Features
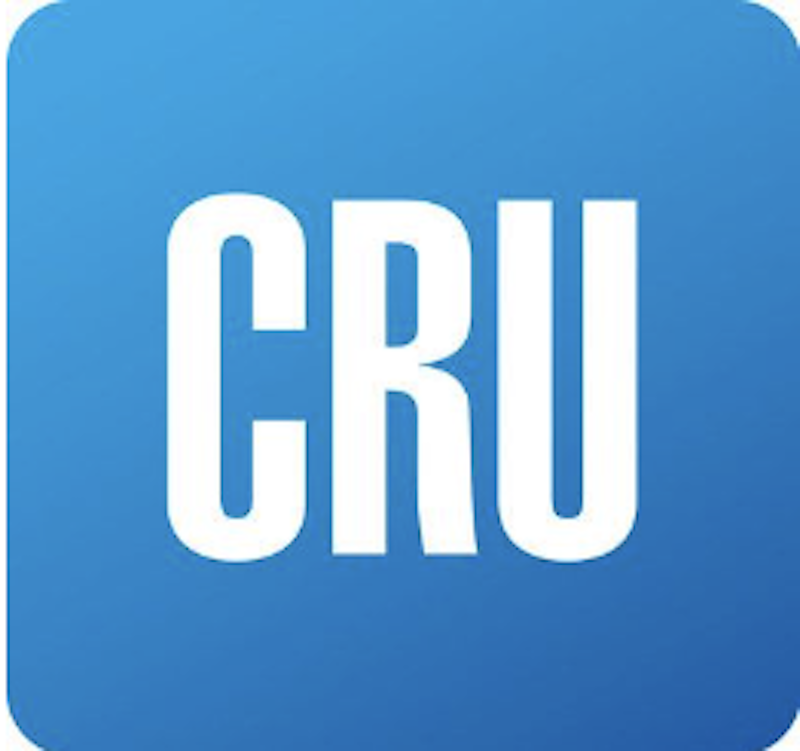
CRU: Electrical Steel – The Forgotten Material in Electrification
Written by Brian Schwadron
October 19, 2023
Much effort has been made in examining the supply chain of commodities related to electrification: everything from copper to aluminum to critical battery materials such as lithium, nickel, and cobalt. One overlooked material, however, is electrical steel.
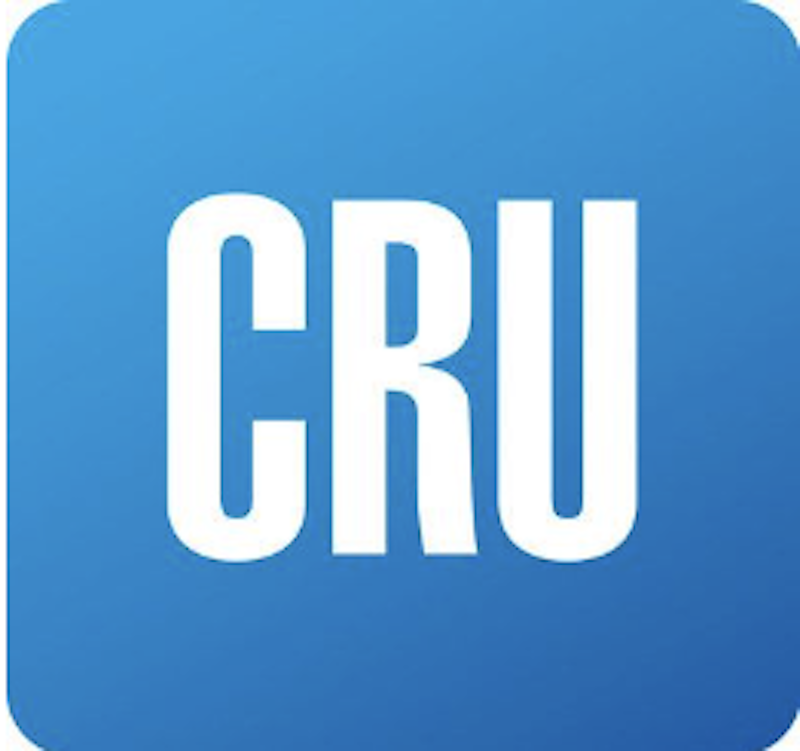
A small, niche segment of the steel industry – everything with a motor and every transformer contains electrical steel. Many questions have been raised regarding the capacity of steelmakers to produce sufficient volumes of electrical steels, particularly as increasing efficiency standards and more challenging applications drive the need for higher-quality, lighter gauge material. The high levels of required capex, combined with complex, somewhat secretive production methods (with some IP issues as well) and, finally, the potential for materials substitution with a new generation of amorphous steels, have left this segment of the market in flux.
In most applications, steels are selected on the basis of mechanical properties – yield and tensile strength, hardness, toughness, n-values, and so on. Although mechanical properties are also important for electrical steels, it is the magnetic properties that are the key differentiator. High flux density (permeability), which is the amount of magnetization produced in a material by an electric field, and low core loss, the amount of (unwanted) heat generated by an alternating magnetic field, are the most important attributes of electrical steel.
Electrical equipment with rotating parts (such as motors) require steels with isotropic (non-oriented) properties, such as fully-processed non-grain oriented electrical steel (NGOES) or semi-processed cold-rolled motor laminates (CRML, a product little seen outside of North America). Stationary electrical equipment (primarily transformers) utilizes anisotropic grain-oriented electrical steel (GOES), where proper texture and material alignment allow for significantly higher flux density in the rolling direction.
As transformers are the only major consumer of GOES, the market is significantly smaller for that product than for NGOES, at ~1/3 the demand.
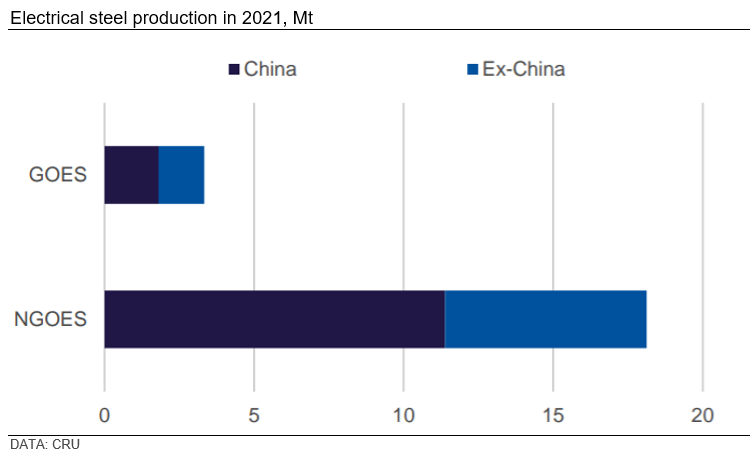
Electrical steels are high in silicon, which adds expense and complexity throughout the entire production process, including hot rolling, pickling, cold rolling, annealing, and temper rolling. The complexity involved in both materials’ development and production, combined with the relatively small size of the market, limits production of these products to a handful of advanced mills, which have seen little reason to increase capacity over the past five years. Expected increases in demand will support capacity increases for certain types of electrical steels over the next few years, but this is not the case for all types of electrical steels.
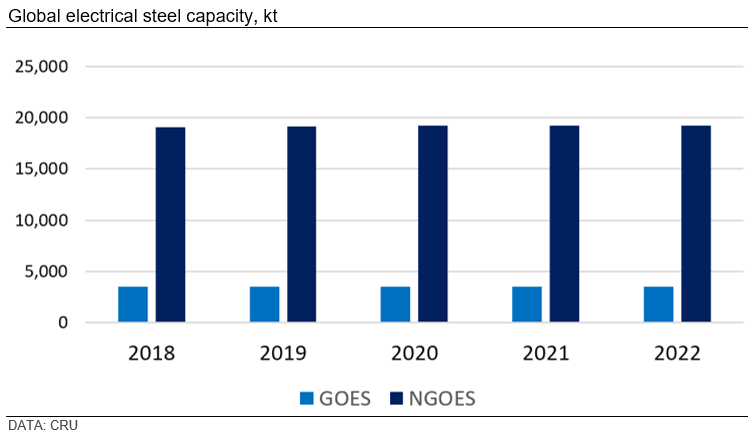
With this segment undergoing rapid change, CRU will continue to update our clients on developments on both the supply and demand side in the electrical steel space.
This article was first published by CRU. Learn more about CRU’s services at www.crugroup.com.
Brian Schwadron
Read more from Brian SchwadronLatest in Features
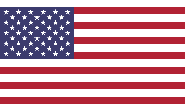
Holiday Notice: Fourth of July
SMU will be closed on Friday, July 4, with no Sunday newsletter on Sunday, July 6.
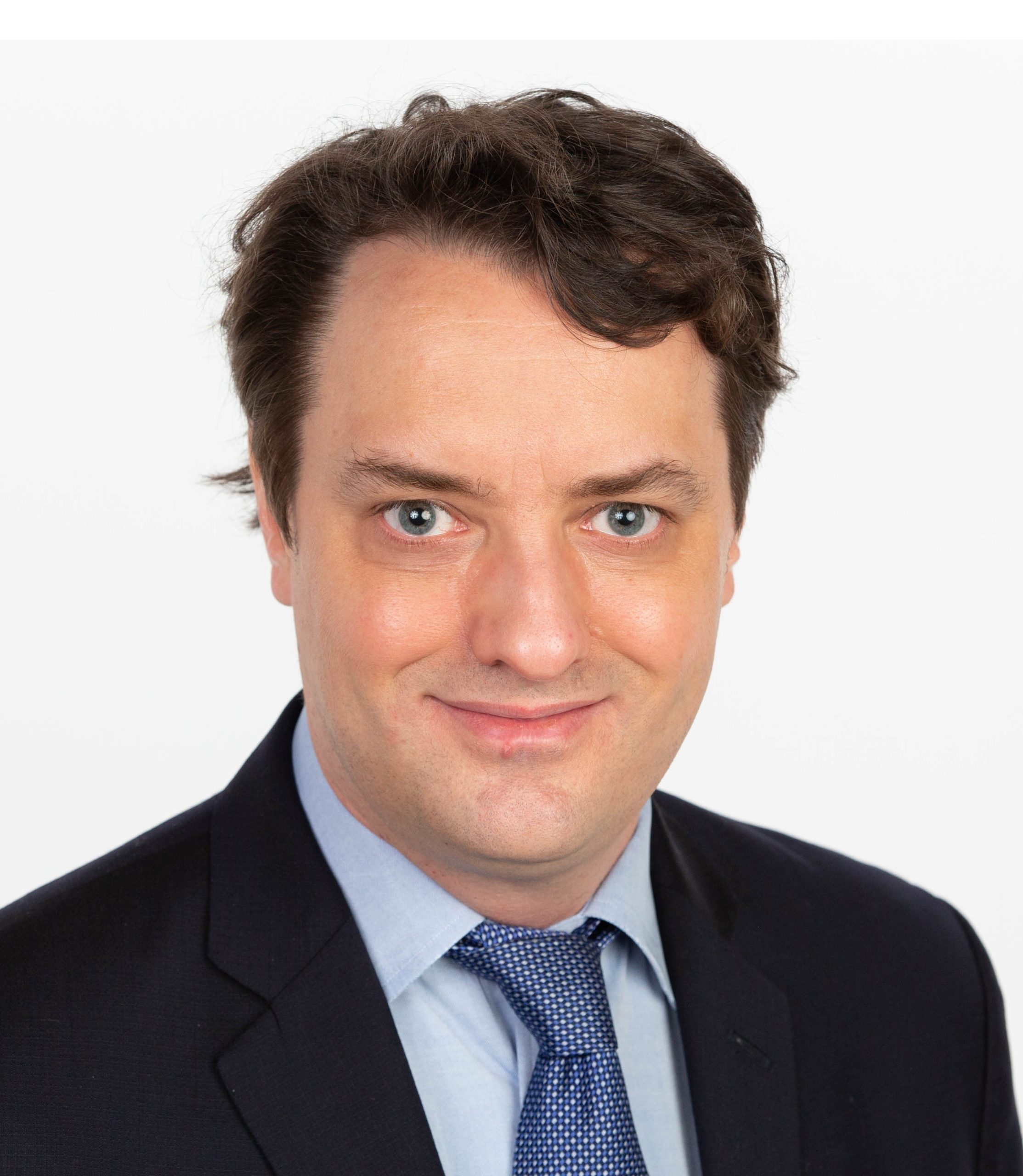
Final Thoughts
I’m not sure how many different ways I can write that it’s been a quiet market ahead of Independence Day. There are variations on that theme. I’ve heard everything from the ominous “eerily quiet” to "getting better" and even the occasional “blissfully unaware” (because I’m enjoying my vacation).
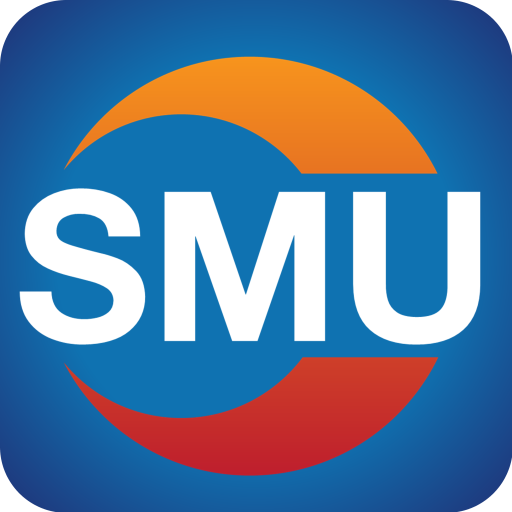
SMU’s Week in Review: June 30-July 3
It will be a shorter week as the United States celebrates Independence Day on Friday. But we won’t leave you high and dry.
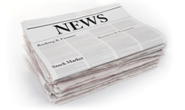
Steel groups welcome passage of budget bill
Steel trade groups praised the passage of the Big Beautiful Bill (BBB) in Congress on Thursday.
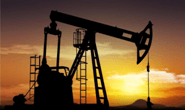
Drilling activity down further in US, climbs in Canada
The rig count declined for the 10th consecutive week in the US, while Canadian count rose for the fifth straight week, according to Baker Hughes.