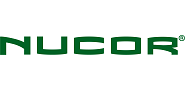
Nucor maintains plate prices, opens August order book
Nucor aims to keep plate prices flat again with the opening of its August order book.
Nucor aims to keep plate prices flat again with the opening of its August order book.
Nucor maintained its weekly list price for hot-rolled (HR) coil this week, following two consecutive increases.
Cleveland-Cliffs plans to increase prices for hot-rolled (HR) coil to $950 per short ton (st) with the opening of its July spot order book. The Cleveland-based steelmaker said the price hike was effective immediately in a letter to customers dated Monday.
The price spread between HRC and prime scrap widened in June.
Steel prices climbed for a second straight week across all five sheet and plate products tracked by SMU.
The $20/short ton increase applies to all of the steelmaker’s sheet mills, including West Coast joint-venture subsidiary CSI.
Nucor halted a four-week decline in its spot price for hot-rolled coil this week, maintaining its weekly consumer spot price (CSP) at $870/st.
Nucor has lowered its consumer spot price (CSP) for hot-rolled coil by $10 per short ton (st), marking the fourth consecutive weekly decrease.
After eight weeks of double-digit price increases on hot-rolled (HR) coil, Nucor slowed the price rise this week with an increase of $5 per short ton.
The price spread between stateside-produced CR and imports reached its widest margin in over a year.
Evraz North America (NA) has followed Nucor and SSAB with a plate price increase of its own: up $160 per short ton (st). The increase was effective immediately for all new orders of carbon, high-strength low-alloy, and normalized and quenched-and-tempered plate products, as well as for hot-rolled coil, the steelmaker said in a letter to […]
Nucor has increased its consumer spot price (CSP) for hot-rolled (HR) coil for a fourth consecutive week.
Nucor increased its consumer spot price (CSP) for hot-rolled (HR) coil to $790 per short ton (st) on Monday, Feb. 10 – a $15/st bump vs. last week. The Charlotte, N.C.-based company has raised its weekly CSP by $40/st over the past three weeks after maintaining tags at $750/st since Nov. 12, according to SMU’s […]
ArcelorMittal Dofasco is raising spot sheet prices by CA$100 per ton (US$70/ton). The Hamilton, Ontario-based flat rolled steelmaker told customers the increase is effective immediately for all new orders. It did not specify to what level this brings its base prices but noted its right to re-quote previous but unconfirmed orders. “We will continue to […]
Nucor increased its consumer spot price (CSP) for hot-rolled (HR) coil to $775 per short ton (st) on Monday, Feb. 3. The $15/st week-on-week (w/w) rise marks the first back-to-back increases in the steelmaker’s weekly CSP since last August, according to SMU’s mill price announcement calendar. Nucor’s joint-venture subsidiary California Steel Industries (CSI) is also up […]
Nucor increased its consumer spot price (CSP) for hot-rolled (HR) coil to $760 per short ton (st) on Monday, Jan. 21. The $10/st week-on-week (w/w) rise marks the first increase in the CSP since Nov. 12. According to SMU’s mill price announcement calendar, the Charlotte, N.C.-based steelmaker held the weekly price at $750/st for 11 […]
Steel prices ticked lower this week for four of the five products SMU tracks, according to our latest canvass of the sheet and plate markets. Following last week’s bump, our hot rolled, cold rolled, galvanized, and plate indices all edged lower this week by $5-15 per short ton (st) on average. Galvalume was the only […]
The steelmaker has kept its weekly consumer spot price for hot-rolled steel sheet unchanged since Nov. 12.
Nucor’s weekly spot price for hot-rolled (HR) coil will remain at $750 per short ton (st) for a fifth week.
Steel sheet prices remain at or near multi-month lows, while plate prices continue edging lower from their mid-2022 peak.
For the fourth week in a row, Nucor will keep its published spot price for hot-rolled (HR) coil unchanged.
Wolfe Research's Managing Director Timna Tanners discusses the 'Trumplications' for steel in the coming year in this week's SMU Community Chat.
Nucor raised its weekly consumer spot price (CSP) for HRC this week to $750/short ton.
Steel sheet prices mostly edged lower for a second week, while plate prices slipped for the third consecutive week.
After holding its weekly spot price for hot-rolled (HR) coil steady for three weeks at $730 per short ton (st), Nucor lowered the price this week by $10/st.
Steel sheet and plate prices moved lower this week as efforts among some mills to hold the line on tags ran up against continued concerns about demand.
CRU Senior Steel Analyst Alexandra Anderson shares insight into the current market for long steel products.
Nucor is holding its hot-rolled (HR) coil consumer spot price (CSP) at $730 per short ton (st) this week.
Galvanized steel buyers on Tuesday discussed the eerie stability in sheet prices of late. Expectations are for the murky market to persist in the short term, while glimmers of hope continue for prices pushing higher.
Nucor’s weekly consumer spot price (CSP) for hot-rolled (HR) coil increased $10 per short ton (st) from last week to $730/st as of Monday, Sept. 23.