Environment and Energy
IEEFA: Net-Zero Steel Will Require More High-Grade Iron Ore
Written by David Schollaert
June 28, 2022
The steel industry’s push to decrease CO2 emissions in steelmaking will require an increase in high-grade iron ore production and improved beneficiation techniques, according to a report from The Institute for Energy Economics and Financial Analysis (IEEFA).
To reach net-zero emissions by 2050, not only will steelmakers need to switch production methods from coal-consuming blast furnaces (BF) to green hydrogen-based direct reduced iron (DRI) processes, but a higher grade of iron ore is a must, the study found.
“Iron ore miners continue to be largely focused on producing lower quality blast furnace-grade iron ore as this coal-consuming technology still produces the great majority of the world’s steel,” said Simon Nicholas, the report’s author.
And though deposits of high-grade iron ore are scarce, there are mining options available to alleviate the DR-grade iron ore supply issue.
“Increased focus on magnetite mining is one option,” said Soroush Basirat, the report’s co-author. “Magnetite iron ore is often more suitable and preferable for further processing and producing iron ore concentrate and pellets of DR-grade quality.”
“There may also be the possibility of beneficiation of some existing iron ore production towards DR-grade,” he added.
Bloomberg New Energy Finance (BNEF) anticipates that a push for a net-zero steel sector by 2050 would require 59% of primary steel production to be driven by DRI-EAF-made steel.
“This would mean 889 million tons of steel production from DRI-electric arc furnace (EAF) by 2050, requiring a tenfold rise in DR-grade iron ore supply unless technology innovations allow DRI processes to use lower-grade ore,” said Basirat.
He noted that potential solutions to the DR-grade iron ore supply issue are in the works, “fortunately, such technology innovations are being developed.”
German steelmaker ThyssenKrupp plans to replace its BFs with DRI plants that include an integrated melting unit (submerged arc furnace) starting in 2025. The resultant liquid iron will then be converted to steel in the company’s existing metallurgical plant.
“This technology configuration will allow ThyssenKrupp to use blast furnace-grade iron ore in their DRI processes,” says Nicholas.
The challenge, according to Nicholas, is that “the focus on potential solutions must increase immediately” given the long mining lead times and extensive technology shift it will require.
That shift is already underway in some cases. ArcelorMittal and BlueScope Steel are examining similar DRI-melting unit combinations, while US Steel announced today that its Granite City Works will switch its BFs to pig iron production in the second half of 2024.
The Lakewood, Ohio-based Institute for Energy Economics and Financial Analysis (IEEFA) explores issues related to energy markets, trends, and policies. Its focus is to accelerate the transition to a diverse, sustainable, and profitable energy economy.
By David Schollaert, David@SteelMarketUpdate.com
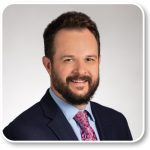
David Schollaert
Read more from David SchollaertLatest in Environment and Energy
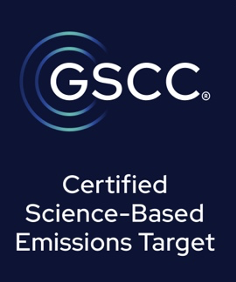
Global Steel Climate Council certifies eight SDI, ASA HR products
GSCC certifies eight products from Steel Dynamics and Arkansas Steel Associates.
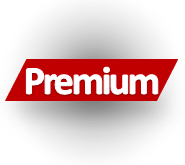
June energy market update
In this Premium analysis we examine North American oil and natural gas prices, drill rig activity, and crude oil stock levels. Trends in energy prices and rig counts serve as leading indicators for oil country tubular goods (OCTG) and line pipe demand.
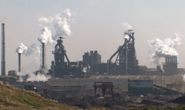
EPA deregulation proposals win praise from steel advocates
Two industry groups are applauding two EPA proposals that would support domestic steel production.
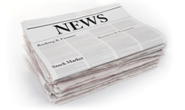
Met coal receives critical materials status
The US Department of Energy (DOE) adds metallurgical coal to the nation’s list of Critical Materials, following its designation by US Secretary of Energy, Chris Wright’s announcement on May 22.
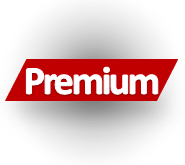
May energy market update
An analysis of the North American energy market in May.