Steel Products
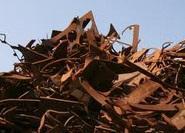
Scrap Insight: Scrap Optimization as a Hedge on Pig Iron Usage?
Written by Stephen Miller
October 6, 2023
Some of the movements in scrap and pig iron pricing over the past 18-24 months have been quite drastic. At the International Iron Metallics Association (IIMA) meeting Oct. 2-4 in Nashville, Tenn., there were several reports presented on them. The breakout of hostilities in Ukraine severely impeded the flow of pig iron from the Black and Baltic Seas to the US. US-based electric-arc furnace (EAF) mills relied on pig iron from Russia and Ukraine for low-phos material. In fact, this reliance grew to over 60% of all pig iron imports over the last decade at the expense of Brazilian grades. This was a very risky strategy as it turned out.
After the war broke out, US users of pig iron realized shipments from this region would end soon. What followed was panic buying of pig iron from Brazil, and to a lesser extent, India. Even China sold us a cargo. The price rose from the mid-$500s to over $1,000 per metric ton (MT) on a delivered to New Orleans basis. Not only did pig iron rise, so did the price of prime scrap, like #1 busheling and #1 bundles. The busheling price jumped to $800/MT from $525/MT in a two-month period in the Ohio Valley, according to the CRU scrap price database.
So, with these severely increased input costs facing EAF flat-roll mills, they started to change their melt mix in order to use less pig iron and less busheling. They met with some success and are still employing this practice today, despite the return of somewhat popular pricing to both pig iron and prime scrap. This is what they mean by scrap optimization. The mills did a commendable job, given the hand the were dealt (maybe by themselves!).
Some of the presenters at the IIMA put forth this strategy as a partial solution to rising input costs. However, I believe this is not solving the long-term problem of sourcing adequate low-residual inputs for the ever-expanding sheet-making capacity that has been installed, or soon will be.
The US mills will need more pig iron, direct-reduced iron (DRI)/hot-briquetted iron (HBI), and prime scrap to operate going forward. They will have to use higher residual grades as over 12 million tons of new capacity is either ramping up now or is planned over the next year or two. They will need pig iron and/or HBI to dilute the residual alloys present in the obsolescent, higher residual scrap grades. This new capacity figure does not include Canada. There both ArcelorMittal Dofasco and Algoma are switching over to EAF production. From where will all this additional prime melting stock be sourced?
There is no easy answer. Pig iron will be in short supply as the Russian material will likely not be available and Ukraine is very questionable. Brazil does not produce as much as they historically have in the past, as much production has been shuttered over the last two decades. Indian pig iron is being used internally or supplied into China and Southeast Asia. There are two pig iron projects underway domestically. U.S. Steel will produce 500,000 tons per year (TPY) at their Gary Works in Indiana, which will supply their EAF at Big River Steel in Arkansas. They also have plans to produce up to 2 million TPY at their Granite City Works in Illinois, but this is not final yet.
HBI can be imported, but the prices will have to rise since it generally must be shipped from overseas as production in the US is largely already spoken for. There is really no regular trade in merchant HBI into the US. It is only spot.
Regarding prime scrap, the situation is even bleaker. The US automotive industry may likely produce less prime scrap when the transition to EV’s takes hold. We import a great deal of prime scrap from Canada. However, when their conversion to EAF melting is complete, it is hard to imagine this scrap leaving for the US. The US mills also import cargoes of prime scrap from N. Europe. The feeling is this will continue, according to a presentation at the IIMA, providing the European Union does pass any radical restrictions, or does not use it themselves after their proposed conversion. Needless to say, there will be steep competition for the available prime scrap in the US.
So, despite the success in scrap optimization which has been accomplished recently, it will not solve the long-term problem looming on the scrap horizon.
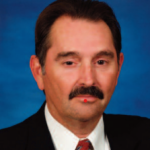
Stephen Miller
Read more from Stephen MillerLatest in Steel Products
CRU: Excessive global supply could hit rebar mill investments in US
Following the onset of the war in Ukraine in March 2022, concerns about import availability and expectations of rising demand from President Biden’s Infrastructure Bill pushed US rebar prices to record highs. In response, a flurry of new mills and capacity expansions were announced to meet the rise in demand from growth in the construction […]
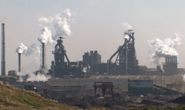
Steel buyer spirits tempered by soft spot market conditions
Steel sheet buyers report feeling bogged down by the ongoing stresses of stagnant demand, news fatigue, tariff negotiations or implementation timelines, and persistent macroeconomic uncertainty.
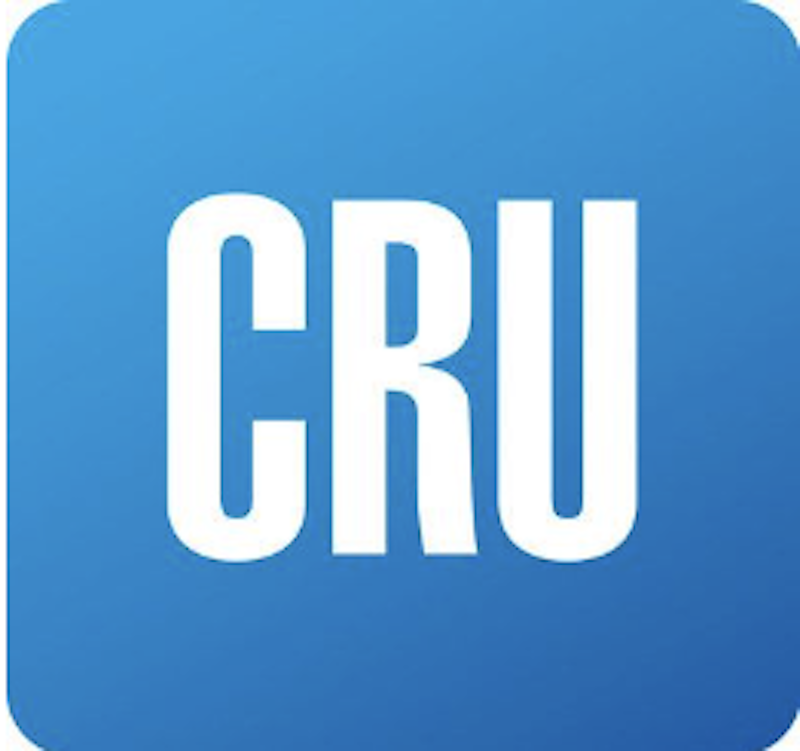
CRU: US stainless prices to rise on expanded S232 tariffs
Stainless prices in the US market will rise, following price increases by major US producers. Our base case scenario incorporates higher US prices in the near term, despite the initial negative reaction by the market. US stainless prices will go up in 2025 H2 and will stay elevated in 2026 as tariffs on stainless […]
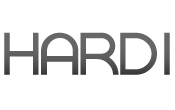
Galvanized steel demand unsteady amid lingering buyer fatigue: HARDI
Uneven demand for galvanized steel in June reflects a market that remains mired in uncertainty, according to industry sources.
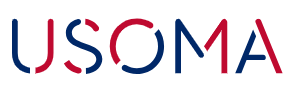
OCTG industry salutes Customs for catching trade crooks
The US OCTG Manufacturers Association is commending US Customs for intercepting another Thai company's attempt to illegally transship Chinese oil pipe to the US.