuously rolls the thin slab into 40-ton coils as thin as 0.030 inch, the steelmaker said in an email to Steel Market Update.
Such equipment was part of U.S. Steel’s plan a few years ago for a $1 billion upgrade to its Edgar Thomson Plant in Braddock, Pa. That project was killed in April 2021 for environmental and other reasons, but the plan for endless casting and rolling lives on at Osceola.
U.S. Steel said its new minimill in Arkansas will house two electric arc furnaces with a total of 3 million tons of annual steelmaking capacity, but offered no further detail on the rationale for the endless casting and rolling technology, though some inferences can be drawn from the press reports back in 2019.
U.S. Steel was planning to emulate the Endless Strip Production process used by Italian steel producer Acciaieria Arvedi S.p.A.’s (Arvedi). In the original plan, equipment supplier Primetals Technologies was to supply an Arvedi ESP at Edgar Thompson with a rated capacity of 2.76 million short tons of ultra-thin strip at a maximum width of 77 inches, making it the widest ESP line ever built.
According to its developers, the ESP process offers savings in energy consumption of up to 45% over conventional casting and rolling, as well as a significant reduction in CO2 emissions. Due to the continuous rolling, strip can be produced with uniform and repeatable mechanical properties along its entire length. Head and tail end croppings are virtually eliminated, reducing yield loss.
The system’s suppliers claim the quality of endlessly cast products is as good or better than a conventional hot-strip mill, producing steel with outstanding surface quality suitable for the most demanding automotive and appliance applications. Hot-rolled thin strip produced with continuous casting and rolling is said to be good enough for some cold-rolled strip applications.
When completed in 2024, U.S. Steel said its sophisticated new steelmaking facility in Osceola, in combination with the adjacent Big River Steel, will form a “mega mill” with EAF capacity of 6.3 million tons per year, moving the company closer to its goal of a 20% reduction in GHG emissions by 2030.
By Tim Triplett. Tim@SteelMarketUpdate.com
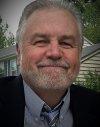
Tim Triplett
Read more from Tim TriplettLatest in Steel Mills
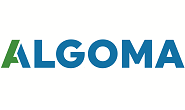
Algoma fires up EAF steelmaking with first arc
Algoma Steel reached a milestone in its transformation from blast furnace to electric arc furnace (EAF) steelmaking, with its Unit One EAF achieving its first steel production this week.
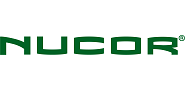
Nucor holds HR list price at $910/ton
Nucor is keeping its list price for spot hot-rolled coil unchanged after last week’s shortened holiday week.
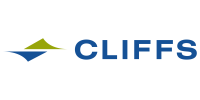
Cliffs unveils new hydrogen-powered stainless line in Ohio
CEO Lourenco Goncalves, flanked by state leaders and union reps, touted the project as proof that US manufacturing is not only alive, but also advancing.
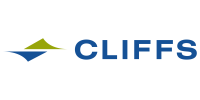
Cliffs idles Steelton, Riverdale, and Conshohocken operations
Cliffs has idled facilities in Riverdale, Ill., and Conshohocken and Steelton, Pa.
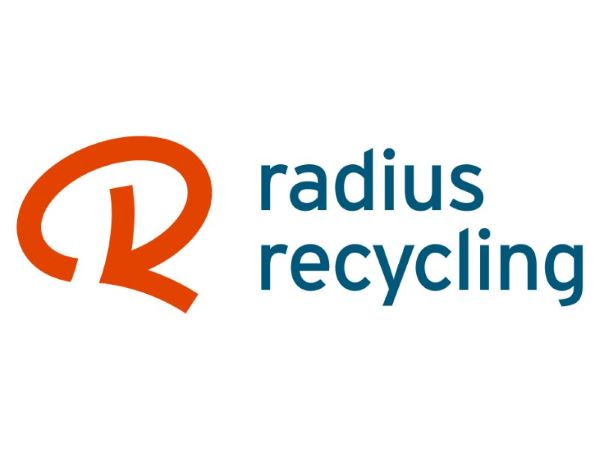
Radius loss narrows, volumes climb in ‘healthy’ West Coast market
Stronger steel demand in the Western US, rising scrap flows, and improved rolling mill utilization drove sequential gains for Portland, Ore.-based Radius Recycling.