Steel Mills
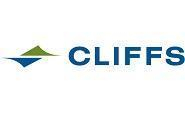
Cliffs Considers Converting BF to EAF Amid Mine Idling, Coke Plant Closure: CEO
Written by Michael Cowden
February 11, 2022
Cleveland-Cliffs Inc. could join other steel producers in adding electric-arc furnace (EAF) capacity, the company’s top executive said.
The Cleveland-based steelmaker is considering that because the cost of relining a blast furnace – and investing in the supply chains needed to feed it – are roughly the same as those for of building a new EAF.
Because the costs “come out close to a wash,” Cliffs “might consider an EAF as a replacement to a blast furnace in the future,” Cliffs Chairman, President and CEO Lourenco Goncalves said in an earnings conference call with analysts on Friday, Feb. 11
Goncalves did not have a specific timeline for when Cliffs might add EAF capacity. “Certainly not in 2022. I don’t believe it will be 2023 either,” he said.
Cliffs says it is the top supplier of automotive steels in North America, and those products need to come from blast furnace-based steelmaking. But other less-demanding applications could be served well via the EAF route, Goncalves said.
While Cliffs is primarily known as an integrated steelmaker, it also operates several EAFs. And sourcing scrap shouldn’t be an issue because of the company’s acquisition last year of Ferrous Processing and Trading Co. (FPT), a leading recycler of the prime scrap needed to make sheet products, he said.
Also on the operations side, Cliffs confirmed that it was taking an extended outage on one of two blast furnaces at its Cleveland Works. The work will be on the No. 5 blast furnaces, as SMU previously reported. The 100-day outage will run from March to June, a company spokeswoman told SMU on Friday.
That is longer than the 80-90 day outage market participants reported to Steel Market Update earlier this week. We have updated our blast furnace status table to reflect that development.
Turning to raw materials, Goncalves said that Cliffs would idle all production at its North Shore mining operations in Silver Bay, Minn., starting in the spring and through at least the fall – and potentially well beyond. He said the company was doing so mostly because of an onerous royalty structure.
The extended idling is also possible because Cliffs is melting more scrap and hot-briquetted iron (HBI) in its furnaces – which means it requires less iron ore, Goncalves said.
That ability to “stretch” hot metal in addition means that Cliffs needs less coke. And the company is therefore permanently closing its Mountain State Carbon coke plant in Follansbee, W.Va., in the second quarter. Doing so will reduce the company’s carbon footprint and save it approximately $400 million in capital expenditures that would have been necessary there in the future years. Workers there will be offered jobs at other Cliffs operations nearby, he said..
Metallurgical coal is heated into coke in coke ovens. Coke is a necessary raw material in steel production via the integrated route – in which iron ore and coke are combined in blast furnaces to produce liquid iron. But that process is also extremely carbon intensive, which is why other steelmakers – Canadian steelmaker Algoma, for example – are building EAFs to replace their integrated operations.
By Michael Cowden, Michael@SteelMarketUpdate.com

Michael Cowden
Read more from Michael CowdenLatest in Steel Mills
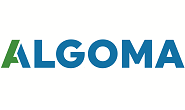
Algoma fires up EAF steelmaking with first arc
Algoma Steel reached a milestone in its transformation from blast furnace to electric arc furnace (EAF) steelmaking, with its Unit One EAF achieving its first steel production this week.
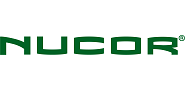
Nucor holds HR list price at $910/ton
Nucor is keeping its list price for spot hot-rolled coil unchanged after last week’s shortened holiday week.
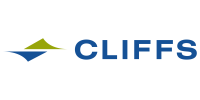
Cliffs unveils new hydrogen-powered stainless line in Ohio
CEO Lourenco Goncalves, flanked by state leaders and union reps, touted the project as proof that US manufacturing is not only alive, but also advancing.
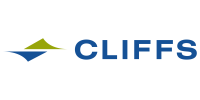
Cliffs idles Steelton, Riverdale, and Conshohocken operations
Cliffs has idled facilities in Riverdale, Ill., and Conshohocken and Steelton, Pa.
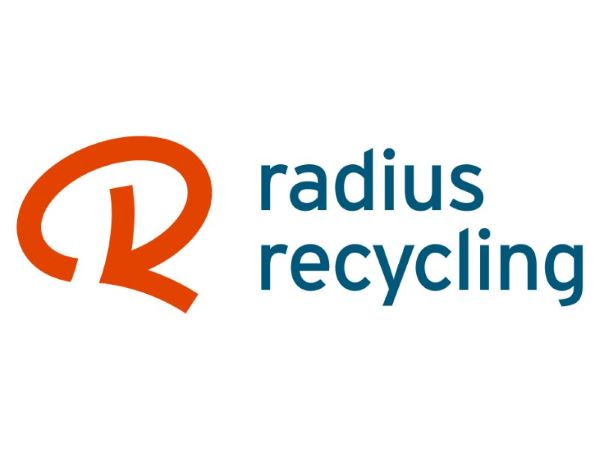
Radius loss narrows, volumes climb in ‘healthy’ West Coast market
Stronger steel demand in the Western US, rising scrap flows, and improved rolling mill utilization drove sequential gains for Portland, Ore.-based Radius Recycling.