Steel Mills
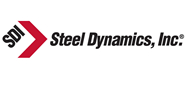
It's Official, SDI To Build Aluminum Rolling Mill in Columbus, Miss.
Written by Michael Cowden
November 3, 2022
It’s official. Steel Dynamics Inc. (SDI) will build its $1.9 billion flat-rolled aluminum mill in Columbus, Miss., where the company already operates an electric-arc furnace (EAF) steel sheet mill.
The Fort Wayne, Ind.-based steelmaker said it would also construct a “biocarbon” facility in Columbus to reduce reliance on anthracite coal in its EAFs and to further cut its already low carbon-emissions profile.
Those CO2 cuts would come in addition to those inherent in using recycled aluminum scrap. SDI noted that it is the largest nonferrous metals recycler in North America.
“A significant number of our flat-rolled carbon steel customers are also consumers and processors of aluminum flat-rolled products,” SDI chairman, president and CEO Mark Millett said in a press release on Wednesday, Nov. 2.
“This investment broadens our ability to serve our existing and new customers by adding high-quality, low-carbon footprint flat-rolled aluminum to our product portfolio,” he added.
The facility is expected to create 700 jobs and as many as 250 more indirect jobs, SDI said.
Recall that the ~$2.2 billion figure for the entire aluminum project includes $350 million for two “satellite” slab-casting plants, one in the southwestern US and another in north-central Mexico.
The Aluminum Mill
Steel Market Update reported prior to SDI’s official announcement that the aluminum mill would be in Columbus. We also noted that it was registered as “Aluminum Dynamics” in paperwork filed with the Mississippi Secretary of State.
The aluminum rolling mill is expected to have annual capacity of 650,000 metric tons of finished products. It is slated to begin operations in mid-2025 and to serve the beverage can, automotive, and common alloy markets, SDI said.
The mill will also sport value-added finishing lines, including continuous annealing solutions heat treating (CASH) lines, continuous coating, and slitting and packaging operations.
The Columbus site sports enough acreage for customers to co-locate with aluminum mill. That will provide the mill with a baseload of business while also saving customers money on logistics and working capital, the company said.
That strategy echoes one SDI deployed at its new EAF sheet mill in Sinton, Texas, where customers are located on the site of the mill – something that reduces freight costs and associated scope 3 carbon emissions.
Scope 1 refers to emissions generated directly by a producer’s operations. Scope 2 refers to emissions related to the energy that powers that company. And Scope 3 includes other emissions associated with a mill’s manufacturing process — including transportation and logistics.
Columbus in addition has access to both natural gas and “ample” renewable power, SDI said.
As for logistics, the mill will have on site-access to a class I railroad, proximity to major highways, and access to the Tennessee-Tombigbee Waterway.
The “Tenn-Tom” connects the Tennessee River in northeast Mississippi with the Tombigbee River in Armory, Miss. The 234-mile system allows for navigation from the interior US to the Gulf of Mexico, according to the Army Corps of Engineers.
Biocarbon Production
SDI also selected Columbus for an “initial” SDI Biocarbon Solutions operation, one that will be a joint venture with Aymium, an Oakdale, Minn.-based company that makes coal alternatives from biomass — think wood, crops, or agricultural waste.
“We believe this strategic joint venture with Aymium will significantly reduce our steelmaking greenhouse gas emissions, which are already materially lower than our global competitors, in a cost-effective manner,” Millett said.
The Columbus biocarbon plant is expected to begin operations in early 2024 and to have capacity of 160,000 metric tons per year. SDI said it has already trialed Aymium’s biocarbon successfully in its steel mills.
The company estimates that the Columbus biocarbon plant will cut scope 1 greenhouse gas emission intensity at its steel mills by 20–25%.
Both projects hinge on receipt of necessary permits as well as continued state and local government support, SDI noted.
By Michael Cowden, Michael@SteelMarketUpdate.com

Michael Cowden
Read more from Michael CowdenLatest in Steel Mills
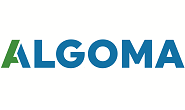
Algoma fires up EAF steelmaking with first arc
Algoma Steel reached a milestone in its transformation from blast furnace to electric arc furnace (EAF) steelmaking, with its Unit One EAF achieving its first steel production this week.
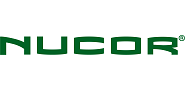
Nucor holds HR list price at $910/ton
Nucor is keeping its list price for spot hot-rolled coil unchanged after last week’s shortened holiday week.
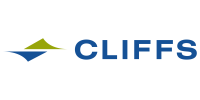
Cliffs unveils new hydrogen-powered stainless line in Ohio
CEO Lourenco Goncalves, flanked by state leaders and union reps, touted the project as proof that US manufacturing is not only alive, but also advancing.
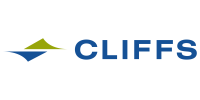
Cliffs idles Steelton, Riverdale, and Conshohocken operations
Cliffs has idled facilities in Riverdale, Ill., and Conshohocken and Steelton, Pa.
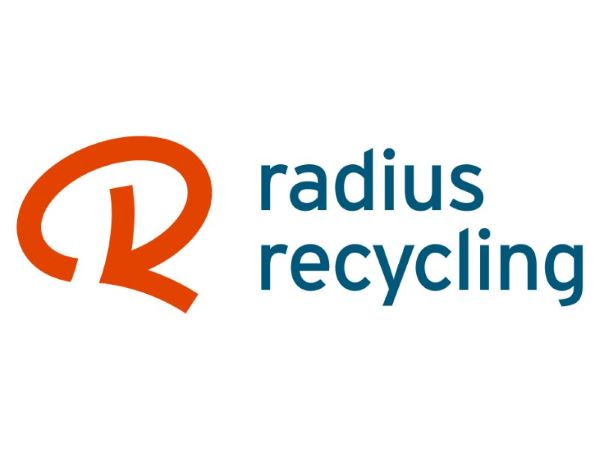
Radius loss narrows, volumes climb in ‘healthy’ West Coast market
Stronger steel demand in the Western US, rising scrap flows, and improved rolling mill utilization drove sequential gains for Portland, Ore.-based Radius Recycling.