Steel Mills
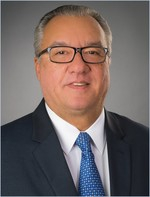
EXCLUSIVE: Cliffs CEO Makes New Deal With Auto Cos, Sees Green in EVs
Written by Michael Cowden
June 2, 2022
Cleveland-Cliffs Inc. has changed how it supplies the automotive industry in response to chip and parts shortages that have thrown a wrench into automaker production forecasts, the company’s top executive said.
“We no longer adopt their forecast as the final truth, like it was historically,” Cliffs chairman, president and CEO Lourenco Goncalves said.
How did things work in the past? “They would tell you, ‘I’m going to produce X amount of cars.’ And either ArcelorMittal (USA) or AK Steel would go ahead and produce exactly what they were telling them to produce,” he said.
That shift is notable because the Cleveland-based steelmaker supplied approximately 6.8 million tons of steel to the automotive industry last year. And that figure is even higher if one includes the roughly one million tons of slabs shipped by Cliffs to AM/NS Calvert that were rolled into coil and sold by the joint venture into the automotive sector, Goncalves noted.
The result: If the US automotive industry were to produce roughly 14 million vehicles in 2022, each containing approximately one ton of steel, Cliffs would be supplying about half of the steel that goes into vehicles in the United States.
“Automotive is our bread and better. Automotive is almost half of what we produce in steel,” he said.
Goncalves made the comments in an exclusive interview with Steel Market Update on the sidelines of an annual meeting of the American Iron and Steel Institute (AISI) and the Steel Manufacturers Association (SMA) last week in Washington, D.C.
Changing the Rules of the Forecasting Game
Cliffs transformed itself from an iron ore miner and pellet producer to one of the biggest steelmakers in the US – and the largest steel supplier to automotive – with the 2020 acquisitions of the former ArcelorMittal USA and AK Steel.
And the company now uses its own forecasting models – in combination with close communication with automakers – to determine how much steel to supply the industry. The result: Cliffs doesn’t have to worry about being “trapped” with too much inventory, and automakers continue to receive steel on a just-in-time (JIT) basis.
Why was a new model necessary? “If they don’t produce the cars, if they don’t put it in the assembly line, we’re not going to recognize the revenue. That’s why we had to create our own ways of doing business,” Goncalves said, in reference to auto assembly plant idlings caused by shortages of chips and other parts.
How does the new model work? “We send it to a place … it could be a waiting station, could be a processor, it could be whatever. But once you produce, you want to recognize the revenues,” he said.
Goncalves declined to provide additional specifics of the new arrangement but said it was working for both parties. “They (automakers) understand, all of them understand, and they are happy with that because we continue to grow business with them,” he said.
And he said Cliffs has a better relationship with automakers, despite jawboning with some of them on earnings calls, than had been the case previously. “I have a relationship at the CEO level, and that’s a game changer,” he said.
That’s not to dismiss the important day-to-day work of sales and engineering staff who work together to specify products. But engineers often focus on specific, localized goals, such as weight reduction, and less on the strategic goals, such as electrification, being discussed at higher levels.
“The relationship became so transparent and so adult that now we are doing more together,” Goncalves said.
EVs Mean More Steel Demand, Less C02
One area where that high-level relationship is bearing fruit is in electric vehicles. President Biden in August announced a goal of increasing electric vehicle share of US auto sales to 50% by 2030. Automakers are taking that goal seriously, Goncalves said.
2030 is eight years from now, which is “tomorrow” as far as automakers are concerned given the long lead times involved in designing and producing new vehicles. That presents an opportunity for a company like Cliffs, which Goncalves said is among the very few domestic steelmakers that can provide every flat-rolled steel grade and specification automakers might need.
EVs also present an opportunity to steel – and potential a challenge to aluminum – because among the biggest immediate concerns for automakers is how to protect the battery and other electrical components in case of a crash. The most obvious solution is putting more steel around critical EV components. And additional weight on an EV is not the problem it would be on a vehicle with a combustion engine, which presents a hurdle to lighter-weight aluminum.
“Let’s face it, with combustion engine vehicles, you are very concerned about weight because the more weight, the more consumption of fuel,” Goncalves said. “With the electric vehicle, a little bit less weight will probably consume a little less power. But it’s minimal … it doesn’t change much based on weight.”
The result: “Believe it or not, the EV will take 15-20% more steel. So my one car, one ton of steel, will go to one car, 1.2 tons of steel,” he said.
And it’s not just automakers pushing for electric vehicles, so is the broader debate around decarbonization. The steel industry is making strides to decarbonize but accounts for only about 1% of carbon emissions in the US compared to roughly 8% globally.
Tailpipe emissions from internal combustion engines, in contrast, account for about 29% of carbon emissions in the US with the next biggest source being power generation. All of which is to say that the US must convert more internal combustion engine vehicles to EVs if it is to reach its climate goals.
“If they (automakers) get to their goal of 50% by 2030 – and we believe there is a chance that they accomplish that – that will cut the 29% to 14-15%,” Goncalves said.
That’s not to say that the domestic steel industry won’t continue to decarbonize. Cliffs, for example, continues to use more hot-briquetted iron (Goncalves declined to say how much) in its blast furnaces to reduce coking rates. That’s possible because HBI – which Cliffs makes in Toledo, Ohio – is already reduced, and so less coking coal is needed as a reductant.
“My coke rate today at 325 kilograms (717 pounds) per ton is completely impossible to replicate throughout the entire world because it’s more like 650-700 kilos (abroad),” he said, noting that integrated steelmakers outside the US rely far more on coke and pulverized coal injection (PCI) in their blast furnaces.
By Michael Cowden, Michael@SteelMarketUpdate.com

Michael Cowden
Read more from Michael CowdenLatest in Steel Mills
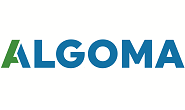
Algoma fires up EAF steelmaking with first arc
Algoma Steel reached a milestone in its transformation from blast furnace to electric arc furnace (EAF) steelmaking, with its Unit One EAF achieving its first steel production this week.
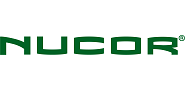
Nucor holds HR list price at $910/ton
Nucor is keeping its list price for spot hot-rolled coil unchanged after last week’s shortened holiday week.
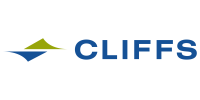
Cliffs unveils new hydrogen-powered stainless line in Ohio
CEO Lourenco Goncalves, flanked by state leaders and union reps, touted the project as proof that US manufacturing is not only alive, but also advancing.
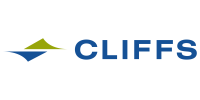
Cliffs idles Steelton, Riverdale, and Conshohocken operations
Cliffs has idled facilities in Riverdale, Ill., and Conshohocken and Steelton, Pa.
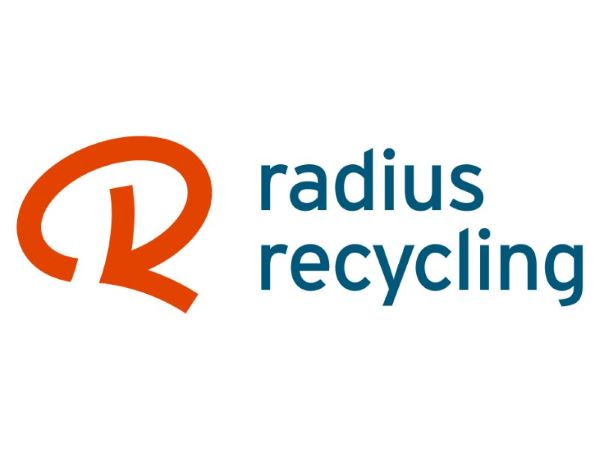
Radius loss narrows, volumes climb in ‘healthy’ West Coast market
Stronger steel demand in the Western US, rising scrap flows, and improved rolling mill utilization drove sequential gains for Portland, Ore.-based Radius Recycling.