Steel Mills
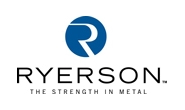
Last Three Months Have Felt Like Three Years, Says Ryerson CEO
Written by Sandy Williams
May 7, 2020
Ryerson CEO Eddie Lehner says the last three months have felt like three separate years due to the shock of the COVID-19 pandemic: BCV (Before the Coronavirus), DCV (During the Coronavirus) and ACV (After the Coronavirus).
After a slow start to January due to weak demand from OEMs, the quarter gave way to a “pandemic tidal wave which gripped China in January and February, exponentially spread, and paralyzed North America in March,” said Lehner. BCV and DCV were dedicated to implementing plans and policies to safeguard the health and safety of the workforce “while preserving liquidity and recovery capacity through the crisis interval and aftermath.”
The company reduced warehousing, delivery, selling, general and administrative expense by $8.0 million driven by reductions in staffing-related expenses. Workforce numbers were reduced by 16 percent. Ryerson hopes to bring staff back as conditions improve.
It is difficult to gauge demand “because we are not used to this kind of demand shock that is so unparalleled,” said Lehner. The company has seen customers reopening and then closing because there was not a sufficient backlog to sustain operations. OEM communications on reopening can be mapped right back to demand, said Lehner. “It is one of those times that if you follow the headlines you can get a pretty good beat on what is going on.”
“With respect to ACV,” he added, “we remain hopeful and determined that as we collectively accelerate learning about the virus and continue building virus response infrastructure to combat and eventually eradicate the virus, we will see societal and economic conditions normalize to the better side of current projections.”
North American April shipments trended 25 percent below March while the pricing environment held up better than expected given the rapid decrease in demand and already below average commodity prices, he said.
Ryerson shipments were up 4.6 percent from Q4 to 566,000 tons but down 8.6 percent on a yearly basis. Revenue totaled $1.01 billion, up 5.2 percent from the previous quarter but down 10.2 percent from the prior year. Net income was $16.4 million. Average selling price was $1,785 per ton.
Ryerson declined to provide guidance on the second quarter due to macroeconomic uncertainty and “overall lack of visibility into future demand trends, metal pricing and market conditions in the end-markets.”
Based on prior experience in recessions, Ryerson expects that demand will continue to retract in the second quarter, stabilize in the third, and economic growth will rebound from depression levels in the fourth quarter and continue into 2021.
There is a “risk of economic false starts where demand-driven and virus-driven business continuity cannot be re-established with any consistency,” added Lehner.
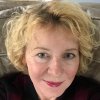
Sandy Williams
Read more from Sandy WilliamsLatest in Steel Mills
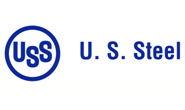
Steel Summit: Burritt says USS and Nippon are fast-tracking modern steelmaking
U.S. Steel President and CEO David Burritt told audiences at SMU's Steel Summit 2025 that the iconic American steelmaker’s partnership with Nippon Steel is fast-tracking smarter steel production.
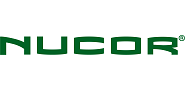
Nucor moves to stop HRC price slide with $10/ton hike
Nucor is attempting to halt the decline in hot-rolled coil prices with the announcement of a $10-per-short-ton increase in its weekly consumer spot price on Monday.
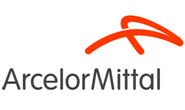
Explosion rocks ArcelorMittal’s DR plant in Mexico
ArcelorMittal reported a "strong" explosion at the direct reduction part of its massive Lazaro Cardenas mill in Mexico.
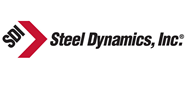
SDI to acquire remaining stake in New Process Steel
Steel Dynamics Inc. (SDI) announced that it has agreed to acquire the remaining 55% equity interest in New Process Steel.
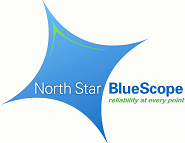
North Star results improve despite buyer caution as tariffs drive prices higher
North Star BlueScope said it is optimistic that US tariffs will bolster selling prices and tighten the spread the Australia-based steel maker suffered in 2025.