Final Thoughts
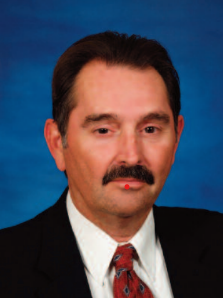
Final Thoughts
Written by Stephen Miller
May 1, 2025
The process of upgrading shredded scrap to reduce the copper content has been prioritized over the last several years. The abrupt rise in imported pig iron after the Russia-Ukrainian War in 2022 made this, what some consider, a worthy investment by steelmakers and their key suppliers.
Pig iron prices did normalize in 2023 and to a lesser extent in 2024. However, with the recent tariffs imposed on pig iron imports and those on direct-reduced iron/hot-briquetted iron (DRI/HBI), the upgrading of shredded scrap is back in the news.
Both pig iron and DRI/HBI play a significant role in flat-roll steel production in the US. The EAF producers of hot-rolled coil (HRC) rely on these two commodities to allow them to produce drawing-quality coils using available grades of ferrous scrap.
The pig iron and DRI/HBI are used to dilute the residual alloys, mainly copper, which are ever present in scrap.
Starting in the mid-1990s, the US mills have collectively imported between 4-7 million short tons (st) of pig iron per year.
The importation of this amount of pig iron comes at a stiff premium over domestic scrap. Many of the newer EAF mills were located in the southern US, and at the time, did not have economical access to the prime grades of #1 Busheling and Bundles, which were produced by northern-based automotive stamping plants.
This has changed somewhat with the building of transplant automotive plants in the South, but this region is still short prime scrap. Therefore, pig iron imports are critical.
In a recent earning report, Steel Dynamics Inc. (SDI) commented in response to a question about the increased pricing of pig iron.
They were going to rely on the sourcing of more prime grades of scrap and the upgrading of shredded scrap via the SHRED-1 technology.
SHRED-1 technology is the brainchild of Eriez Co, Erie, Pa. The SHRED-1 technology through advanced separation systems can reduce the copper content in shredded scrap from .30-.40% to levels between .16-.20%.
While this is a true upgrade, it still does not approach the lower levels of copper present in #1 Busheling, which are in the range of .02-.06%.
The question today with the increased costs of pig iron and DRI due to tariffs is: Can the technologies that have been installed in the shredding sector keep steelmaking costs from significantly increasing in the face of tariffs? Today, these are adding about $45 per metric ton (mt) to pig iron and $30/mt to DRI.
In a recent press release by Eriez, they celebrated the installation of its 50th SHRED-1 technology to the shredder community in the US. There are approximately 284 shredders operating in the country in 2025, according to Eriez.
So, although this technology has made progress, less than 20% of the shredded production can achieve the low-copper material. This has been significant progress.
In addition to mill operated shredders, several private scrap processors have also installed low-copper shredding equipment.
Scrap sources respond
In speaking with an executive for a Midwestern scrap concern with multiple facilities, he said his firm runs 20 shredders of which three have the SHRED-1 ballistic separation system.
According to this executive, the copper levels they have achieved are in the range of .17 – .18%. He said some other companies claim they have lowered their copper to .13%, but he doubts this can be duplicated without adjusting the feedstock to include material that is already low copper, and in only limited quantities.
He also confirmed the mill customers who they supply the lower copper shredded to pay a premium, but refused to elaborate.
However, another large multi-shredder operation doubts the lower levels can be achieved on a volume basis without including a portion of #1 Busheling and clips in the feedstock.
They have processed shredded scrap with equipment that reduces the copper content, but they will not guarantee copper levels below .20%.
Part of the problem is the separation equipment cannot remove copper, which is intrinsically contained in the scrap. But it does reduce the “free copper.” (“Free copper” is copper fragments that are not attached to steel or iron fragments after the feedstock is shredded.)
It seems these systems that are designed to reduce copper in shredded scrap can work best at mill-operated facilities where the system can be deployed near the furnace.
What is questionable is if there is enough supply of low-copper shredded being produced in the US to supply enough material to EAF steelmakers to reduce their reliance on pig iron or DRI to a meaningful extent.
We contacted SDI for comment, but did not receive a response by time of publication.
As the installed capacity of EAF steelmaking is on the rise, the competition for low-residual scrap and scrap complements will become more challenging. Can this technology provide an answer?
Also, it should be pointed out, shredded is estimated to be ~30% of scrap generation.
The other grades of obsolescent scrap, like #1 HMS, P&S, #2 HMS, Foundry Steel etc, are still a large part of scrap generation. Mills have to use these grades too. They all contain copper and other residual alloys and a portion of it is intrinsic.
The mills will continue to need pig iron and DRI to dilute these contaminants in order to produce the desired grades of steel.
It is not yet determinable whether the tariffs on pig iron, HBI/DRI and the materials that are imported to produce domestically made DRI/HBI will cause a significant increase in the price of EAF flat-rolled steel.
But it’s safe to say, the tariffs will raise production costs and may make the procurement of pig iron harder to source and more expensive.
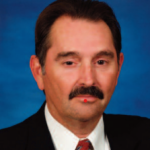
Stephen Miller
Read more from Stephen MillerLatest in Final Thoughts
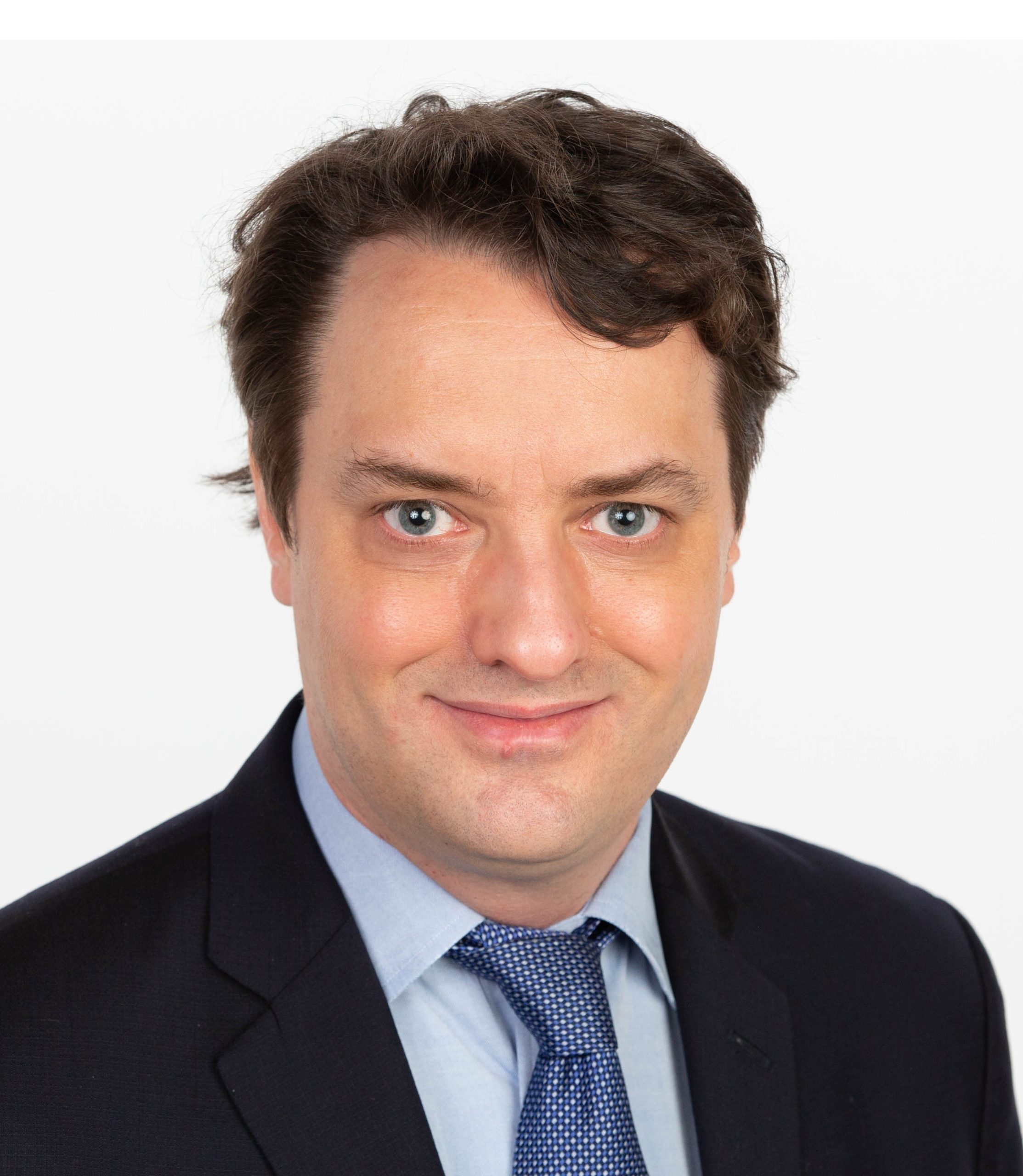
Final Thoughts
The big show is here again. SMU Steel Summit begins on Monday. This year, like last year, more than 1,500 people will be joining us. And I couldn’t be more excited to have everyone here in Atlanta.
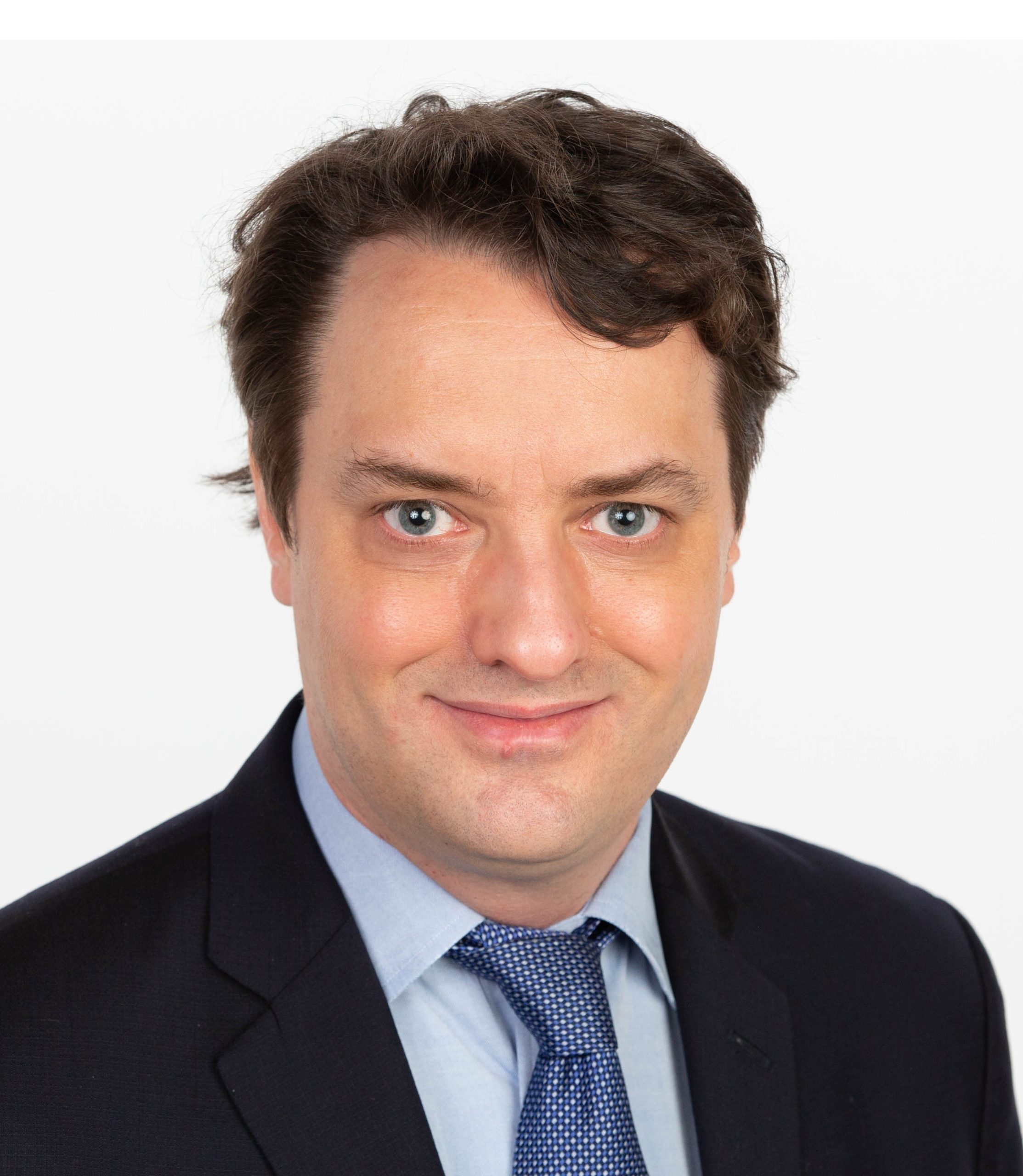
Final Thoughts
With SMU Steel Summit starting in just a few days, I decided to go back and do a quick check on where things stand now compared to the week before Summit last year.
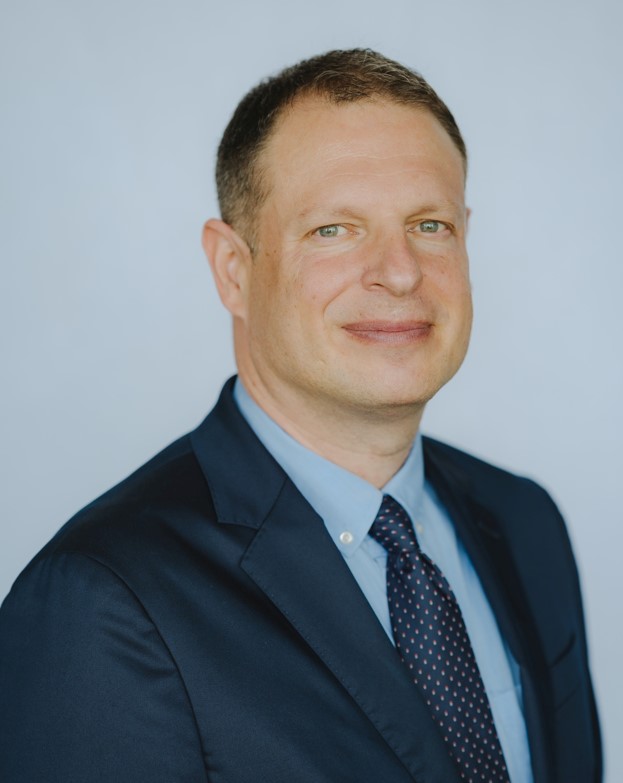
Final Thoughts
Is a pattern finally emerging in the post-Liberation Day tariff landscape?
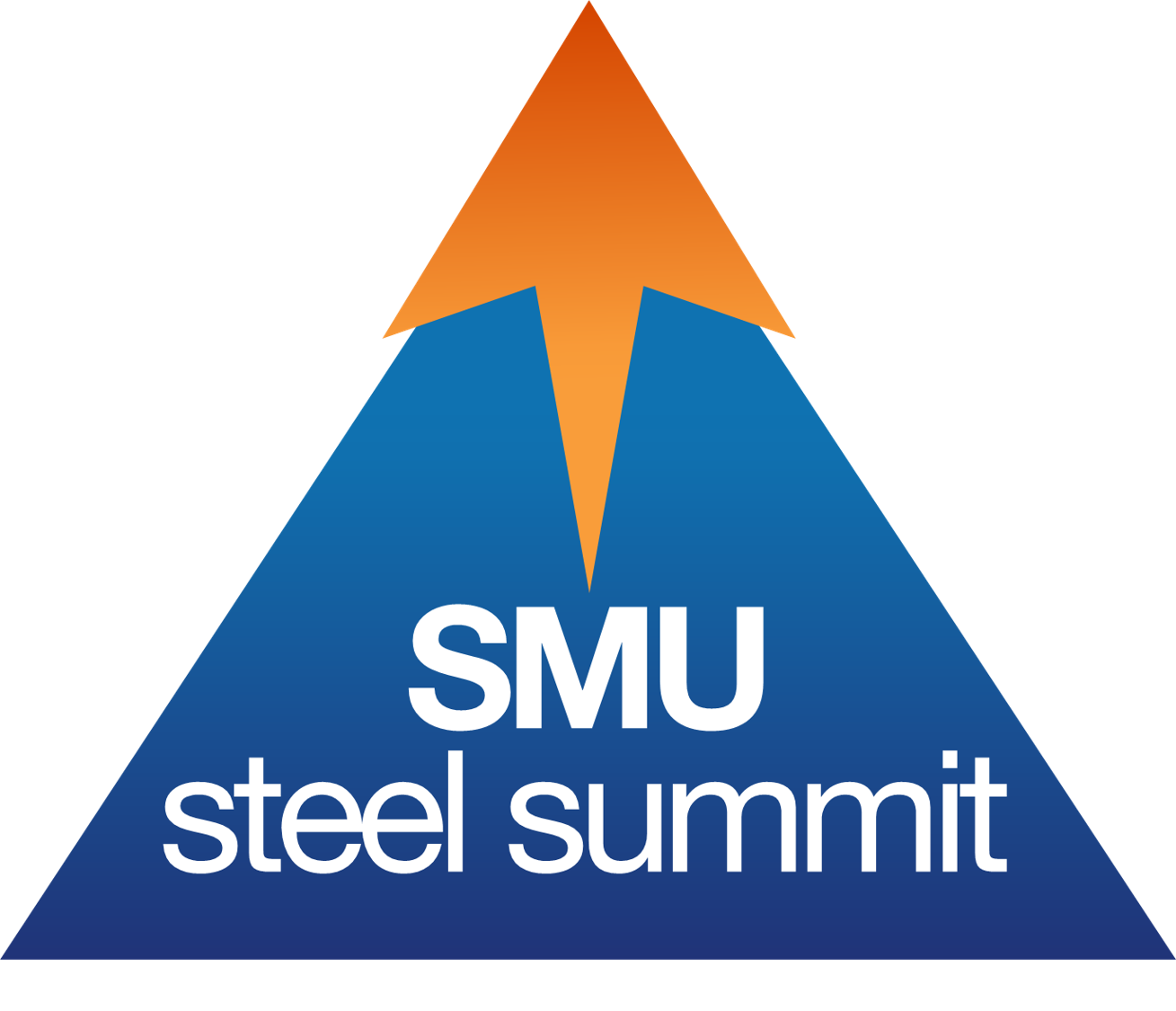
Final Thoughts
Don't be puzzled. Solve our crossword, and get ready for Steel Summit 2025!
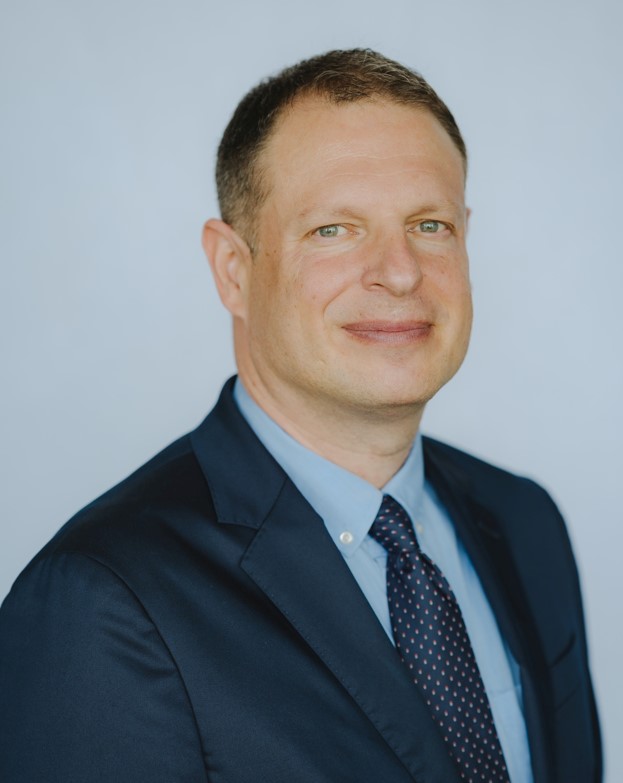
Final Thoughts
We're getting ready to initiate the 10-day countdown until Steel Summit 2025 in Atlanta. Liftoff is on Aug. 25, and the conference goes through Aug. 27. With the speed at which things have moved this year, it will be great to take a breath and reflect on what's happened so far.