Steel Mills
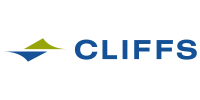
Cliffs Introduces Surcharge on Steel Made From HBI
Written by Laura Miller
July 25, 2023
Cleveland-Cliffs is now charging its automotive customers a premium for its lower-carbon steel.
The steelmaker has recently introduced a surcharge of $40 per net ton ($44 per metric ton or $2 per cwt) to each ton of steel made with Cliffs’ hot-briquetted iron (HBI). They are calling it the “Cliffs H” surcharge, chairman, president and CEO Lourenco Goncalves said on the company’s second-quarter earnings call on Tuesday, July 25.
“Our customers are starting to recognize the important role that HBI has played in our carbon-reduction goals,” he said, also noting later that “they are paying because if they don’t pay, they don’t get the steel.”
“We deserve to be paid for a characteristic of our steel that truly differentiates us, particularly when compared to other major suppliers of steel to the automotive industry in the US, in Europe, in Japan, in South Korea, in China, or anywhere else throughout the entire world,” he explained.
Goncalves said they’ve been producing HBI at a cost of less than $200 per metric ton.
“Our HBI has not only been a carbon-intense reduction agent, but also a productivity and margin enhancing agent,” he noted.
Goncalves said he believes the Cliffs H surcharge should be passed on by the car manufacturers to the final consumers. “That would only increase the window sticker, the MSRP on the car by 0.1%,” he said.
“Cleveland-Cliffs wants to continue to invest in our green initiatives. Therefore, we need to be paid for that. That’s not unreasonable and should actually be expected and universally accepted,” he stated.
Goncalves reflected on the success the company has had in building, renting out, and operating its 2-million-ton-per-year direct-reduction plant in Toledo, Ohio, which began HBI production late in 2020. He said neither of the other two reduction plants previously built in the US are good examples of success.
With those plants’ “failure to execute… it goes underappreciated that since we’ve built and commissioned our HBI plant, we have been operating uneventfully and at capacity for two and a half years,” he said.
The next step in the company’s evolution will be the use of hydrogen throughout its footprint, including at its Toledo facility and in its blast furnaces, he said.
In May, Cliffs became the first company in the Western hemisphere to successfully complete a full-scale trial injecting hydrogen into a BF. Using it as a substitute for fossil fuel reductant, it replaces CO2 emissions with H20 water vapor “with no impact to product quality or operating efficiency.”
Goncalves said they will next be trialing the technologies at its largest blast furnace, No. 7, in Indiana Harbor, Ind.
“We believe hydrogen will be the true game changer for the decarbonization of steel. It’s simple chemistry after all,” Goncalves said, noting they’ve already proven its effectiveness. Now the main hurdle remaining is economics, as equivalent units of hydrogen gas are about 10 times more expensive than natural gas.
And that’s why Cliffs has become an active player in the building of hydrogen hubs in the Midwest, Goncalves said.
Cliffs is a part of the Great Lakes Clean Hydrogen Coalition, which has proposed to develop low-carbon hydrogen via electrolysis in Ohio to be distributed throughout the region. The Coalition has applied for funding from the US Department of Energy’s regional clean hydrogen hub initiative, asking for 50% of the $2 billion plus needed for the project.
“As hydrogen becomes more and more economical, we’ll be able to implement it throughout our entire footprint,” he noted.
By Laura Miller, laura@steelmarketupdate.com
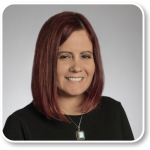
Laura Miller
Read more from Laura MillerLatest in Steel Mills

Nippon plans to double steel output at USS operations: Report
Now that it has acquired U.S. Steel, Nippon Steel is planning a significant expansion of its US operations, including the construction of a new mill and more than doubling its steel output.
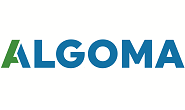
Algoma fires up EAF steelmaking with first arc
Algoma Steel reached a milestone in its transformation from blast furnace to electric arc furnace (EAF) steelmaking, with its Unit One EAF achieving its first steel production this week.
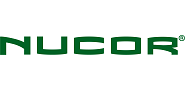
Nucor holds HR list price at $910/ton
Nucor is keeping its list price for spot hot-rolled coil unchanged after last week’s shortened holiday week.
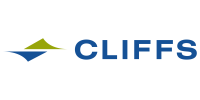
Cliffs unveils new hydrogen-powered stainless line in Ohio
CEO Lourenco Goncalves, flanked by state leaders and union reps, touted the project as proof that US manufacturing is not only alive, but also advancing.
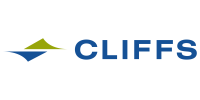
Cliffs idles Steelton, Riverdale, and Conshohocken operations
Cliffs has idled facilities in Riverdale, Ill., and Conshohocken and Steelton, Pa.