Aluminum
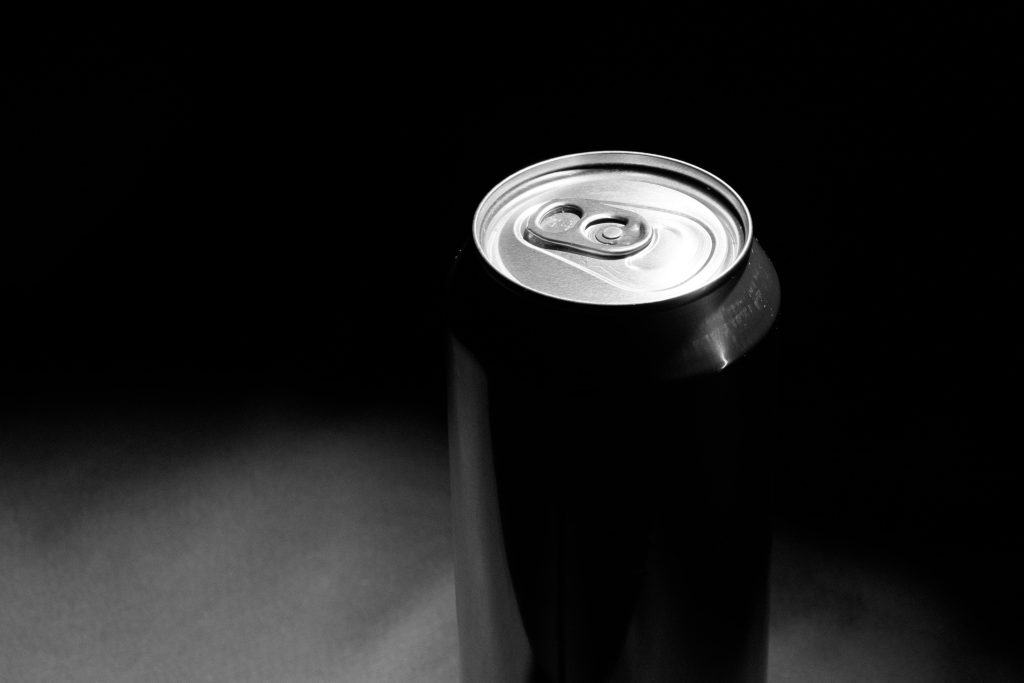
Tariffs are easy to announce, but hard to track
Written by Gabriella Vagnini
April 3, 2025
Announcing tariffs is easy. Implementing them at the border? That’s a whole different ball game.
Customs runs all of this through their Automated Commercial Environment, better known as ACE. It’s their system for processing imports, flagging issues, applying duties, and pushing out updates. It sounds clean on paper, but when new tariffs get added, especially when they’re messy and product-specific like aluminum derivatives, it takes more than just flipping a switch.
Case in point: On March 12, ACE mistakenly applied Section 232 duties to certain imports due to misclassification. Specifically, items under HTSUS codes 8418.99.8010, .8015, .8020, and .8025 that were flagged incorrectly. Customs had to scramble to fix it and told importers they’d need to file a Post Summary Correction (PSC) in order to get their money back. That means time, paperwork, and delays.
So how is Customs trying to stay on top of all this?
To ensure compliance, CBP employs several strategies. Here are three of the top key tools:
Cargo Systems Messaging Service (CSMS): This is where CBP posts real-time alerts about tariff changes, filing instructions, and technical issues. On March 7, for example, CSMS #64348288 provided detailed guidance on how to file aluminum tariffs that were going live five days later.
ACE system updates: Customs constantly tweaks the ACE system to handle new product codes, duty rates, and Country of Origin (COO) rules.
Reporting requirements: Importers have to provide more detailed information now, especially for aluminum. That info lets Customs trace where the metal came from, who processed it, and whether it qualifies under any trade deals or country-specific rates (primary smelt country, secondary smelt country, country of cast).
What should importers be doing right now?
Stay plugged into CSMS. That’s where the critical updates drop first.
Make sure your codes are right. One wrong HTS number and you’re paying the wrong tariff or overpaying altogether. View HTS codes for aluminum here.
Keep tight records. If something goes sideways, you’ll need backup to file a PSC and try to get that money back.
Real example: Triple-tariff trap
Say a US company brings in aluminum sheet from India and pays the import tariff. Then they send some of that material to Mexico to turn it into automotive heat shields. That gets exported back into the US as a finished product.
If that part doesn’t meet USMCA-origin rules, meaning it didn’t go through a big enough transformation in Mexico, it can get hit with another tariff on the way back into the US. So, even though duties were already paid at the start, and again going into Mexico, now there’s a third duty waiting at the border. That’s because Customs still sees that metal as Indian. Unless you have the paperwork to prove otherwise, it’s not going to qualify.
In this case, you need a document issued by the Mexican exporter or producer. It should state that the product meets USMCA rules of origin, meaning enough manufacturing happened in Mexico to qualify it as a North American product. Without this certificate, the product is presumed to be, in this example, still of Indian origin), and tariffs will apply.
US Customs can, and often does, ask for additional supporting documents, including bills of material, production and assembly records, purchase invoices for raw materials, cost breakdowns, and product-specific process documents.
If you can’t prove that substantial transformation happened in Mexico, the CBP can deny the USMCA claim and apply full duties.
The bottom line
This is a lot to ask from Customs. We’re not talking about basic ingots or T-bars anymore. These are aluminum derivatives, like cans, auto parts and all kinds of processed materials, and that means Customs has to dig deeper. More paperwork, more judgement calls, more things that can get missed.
It’s not that the system can’t handle it, it’s just that the more complicated this gets, the more likely codes get crossed, shipments get flagged, and the process turns into a full-on logistics nightmare.
Editor’s note: This column appeared first in Aluminum Market Update (AMU), SMU’s new sister publication.
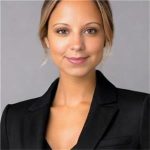
Gabriella Vagnini
Read more from Gabriella VagniniLatest in Aluminum
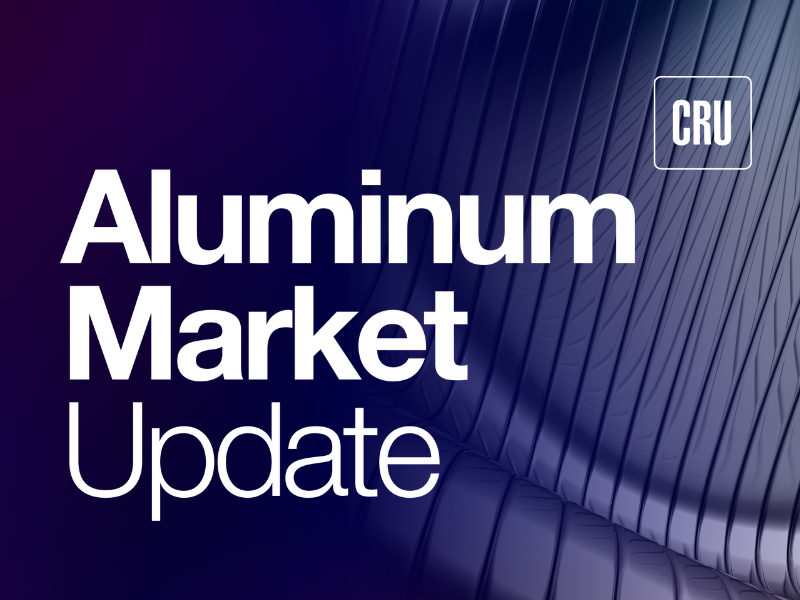
AMU: Does the US-EU trade deal shift attention to Mexico or Canada?
On Thursday, the U.S. and EU agreed to more concrete terms to their handshake deal of last month.
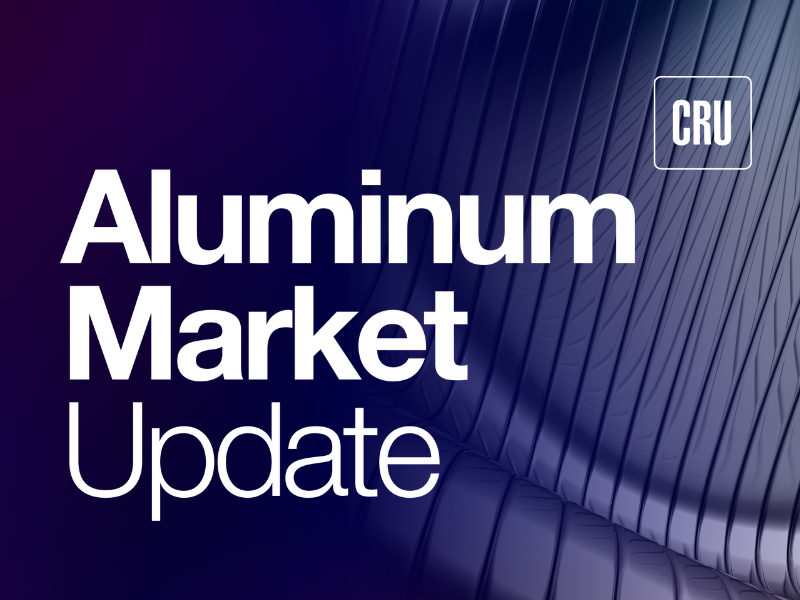
AMU: Grid upgrades starting to cope with rising electricity demand
Hardly a day goes by without someone writing about the expected rise in US electricity demand. This demand is largely driven by data center and AI’s appetite for power.
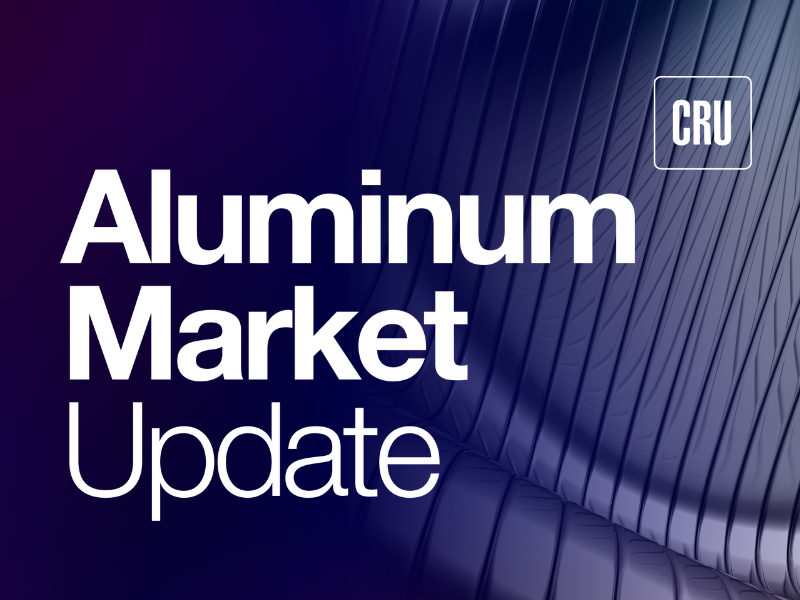
AMU: Non-residential construction sends mixed signals
While US construction markets are far from uniform, recent indicators from June and July paint an unusually fragmented picture.
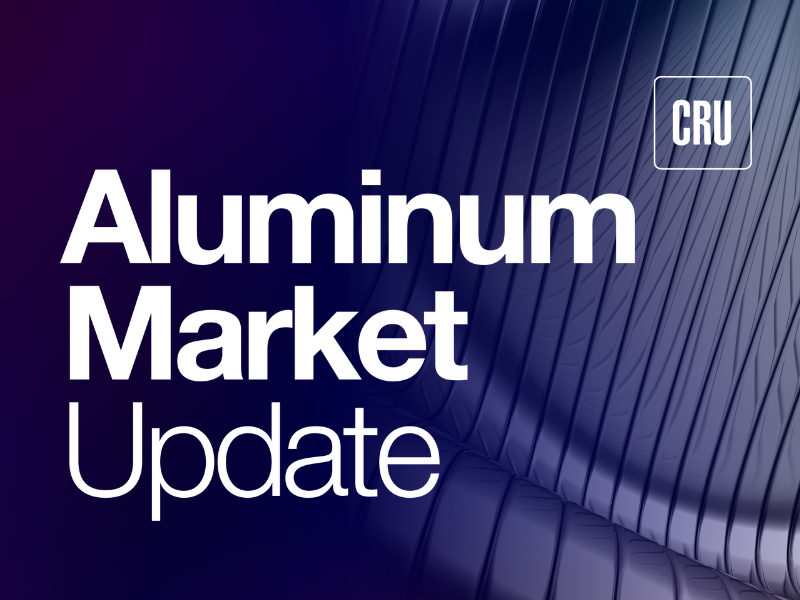
AMU: Q2 tariff headwinds blow Alcoa inland
Tariff threats on Brazil aren't just hitting steel products. Aluminum is also feeling the heat.
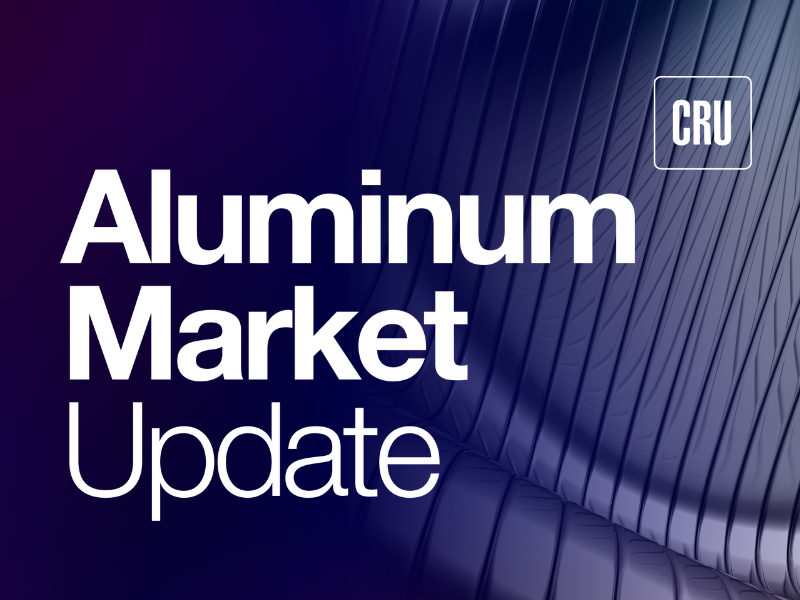
AMU: Commercial vehicle trends in aluminum
The commercial vehicle sector is showing signs of fatigue, but you wouldn’t know it at first glance of the latest government figures.