Steel Markets
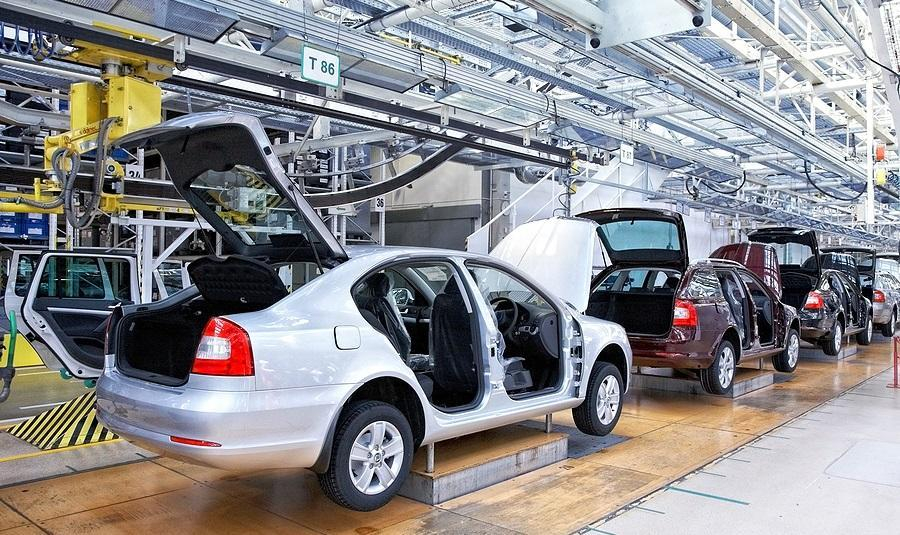
Chip Shortage Update: COVID Crisis in SE Asia Halts F-150 Production in U.S.
Written by Michael Cowden
August 27, 2021
Steel mills were supposed to see increased demand this summer as automakers ramped up production after putting the chip shortage in the rear-view mirror.
That might no longer be the case. And now the COVID-19 pandemic is complicating matters further.
Case in point: Dearborn, Mich.-based Ford Motor Co. is scaling back production of the F-150 pickup truck, the best-selling vehicle in the U.S.
Automakers typically try to protect their most popular and most profitable vehicles – think pickups and full-size SUVs – from the chip shortage and to idle production of them only as a last resort.
The reason for cutting F-150 production: The pandemic has hit Southeast Asia hard. And Ford sources chips from Malaysia, a company spokeswoman said in an email on Friday, Aug. 27.
The COVID crisis on the other side of the world has impacted three of Ford’s plants in North America, she said.
F-150 production at Ford’s assembly plant in Claycomo, Mo. – just outside of Kansas City – will be down the week of Aug. 30. And the automaker’s truck plant in Dearborn, Mich. – which also makes the F-150 – will operate on only one shift.
Also down next week is Ford’s assembly plant in Oakville, Ontario – it’s sole manufacturing facility in Canada. Oakville makes the Ford Edge SUV and the Lincoln Nautilus luxury car.
“Our teams continue making the most of our available semiconductor allocation, finding unique solutions to provide as many high-quality vehicles as possible to our dealers and customers,” the Ford spokeswoman said.
And Ford is hardly alone.
Its crosstown rival, Stellantis (formerly Chrysler), is also idling multiple plants next week “due to the unprecedented global microchip shortage,” a company spokeswoman said.
The Stellantis assembly plant in Belvidere, Ill., will be down the weeks of Aug. 30 and Sept. 6. And its assembly plant in Sterling Heights, Mich., will be down the week of Aug. 30. Belvidere makes the Jeep Cherokee SUV. Sterling Heights makes the Ram 1500 pickup truck.
North of the border, the Stellantis plant in Windsor, Ontario, will be down the weeks of Aug. 30 and Sept. 6. And the automaker’s operations in Brampton, Ontario, will be down the week of Aug. 30.
The Windsor plant makes the Chrysler Pacifica, Chrysler Voyager and Chrysler Grand Caravan minivans. Brampton makes the Chrysler 300, Dodge Charger and Dodge Challenger cars.
The semiconductor shortage is also impacting transplant automakers such as Nissan, which operates plants in the U.S. and in Mexico.
“We continue to make adjustments to our production schedules where needed. With the situation remaining extremely dynamic, I cannot make predictions on production for Q3 and beyond,” a company spokeswoman said.
Attendees at SMU’s Steel Summit in Atlanta earlier in the week were generally vey bullish. But some expressed growing concerns about the chip situation on the sidelines of the event.
One attendee noted that increased automotive demand following the initial outbreak of the COVID-19 pandemic had pulled hot-rolled coil out of the depths of sub-$500 per ton ($25/cwt) spot prices. And automotive could send steel prices back downward again should the chip shortage continue to weigh on auto production.
“Live by the sword, die by the sword,” he said.
Others noted that talks between some automotive parts suppliers and domestic mills had become contentious, with some saying they could not accept or pass through current high prices – and that other mills were willing to offer lower prices. It was not clear whether such comments were statements of fact, bargaining positions or both.
Hot-rolled coil prices stand at $1,915 per ton ($95.75/cwt). And some sources have reported spot deals as high as $2,000 per ton – or 4.5-times higher than a 2020 low of $440 per ton recorded last August.
While there is not immediate evidence of hot-rolled coil prices slipping, average hot rolled coil lead times have edged down from nearly 11 weeks in early July to a little more than nine weeks, according to SMU’s interactive price tool.
Lead times can be an advance indicator of price movements.
By Michael Cowden, Michael@SteelMarketUpdate.com

Michael Cowden
Read more from Michael CowdenLatest in Steel Markets
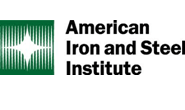
AISI: Raw steel production rises for second consecutive week
Domestic raw steel production ticked up again last week, now up to a three-week high according to the latest data released by the American Iron and Steel Institute (AISI).
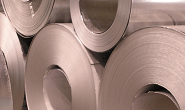
Wolfe Research’s Tanners cautions on sheet storm’s darkening clouds
Wolfe Research Managing Director Timna Tanners cautioned clients about the darkening clouds of a brewing steel sheet storm in the company's Basic Materials Weekly Webcast on Monday. “This one we’ve been talking about for a while, and we feel like the theme is coalescing here,” she said.
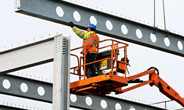
Dodge Momentum Index rebounds on surge of data center planning
A surge in data center project planning pushed the Dodge Momentum Index (DMI), a leading indicator for the nonresidential construction sector, higher in April.
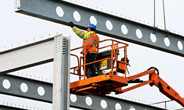
US construction spending levels off in March
Construction spending in the US in March was basically steady from the previous month but showed notable year-on-year (y/y) growth.
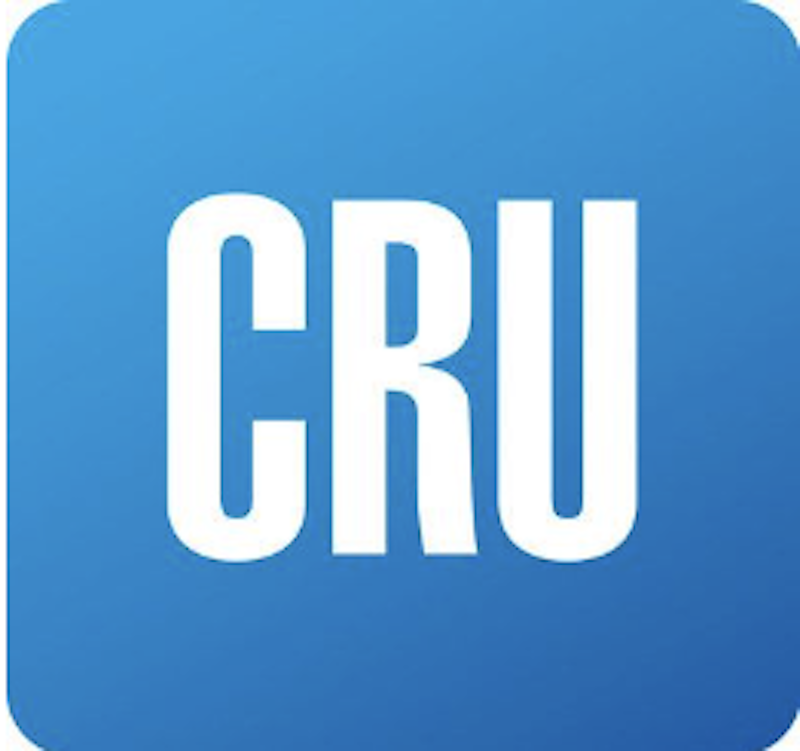
CRU: Brazil proposes quotas on steel imports, with tariff back up
Brazil’s chamber of foreign trade, Camex, has approved quotas on imports of 11 steel products and a 25% levy on shipments 30% above a product’s average import volume between 2020 and 2022.