Steel Mills
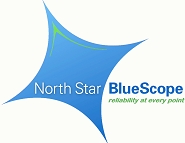
BlueScope: North Star Expands, Coronavirus a Concern
Written by Sandy Williams
February 25, 2020
North Star BlueScope reported weaker earnings in the first half of FY 2020 due to softer prices and margin spreads and normal seasonality. Sales revenue of $592 million was down 32 percent from the first half of 2019. Weaker hot rolled coil prices were partly offset by lower raw material costs. Shipments for the half declined 1 percent year-over-year to 1,028,000 metric tons from 1,074,000 tons in the previous half year. The mill has been operating at 100 percent capacity. Second half results are expected to be relatively unchanged from the first half.
The North Star BlueScope expansion is progressing well. The foundation and erection of the melt shop building is under way along with the tunnel furnace car foundations. The new administration building and warehouse are nearly completed. Mark Vassella, CEO of Australian parent BlueScope, notes that major OEM contracts have been negotiated and orders placed. Full ramp up is expected to take 18 months once the mill is commissioned in 2022. The 850,000 metric ton per year expansion will increase production in Delta, Ohio, to 3.0 million tons annually.
“The incremental installed melt capacity of 1.4 million equivalent metric coiled tonnes allows for further potential upside over time with further debottlenecking of the hot strip mill,” said BlueScope.
The Covid-19 virus has caused some supply disruption to equipment ordered for the Delta mill that is produced in Tianjin. Team members are working on alternative sources of supply to prevent any critical delays.
The addition of another EAF at North Star is consistent with the long-term trend toward EAF production in the U.S., said BlueScope. An estimated 3.65 million tons of HRC capacity (including North Star) is being added in the region. Additional capacity of 4.2 million tons will be added by Big River Steel and Steel Dynamics in the South. In addition, there have been several adjustments to BF production through idled operations. BlueScope expects supply and demand in the U.S. to be largely in balance by 2023.
“Underlying demand across our footprint is generally stable, however the economic impact of Covid-19 has created uncertainty for our Asian businesses and Asian steel spreads in the near term,” said Vassella. “The impact to U.S. Midwest spreads, if any, is unclear. We are aware of some impacts to our supply chains, which to date have been mitigated; we continue to monitor the situation.”
BlueScope reports that its China team members are safe and operations have reopened. The company has four major operating sites in China as well as a number of sales offices. The company is monitoring employee health and providing masks, gloves and health checks.
Production is lower as a result of reduced staffing due to quarantines, limited logistic movement and lower demand. Business in China was heavily impacted in February and similar conditions are expected in March. Rate of recovery in demand and activity remains unclear, said BlueScope.
The entry of HBI pellets to the Great Lakes region by Cleveland-Cliffs is a net positive for North Star, said Vassella. “What we actually need to do is get some product and put it into our process and test it to understand the carbon content,” he said. “We’re delighted with the Cliffs investment.”
BlueScope revenue of AUD $5.9 billion (U.S. $3.9 billion) was 8 percent lower than the first half of FY 2019 due to lower steel and export coke selling prices, which were offset by a favorable Australian dollar exchange rate. The company expects results in the second half of the fiscal year to be generally in line with the first half.
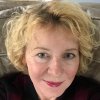
Sandy Williams
Read more from Sandy WilliamsLatest in Steel Mills
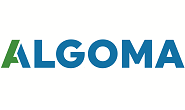
Algoma fires up EAF steelmaking with first arc
Algoma Steel reached a milestone in its transformation from blast furnace to electric arc furnace (EAF) steelmaking, with its Unit One EAF achieving its first steel production this week.
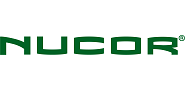
Nucor holds HR list price at $910/ton
Nucor is keeping its list price for spot hot-rolled coil unchanged after last week’s shortened holiday week.
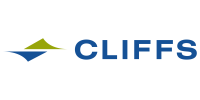
Cliffs unveils new hydrogen-powered stainless line in Ohio
CEO Lourenco Goncalves, flanked by state leaders and union reps, touted the project as proof that US manufacturing is not only alive, but also advancing.
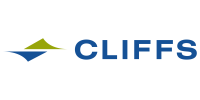
Cliffs idles Steelton, Riverdale, and Conshohocken operations
Cliffs has idled facilities in Riverdale, Ill., and Conshohocken and Steelton, Pa.
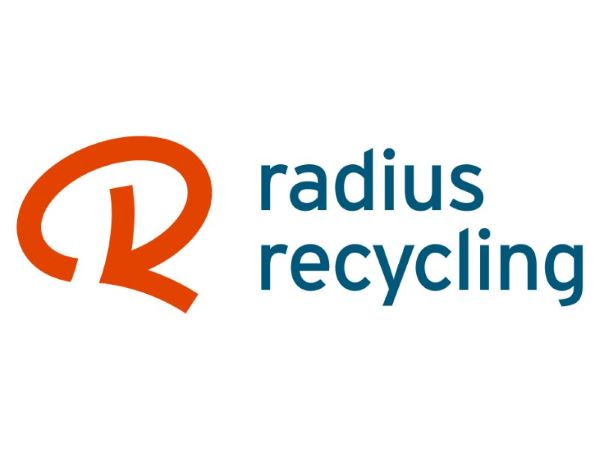
Radius loss narrows, volumes climb in ‘healthy’ West Coast market
Stronger steel demand in the Western US, rising scrap flows, and improved rolling mill utilization drove sequential gains for Portland, Ore.-based Radius Recycling.