International Steel Mills
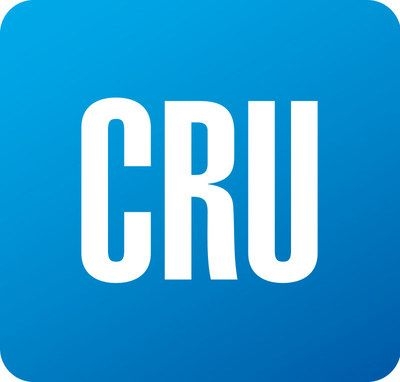
CRU Explains: Why Early Blast Furnace Restarts Lead to Oversupply
Written by Alexander Ordosch
June 2, 2020
By CRU Analysts Alexander Ordosch and Iris Speelmanns, from CRU’s Steel Sheet Products Monitor:
The Covid-19 crisis has resulted in a rapid fall in market activity and steel demand, which has resulted in steelmakers across the globe responding quickly by lowering steel production. Steelmakers have two options to reduce steel output in response to lower demand: lower hot metal consumption and output and/or reduce scrap rates. Because many blast furnaces were already operating at low utilization and scrap rates, many steelmakers needed to idle blast furnace capacity. This has meant the volume of hot metal and steel output has not been reduced as significantly as the capacity idled. Currently, 28 blast furnaces (BFs)—totaling ~43 Mt of annualized nominal capacity—have been idled in the USA and Europe. During the recovery phase of the Covid-19 pandemic because the restart of BF capacity is lumpier than the upturn in demand, there is the potential for periods of excess supply.
Sizeable Steel Output Reductions Require BF Closures
The key inputs into a BOF-based steelmaking process are hot metal (i.e. iron) and steel scrap. In more typical conditions, to adjust to weaker demand, steelmakers can adjust steel output by reducing the utilization of their operating BFs and/or by changing the scrap rate in the BOF. Steelmakers will balance relative costs of hot metal production and scrap in their operations in doing so, though sustaining output at the BF will be a priority and in the first instance they will lower scrap rates. During a demand shock, the low operational flexibility of a BF creates an initial period of oversupply.
BF Utilization and Scrap Consumption Can Only Be Reduced So Far
When there is a need to lower output from the BF, there is a minimum utilization level the furnace must operate at before there are operational problems and it is damaging to the furnace itself. At this point, steelmakers with two or more operational BFs have the option to idle furnaces to further reduce hot metal output. Scrap rates are also technically bounded, with a minimum required to provide a cooling effect in the furnace, while too much scrap cools the hot metal too quickly. The constraints on steelmaking supply chains are discussed further in the Insight CRU explains: flexibility in the steelmaking chain.
Already weak demand had plant operations near these constraints, one of the main reasons for the extensive BF outages taking place so quickly. For example, in Europe scrap rates and utilization of BFs were already low pre-Covid-19 and this meant many operations quickly approached the technical minimum operating rate for their BFs. Consequently, BF operators could not simply lower hot metal output in response to the Covid-19 demand shock and had to close capacity.
The graphic below quantifies the supply cuts of an integrated mill operating with 2 BFs; with BOF scrap rates minimized, we estimate that a reduction in steel output of ~1 Mt can be achieved for every 1 Mt of idled BF capacity.
Inability to Idle All BFs of an Integrated Mill Further Limits Supply Response to Weak Demand
Even during a time of very weak steel demand, integrated mills try to keep at least one BF running to maintain their gas economy and to keep coke ovens operational. This further limits their ability to adjust supply to demand. If weak steel demand requires idling of BFs and minimizing hot metal output on the remaining one, iron content in the charge can be curtailed. This includes using higher rates of lower-grade fines in the production of sinter, reducing pellet rates, and cutting any cold metallics that were being charge. While a shift to low-grade iron ores could improve demand for these materials, supply of has been particularly strong this year. This has sustained a wider discount on these ores.
BF Restarts Create a Lump in Supply
Because a BF must operate at a minimum utilization, there is the risk of a temporary demand-supply mismatch, particularly during a downturn and at the onset of a recovery. This issue is compounded by the fact that BFs have become more productive over time, thus increasing the impact of a shutdown and restart on the market balance. These imbalances occur because changes in BF supply are generally lumpier than shifts in demand. Multi-site steel companies may be able to minimize this imbalance by consolidating steel supply to fewer plants and serving multiple markets as they recover. Even so, a large supply risk remains as many single-site operations have idled furnaces.
BF Restarts are Lumpy, While Demand Will Recover More Gradually
As steel markets recover from the pandemic-induced downturn, idled BFs will be restarted and there is a significant risk of periods of oversupply. Initially, steel producers can increase the productivity of the operating BFs and the BOF, but eventually they will need to restart idled BFs to service increased demand. As blast furnaces cannot restart gradually, this supply will likely exceed available demand, which CRU expects to stay weak in 2020 and recover more gradually. Many market participants are expecting the first BF restarts to begin in late-2020 Q3 and 2020 Q4, creating a risk of temporary oversupply and low prices in this period.
For example, take the case of a steel mill with two 2 Mt/y BFs, one of which is idled. The restart of the idled BF adds ~800 kt/y of crude steel production compared to the maximum steel production using one of the BFs (i.e. maximizing BF output and scrap rates in the BOF). Therefore, a strong order book is needed to justify restarting an idled BF.
Multiple Operating Sites Offer Some Steelmakers More Flexibility, But Is It Enough?
Steelmakers that operate BFs across multiple sites have more flexibility. These companies can restart a BF at one plant and ship excess semis or finished steel to multiple markets as demand there recovers, thereby consolidating ironmaking to fewer plants. This minimizes the potential for oversupply by utilizing fewer BFs to a greater degree for a wider pool of demand. As supply is aggregated it is better adjusted to demand and reduces the risk to steel prices. Even so, this is not an ideal solution for these steelmakers as costs are still being borne at the idled facilities and the steel is being shipped further and incurring greater logistics costs.
BF Restarts May Lead to Oversupply
It is challenging for BF-based steel operations to adjust production dynamically to demand because of the operational inflexibility of the BF. Once closures take place, the restart of BFs creates the risk of a period of potential oversupply as demand will not typically recover quickly enough to absorb all the material produced at the minimum technical utilization of the BF. Our view is that steelmakers are unlikely to wait until order books are filled sufficiently to sustainably restart idled BFs. If demand begins to exceed their available supply without a BF restart, this risks a loss of market share, either to other domestic producers or imports. In Europe, most idled BFs belong to multi-site steelmakers and so can be better managed, but we believe that restarted BFs from single-site producers will be enough to tip the scales of the European steel market. This will lead to oversupply, and excess volume will likely be sold as semi-finished or finished steel at low prices.
Request more information about this topic.
Learn more about CRU’s services at www.crugroup.com
Alexander Ordosch
Read more from Alexander OrdoschLatest in International Steel Mills
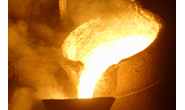
Global steel mill output steady through May
Global raw steel production rose 2% from April to May, slightly above average production levels seen in recent months, according to data recently released by the World Steel Association (worldsteel).
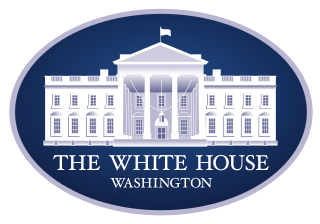
Trump says US government to control 51% share in USS
President Trump says the US government will hold a 51% stake in U.S. Steel after the Nippon deal.
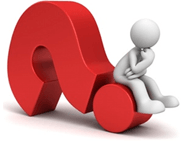
USS, Nippon Steel quiet as litigation deadline approaches
There has been little word from U.S. Steel, Nippon Steel, or the White House since President Trump endorsed the companies’ “partnership” on social media and celebrated it at the May 30 rally outside Pittsburgh.
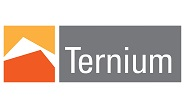
Ternium’s Vedoya named AIST’s Steelmaker of the Year
Maximo Vedoya was awarded in recognition of Ternium’s expansion project in Pesquería, Mexico, and Ternium’s efforts to decarbonize steelmaking.
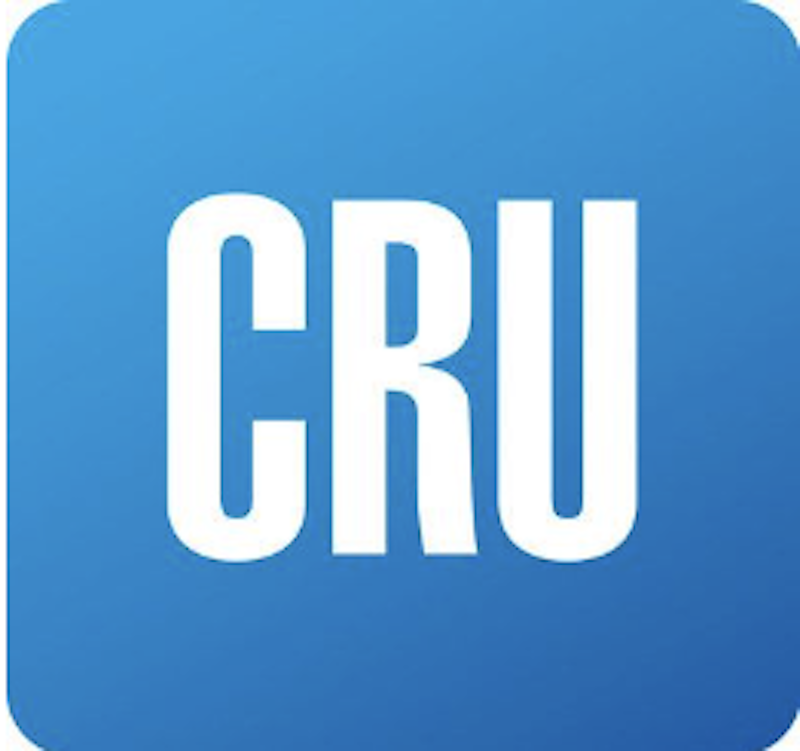
CRU: Baosteel hints at output cuts in China
Baosteel exec comments on market rumors of 50 million tons of output being cut this year, less than 0.5% of the 1 billion tons-plus China has produced annually in recent years.