Steel Mills
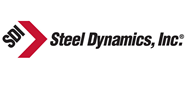
SDI aluminum project logs cost bump, but timeline holds firm
Written by Ethan Bernard
January 26, 2024
Steel Dynamics Inc. (SDI) faces rising costs for its Columbus, Miss., aluminum rolling mill. But the project timeline remains on track.
The total project cost, including the recycled slab centers, has risen to $2.7 billion, SDI co-founder, Chairman, and CEO Mark Millett said in a Q4’23 earnings call on Wednesday.
“The installation cost for the rolling mill has expanded due to inflationary installation costs that we are all facing,” Millett said. However, he added that with virtually all equipment and construction contracts complete, “we are confident in this final budget.”
SMU has reported that the project was originally slated to cost $2.2 billion. SDI revised the estimate upward to $2.5 billion in January of last year.
Millett noted, as previously reported, the project would be 100% funded with cash.
Operation details
The Columbus mill will be supported by two satellite recycled aluminum slab-casting centers, Millett said, with one in Arizona and another in central Mexico.
“Our plans are on schedule, the (aluminum) rolling mill should be mid-’25, the Mexico slab center at the end of ’24, and the Arizona slab center around mid-’25,” Millett said.
CFO Theresa Wagler said SDI believes capital investments will be in ~$2 billion for 2024, of which ~$1.4 billion relates to aluminum investments. She added that because of the investment size, SDI will have a separate aluminum segment broken out going forward.
Millett described the project itself as a 650,000 metric ton per year (mtpy) aluminum flat-rolled facility located in Columbus. Described as a “state-of-the-art plant,” ~300,000/mtpy of the output will be canstock; ~200,000 mtpy auto; and ~150,000 mtpy of industrial and construction products.
“Many customers have already indicated they would like to build facilities on our rolling mill site in Columbus, Miss., and this core location strategy provides a sustainably competitive model for all of us, conserving time, money, and reducing emissions across the supply chain,” Millett said.
Back to roots
He compared the market environment in aluminum to what SDI faced when it started in steel 30 years ago: “older assets, little reinvestment, heavy legacy costs with inefficient high-cost operations.”
“We can emulate the performance-driven, high-efficiency, low-cost model that drove our success in steel to drive superior financial metrics,” Millett said. He pointed out that the operations will employ ~750 people vs. “typically 2,000 or more in a similar competitor out there.”
Millett said SDI would leverage its OmniSource scrap subsidiary’s market position and separation technologies “to ensure higher recycled content.”
Likewise, president and COO Barry Schneider said SDI’s metals recycling team was also “partnering even more closely with both our steel and aluminum teams to expand our scrap separation capabilities through process and technology solutions.”
He said this would help mitigate potential prime scrap supply issues in the future. “It will also provide us with significant advantage to materially increase recycled content for our aluminum flat-roll products and increase the earnings opportunities.”
“If you put it all together, we’re confident that our earnings profile is going to be far superior to the industry today,” Millett said.
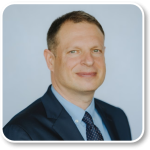
Ethan Bernard
Read more from Ethan BernardLatest in Steel Mills
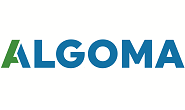
Algoma fires up EAF steelmaking with first arc
Algoma Steel reached a milestone in its transformation from blast furnace to electric arc furnace (EAF) steelmaking, with its Unit One EAF achieving its first steel production this week.
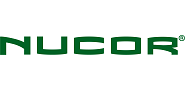
Nucor holds HR list price at $910/ton
Nucor is keeping its list price for spot hot-rolled coil unchanged after last week’s shortened holiday week.
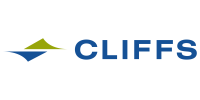
Cliffs unveils new hydrogen-powered stainless line in Ohio
CEO Lourenco Goncalves, flanked by state leaders and union reps, touted the project as proof that US manufacturing is not only alive, but also advancing.
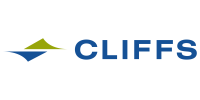
Cliffs idles Steelton, Riverdale, and Conshohocken operations
Cliffs has idled facilities in Riverdale, Ill., and Conshohocken and Steelton, Pa.
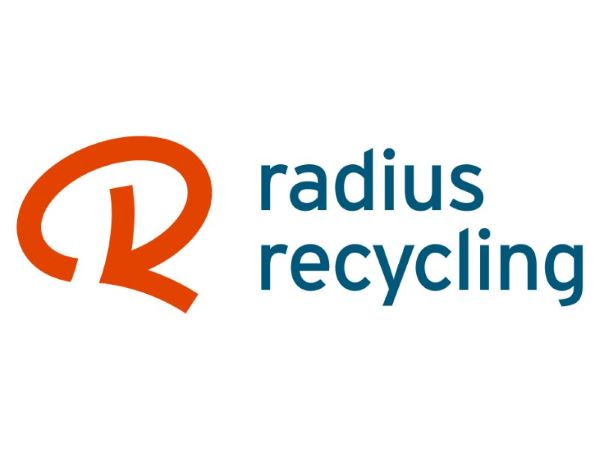
Radius loss narrows, volumes climb in ‘healthy’ West Coast market
Stronger steel demand in the Western US, rising scrap flows, and improved rolling mill utilization drove sequential gains for Portland, Ore.-based Radius Recycling.