Steel Mills
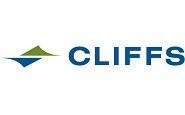
Cliffs to Idle Indiana Harbor No. 4 Blast Furnace, Raises Prices $50/ton
Written by Michael Cowden
February 21, 2022
Cleveland-Cliffs Inc. will indefinitely idle the No. 4 blast furnace at its Indiana Harbor steelmaking campus in northwest Indiana.
The Cleveland-based steelmaker also announced that it was raising prices for April orders of carbon hot-rolled, cold-rolled and coated flat-rolled steel by at least $50 per ton ($2.50 per cwt).
Cliffs will transfer hot metal production from the No. 4 blast furnace to the much larger No. 7 furnace, the company said in an announcement on Monday, Feb. 21.
The No. 4 furnace is expected to cease production within the next two months. The move will reduce the number of operational blast furnaces at Cleveland-Cliffs from eight to seven.
“By concentrating the operation and maximizing productivity at IH#7, we are improving our carbon footprint and, at the same time, lowering our cost structure for the same level of steel production and shipments,” Cliffs Chairman, President and CEO Lourenco Goncalves said in a statement.
Workers who had been assigned to the No. 4 furnace will be re-assigned to other positions at Indiana Harbor, where the number of job openings exceeds the number of people who work on No. 4, Cliffs said.
Normal operations will continue at Indiana Harbor’s two steel shops, hot strip mill and finishing facilities as well as at its Riverdale Works, Cliffs said.
The idling of No. 4 will mean that both Indiana Harbor in East Chicago, Ind., and Riverdale Works, just across the state line in Illinois, will be dependent on a single furnace. Riverdale receives hot metal via torpedo cars – rail cars designed to carry molten steel – from Indiana Harbor.
Cliffs said it would be able to produce the same amount of hot metal using just one furnace because of operational improvements – including the use of more hot-briquetted iron (HBI) in its blast furnaces and more scrap in its basic oxygen furnaces.
Background
Goncalves said last week at the Tampa Steel Conference that Cliffs was considering idling a furnace because the increased use of HBI and prime scrap allowed the company to stretch the same hot metal production over fewer furnaces.
“When we make a move, we make a move. … You might see a blast furnace going down for good still in 2022,” Goncalves said during a fireside chat at the event.
And Cliffs won’t put idled furnaces up sale. “I hope you saw that the blast furnace in Ashland was demolished with explosives. We brought it down for good,” he added in reference to the Amanda blast furnace at the former AK Steel mill in Kentucky.
The No. 4 has daily ironmaking capacity of 4,900 tons. The No. 7 blast furnace – which Cliffs describes as its “flagship” – has daily capacity of 11,500 tons. That makes it the largest blast furnace in North America by a wide margin, according to SMU’s blast furnace status table.
The No. 3 furnace at Indiana Harbor was already permanently idled. And the mill’s No. 5 and No. 6 blast furnaces – decommissioned in 2015 under the ownership of ArcelorMittal USA – have since been demolished.
Cliffs in addition has a 100-day outage planned for roughly March to June at the No. 5 furnace at its Cleveland Works. Cleveland operates two furnaces, the No. 5 and No. 6, with a combined capacity of 8,500 tons per day.
As for prices, they have fallen precipitously in recent weeks. SMU’s average lead time for hot-rolled coil is less than four weeks – meaning that many mills might not be taking orders for April yet.
Reaction
CRU Principal Analyst Josh Spoores agreed that Cliffs would be able to produce similar amounts of steel with fewer furnaces.
“I think they are strategically brilliant. This change is further execution of their strategy of better utilizing raw materials to lower production costs and operate in a very clean and efficient manner,” he said.
But increased efficiency doesn’t come without some potential downsides.
“There is an increased risk in relying on only one blast furnace, yet they still have multiple other furnaces in Michigan and Ohio that might help to limit the cost of an unplanned outage,” Spoores said.
By Michael Cowden, Michael@SteelMarketUpdate.com

Michael Cowden
Read more from Michael CowdenLatest in Steel Mills
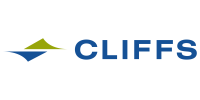
Cliffs unveils new hydrogen-powered stainless line in Ohio
CEO Lourenco Goncalves, flanked by state leaders and union reps, touted the project as proof that US manufacturing is not only alive, but also advancing.
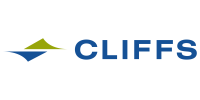
Cliffs idles Steelton, Riverdale, and Conshohocken operations
Cliffs has idled facilities in Riverdale, Ill., and Conshohocken and Steelton, Pa.
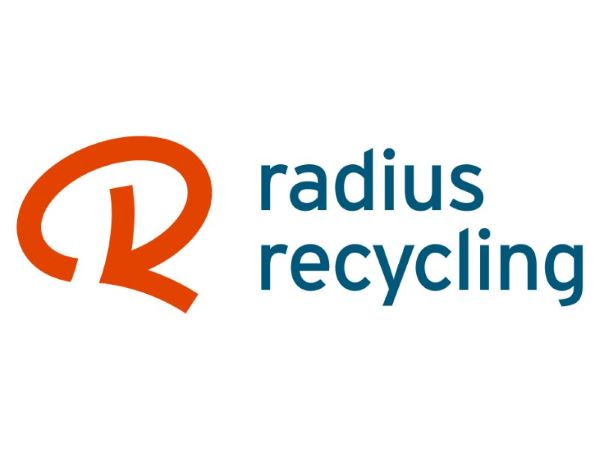
Radius loss narrows, volumes climb in ‘healthy’ West Coast market
Stronger steel demand in the Western US, rising scrap flows, and improved rolling mill utilization drove sequential gains for Portland, Ore.-based Radius Recycling.
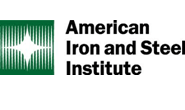
AISI: Raw steel production backs off multi-year high
US raw steel output edged lower last week after hitting a multi-year high in mid-June, according to the American Iron and Steel Institute (AISI).
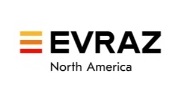
Private equity firm Atlas Holdings to acquire Evraz North America
Atlas Holdings said it has signed a definitive agreement to acquire Evraz North America (Evraz NA). The Greenwich, Conn.-based private equity firm said it expects the deal for the Chicago-based steelmaker to close in the second quarter of 2025 subject to various closing condition.